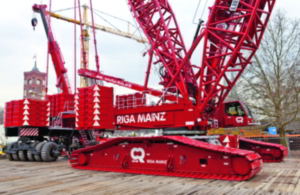
Tunnel drill work for Liebherr Crane
There is a gap of around 2 km in Berlin's underground network between the current stations at Alexanderplatz and Brandenburger Tor. The first trains are due to start running on this section directly beneath the historic city centre, in 2019. A tunnel drill measuring 74 m in length and weighing 700 tonne has now been assembled in the enormous construction shaft near the Red City Hall to excavate the first tunnels. The Herrenknecht drill was delivered in individual components to the site on barges sailing up the River Spree. A brand new Liebherr LR 1600/2 crawler crane from Riga Mainz took care of the unloading and hoisting work.
After around one week of preparation, the red crawler crane was ready for use on the river bank with its 72 m lattice boom and ballast trailer. The LR 1600/2 hoisted the individual components of the tunnel drill on to land during two night shifts from the edge of a temporary dock specially created for site logistics purposes. The heavyweight cargo had to be un-loaded at night on this section of river since it is extremely busy with excursion boats during the day.
Uwe Langer, Head of the Mainz-based crane specialists, ordered his new 600-tonne crane from the Liebherr plant in Ehingen with a ballast trailer. The heavy-duty crane was able to exploit the features of this optional equipment in full in this, its first site operation. For each hoisting cycle, the crane had to travel backwards around 30 m and then slewed through 120? to lower the load.
"Resetting, removing and refitting the ballast on a ballast pallet would have taken longer than the actual 14 hoisting cycles to move the components," says Langer.
The counterweight (in this case 350 tonne) can be left on the ballast trailer even when the load is not being hoisted. The crawler crane travels and slews on 12 giant wheels. The various components of the tunnel drill were lowered 20 m down into the construction trench by the LR 1600/2 over a period of two weeks. The heaviest machine components, the front plate, weighed in at 135 tonne.