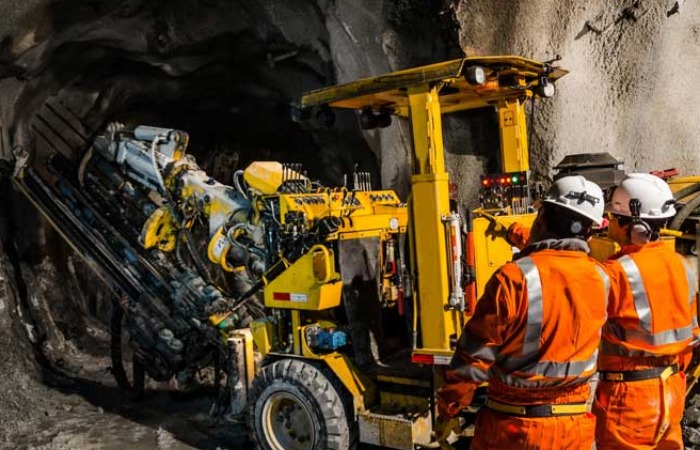
Mining Revolution
India, endowed with a wealth of mineral resources, has witnessed a significant transformation in its mining sector over the past few decades. Traditionally reliant on manual labour, the industry is now increasingly adopting mechanised operations, embracing a diverse range of technologies and automation. This article explores the evolution of the Indian mining industry, the driving forces behind mechanisation, and the impact of technological advancements on productivity, safety, and environmental sustainability.
Mining in India dates back thousands of years, with early records indicating the extraction of gold, copper, and iron. However, the modern era of mining began during British colonial rule when large-scale operations were established. Post-independence, India focused on self-sufficiency and infrastructure development, leading to a gradual increase in mining activities.
Despite the vast mineral wealth, the sector remained largely labour-intensive for many years. Workers used hand tools, and operations were manual, which limited efficiency and productivity. However, as the demand for minerals surged, driven by industrialisation and urbanisation, the need for more efficient and effective mining practices became evident.
Speaking on the trends in the mining equipment industry, Prasanta Ganguly, Head – OTR Marketing (Domestic Sales), BKT Tires, said, “The mining industry is increasingly focused on stability, performance, and comprehensive after-sales service. These trends are driving the need for tyres that offer superior durability and reliability to ensure consistent operations in extreme conditions. High-performance tyres are essential to support heavy mining equipment while delivering optimal load distribution, fuel efficiency, and extended life cycles. As mining companies emphasise stability, they require tyres that can minimise equipment downtime and maintain operational efficiency as well as safety.”
He added, “Additionally, after-sales service has become a critical factor for optimum tyre performance and end users looking for partners who provide continuous support through tyre performance monitoring, maintenance support at site, and prompt issue resolution. BKT addresses these trends by offering advanced tyre solutions equipped with smart technology for real-time performance tracking, ensuring optimal performance and stability while providing the comprehensive after-sales service that mining operations require.”
Yashvardhan Bajla, Director – Business Development, Taurian MPS, said, “The mining industry is experiencing trends like increased demand for efficiency and digitalisation. There’s a push toward electrification to reduce emissions, requiring equipment that’s both powerful and eco-friendly. Taurian addresses these needs with its Terratrak hybrid track-mounted units that offer efficient, emission-free operation. These crushers meet the industry’s demand for reduced environmental impact while also reducing operational costs by up to 80 per cent.”
Mining equipment outlook
The Government of India has allowed 100 per cent foreign direct investment in the mining sector and exploration of metal and non-metal ores under the automatic route, which will propel growth in the sector. The Government introduced Mineral Laws (Amendment) Bill, 2020, to open a new era in Indian coal and mining sector, especially to promote ease of doing business. The National Mineral Policy 2019 was launched for transparency, better regulation and enforcement, and balanced social and economic growth into the sector.
Said Arun Misra, CEO, Hindustan Zinc, “Mining companies play a crucial role in socio-economic development of the country. Over the last decade, the contribution of the Indian mining sector to the country’s GDP has not been more than 3 per cent. With focussed investment, the mining sector aims to contribute 7 to 8 per cent to the GDP, which could create around 25 million jobs in the country, directly and indirectly, and has the potential to propel GDP growth to more than 9 per cent. Thanks to technological revolution, the nature of mining is constantly shifting. At present, we are contributing to the growth and development of the sector and country at large by creating jobs for more than 22,000 employees currently working and have further created multiple opportunities for downstream and ancillary industries in and around Hindustan Zinc. Other than that, we are also transforming the lives of communities around our operational units through varied CSR initiatives of skilling the rural youth, sustainable farming practices for farmers, mobilising rural women through microenterprises and much more,” he added.
Said Rajesh Nath, Managing Director, VDMA India, “Mining would continue to play an important role in India. In actuality, mining accounts for 4 per cent to 5 per cent of our total GDP. Around 60 to 65 per cent of India's electricity still comes from coal. By 2025, the Ministry of Coal wants to expand coal production from its current level of 740 to 750 million tonnes to one billion tonnes. India is still one of the few nations in the world where mining is still a major industry. Because of this, even German businesses are optimistic about India.”
Push towards mechanisation
The liberalisation of the Indian economy in the early 1990s significantly influenced the mining sector. As foreign investment poured in and industries expanded, the demand for raw materials skyrocketed. This surge highlighted the limitations of manual operations, prompting mining companies to seek mechanisation as a means to enhance productivity and reduce costs.
Pune-based Trident International specialises in producing industrial tyres for mining equipment, material handling equipment, infrastructure equipment, and construction equipment. Shyam Gyanani, Co-Founder and Executive Director, Trident International, said Our concentration is on underground mining within the mining sectors’ tyres for LHDs, jumbo drills, etc. As you are aware, underground mining has its own unique quirks and working circumstances that set it apart from surface mining. As a result of the tight quarters and challenging terrain, operating in underground mines presents safety challenges. If a tyre fails in that setting, whether due to damage or premature manufacturing-related problems, it presents many difficulties. We developed solutions for the underground mining industry because of this.”
The advent of new technologies played a pivotal role in transforming the mining landscape. Equipment manufacturers began to develop specialised machinery tailored to the unique challenges of the Indian terrain and mineral extraction processes. Innovations such as automated drilling systems, hydraulic excavators, and advanced hauling equipment became integral to mining operations.
The Indian government recognised the need for modernisation within the mining sector. Various policy initiatives were introduced to facilitate mechanisation and technological adoption. The National Mineral Policy aimed to promote sustainable mining practices and enhance the overall efficiency of operations. Additionally, the introduction of the Mines and Minerals (Development and Regulation) Amendment Act sought to streamline the regulatory framework, encouraging investments in modern mining technologies.
Several Indian mining companies have successfully embraced mechanisation, serving as models for the industry. As one of the largest coal producers globally, Coal India (CIL) has invested heavily in mechanisation, introducing dragline excavators and continuous miners. This shift has led to increased output and reduced labour costs. Vedanta has implemented advanced technologies in its mining operations, focusing on sustainability. The use of automation and real-time monitoring has improved safety and environmental management. Tata Steel has integrated automated systems in its iron ore mining operations, enhancing productivity while prioritising worker safety and environmental compliance.
Challenges
Despite the numerous benefits, the transition to mechanisation is not without challenges. The initial costs of acquiring advanced machinery can be prohibitive, especially for smaller mining companies. Additionally, ongoing maintenance and training for personnel are crucial for maximising the benefits of mechanised operations. The shift towards mechanisation necessitates a workforce that is skilled in operating and maintaining advanced equipment. There is a pressing need for training programmes to equip workers with the necessary skills. Collaborations between mining companies, educational institutions, and government agencies can facilitate this transition.
While the government has made strides in streamlining regulations, certain bureaucratic challenges remain. Delays in obtaining permits and approvals can hinder the adoption of new technologies. A more transparent and efficient regulatory framework would further encourage investment in mechanisation.
Road ahead
The future of the mining industry in India is poised for further transformation with the continued embrace of automation. Technologies such as autonomous trucks, automated drilling systems, and AI-driven analytics are expected to become increasingly prevalent. These advancements will not only enhance productivity but also allow for real-time monitoring and decision-making.
Said Brad Higgings, General Manager Sales – APAC/EMEA, Austin Engineering, “As the global focus on sustainability intensifies, Indian mining companies are likely to prioritise environmentally friendly practices. This includes the use of renewable energy sources, waste reduction strategies, and responsible land reclamation efforts. Companies that invest in sustainable technologies will be better positioned to meet regulatory requirements and consumer expectations. As the mining industry continues to decarbonise and reduce emissions, we are providing products to assist in creating more sustainable mining operations. We offer lighter-weight products that require less steel in manufacture but are engineered to retain strength and limit wear. Our high-performance trays and buckets have a higher payload, reducing fuel, tyre wear and emissions per tonne of material carried.”
Internally, we concentrate on optimising steel usage across the business, meaning there is less scrap to recycle. We currently recycle 96 per cent of any waste we do generate across our operations globally. We are installing solar panels into our fabrication facilities where we can deliver renewable energy for manufacturing in the future.
To remain competitive on a global scale, India’s mining sector must continue to innovate. The integration of cutting-edge technologies and practices will enhance the industry’s reputation and attract foreign investment. Collaborations with international firms can also facilitate knowledge transfer and the adoption of best practices.
The mining equipment revolution in India marks a significant turning point for the industry. The shift from manual to mechanised operations has transformed the way minerals are extracted, improving productivity, safety, and sustainability. While challenges remain, the ongoing adoption of technology and automation presents immense opportunities for growth and innovation. As India continues to embrace these changes, the future of its mining sector looks promising, paving the way for a more efficient, safer, and environmentally responsible industry.