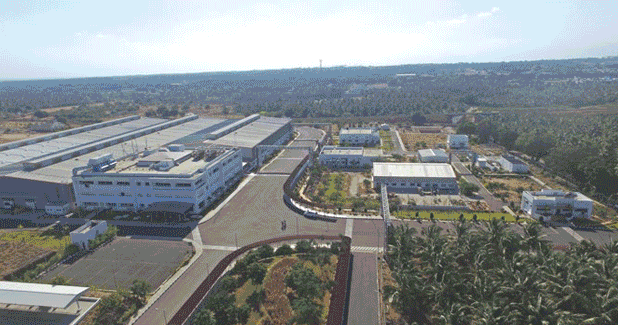
All Set to Leapfrog
From a position of being number seven currently, ELGi Equipments aims to become the second largest compressor manufacturer globally, in a decade. The Indian compressor giant is well on its way. A report based on the facility visit and interaction with the management.<p> Started in a humble way of manufacturing air compressors in 1960, ELGi Equipments has today transformed to become the seventh largest compressor manufacturer world over, with business presence in over 70 countries. The company has now set its ambitious goal of becoming the Number Two compressor manufacturer globally in a decade. In the last four years, after the completion and working of its sprawling 2,00,000 sq ft facility at the Kodangipalayam village in Coimbatore, ELGi can proudly claim that the foundation to reach its goal has been well laid. </p><p><span style="font-weight: bold;">Anvar Jay Varadaraj, Senior Manager - Marketing & Corporate Communications, </span>elaborates on the company's approach, 'Our mission is to establish the ELGi brand. Today with many companies giving technical details and characteristics of their products, we focus on a content-driven approach. Compressor works at the background, and the challenge is to make the customer understand how important are its reliability, power conservation, etc.'</p><p> <span style="font-weight: bold;">Global presence</span><br />ELGi does business in 70 countries with direct presence in 18 countries. The company has manufacturing units in India, Italy and USA, and has 200 distributors worldwide. The company has three subsidiaries: ATS ELGI Ltd, ROTAIR Spa, Italy and Patton's Inc, USA. A joint venture in the name of ELGi Sauer Compressors in India is an added asset. ELGi offers a complete range of air compressors from 1 HP piston to 2,000 HP centrifugal machines, with in-house technology to build futuristic products. It offers a vast range of over 400 compressed air systems - from the large centrifugal compressors to the world's smallest screw compressors. It operates four factories world-wide with the same high quality standards using its own air-ends. Over 15,000 air-ends and 40,000 compressors are produced in a year.</p><p> <span style="font-weight: bold;">The facility of global standards</span><br />ELGi has two factories in Coimbatore - the 20,000 sq m Singanallur facility for the final assembly line, and the Kodangipalayam facility, which includes the airends plant and the foundry. The young Kodangipalayam facility has technologically advanced imported machine tools to ensure the highest accuracy and quality standards. Both the general purpose machines and the special purpose machines are of highest quality. Recently ELGi has also started developing its own machines-for profile milling, grinding and polishing-which can do the same functions of the imported machines. This is aiming at bringing down the manufacturing cost, as imported machines are expensive though give high quality. So the company has decided to develop similar machines in-house without compromising on quality. At least half a dozen machines are already in use and more such machines are under preparation. </p><p>The airend units produced here range from 3 to 250 kg in weight while around 3,800 parts are also produced per annum. The tolerance level of each rotor profile unit is less than 10 microns.</p><p>The foundry adjacent to the airend manufacturing facility is another site of excellence in structure and facilities. 'Everything about the foundry is green, and even the wastage of of the sands that go for moulding is recycled as bricks,' says <span style="font-weight: bold;">KV Rao, DGM - Foundry,</span> who is passionate like all the managers while explaining the various features of the foundry. The foundry is equipped with best-in-class foundry equipment under one roof with minimum use of exhaustible natural resources, contamination of ambiance and facilitates to produce constantly reliable quality castings.</p><p>The furnace, moulding line and the casting fettling and finishing lines are noteworthy spots for conducive working and show great concern for safety and productivity. Says Rao, 'The foundry-grade sands are sourced from the country in processed condition and sometime high quality sands are imported from Saudi Arabia. The entire process is almost automated and is handled by a few workers with a shift of 7 am to 5 pm.' The Singanallur best-in-class conveyor assembly line with automated monitoring and testing stations has a capacity to produce 15,000 screw air compressors and 25,000 piston compressors. The company is in the process of getting its products certified by Compressed Air and Gas Institute (CAGI) of USA.</p><p>On the constant upgrading in quality of its products, <span style="font-weight: bold;">KSR Murthy, Director - Technology and Operations,</span> comments, 'We are doing so many journeys for quality improvement in the last few years and reached a stage of world class quality. Our motto is to invest ahead of demand.' ELGi spends about 3 to 3.5 per cent on R&D, and is equipped with an efficient design team to take care of the futuristic requirements. </p><p><span style="font-weight: bold;">R Jayakanthan, Director - Product, Systems & Strategy,</span> is proud enough when he comments on the privilege that ELGi enjoys in the compressor segment, 'Our core competency is building perfect compressors, and we have achieved this step by step over the years. Today, we stand among the best compressor manufacturers all over the world. We have learnt and applied as the journey progressed and today have reached the position among top players in the world. Besides, new markets have been explored abroad and captured.' </p><p>In the construction industry too, ELGi plays a dominant role in the supply of compressors. Not only that, it has explored and opened up new areas of applications in various sectors. With the economy opening up and segments like infrastructure taking its due place in the developments, ELGi is positive about the demand for compressors perking up in the coming years. ELGi is always in a state of preparedness with technological changes and demand matching such transformation.</p><p> <span style="font-weight: bold;">Going green</span><br />Green initiatives is a continuous process happening in this facility. <span style="font-weight: bold;">Arun Prasad, GM - Air Center and Foundry,</span> points out, 'Energy management system of course is one that we go for the second level of energy audit to certify the plant as the most green factory where we provide energy management systems, using solar power and monitoring and preventing energy wastage, etc. We have plans to set up roof-top solar plants for our energy needs, contributing to carbon credits. We also do transplantation of trees at the factory premises to bring down carbon footprint.' ELGi's foundry facility is the recipient of green foundry award by Institute of Indian Foundrymen for the year 2015-16. </p><p> <span style="font-weight: bold;">Export market</span><br />ELGi exports about 50 per cent of its compressors, of which more than 70 per cent goes to the western markets, mainly the US and Europe. It does business in over 70 countries having over 200 distributors and is actively present in 18 countries. This is no mean achievement. 'The challenge is to enhance the brand of our compressors globally, and get more pull in the market for ELGi compressors. Globally as we start selling compressors to big names like Johnson Controls, people turn their attention to our compressors. Our big competitors are in Europe or the US and hence the challenge to become No. 2 globally will be taken up without any compromise on any of our divisions,' comments Varadaraj.</p><p><span style="font-weight: bold;">Ramesh Ponnuswami, Director-India, South Asia, Africa and Middle East,</span> elaborates on the company's global market presence, 'Our technological capability is of very high order, and as we grow globally, we are prepared to meet many challenges. Today we are a force to reckon with in compressors within the country. India has a relatively small share in the global compressor market. The country has just 5 per cent of the $15 to $16 billion global compressor market. We are in the process of strategising and getting a lion's share in the total market. Our back-end is very strong. Now, with the global aspiration to be No. 2, we are working together towards achieving the goal collectively.'</p><p> <span style="font-weight: bold;">HR and training initiatives</span> <br />One of the cornerstones on which the strength of the company is built is the HR policies and culture. <span style="font-weight: bold;">Jayashankar Jayaraman, Director - HR,</span> explains, 'Our constant endeavour is to be inclusive where communications to everybody across the ELGi universe is common. The strength of our management policy lies in the fact that we have one policy from the lower rung of workers to the top level. This is a culture we have built over the years. We have even worked out how to fill the gaps, when some of our senior managers will be retiring in the next few years. Training the new breed to bridge the gap is already on.'</p><p>ELGi runs its own training school known as ELGi Vocational Training School (EVTS). The company focuses for underprivileged students of 10th and 12th pass with high marks to help them go for further education in EVTS. The school absorbs bright candidates for a three-year Diploma-equivalent course through test and interview. The selected students have been put on the course for three years through class room training and shop floor training. After successful completion of the course, they are inducted into the production lines as workers.</p><p>There is another training facility called Dexterity Centre at the Singanallur premises, to help enhance the ergonomic use of four motion principles of the operators during assembling the compressors. The training is intense and the graded system selects workers on their various capacities to be placed suitably. There is always continuity in training and retraining and the system is aimed at achieving higher levels of accuracy, speed and quality in assembling the components.</p><p> <span style="font-weight: bold;">Looking forward</span><br />When the company is looking forward to moving up in its market position, there are many challenges that lie ahead in the growth path. 'The biggest challenge for us is to create awareness about energy saving through compressors and also to find new applications. We do not want to sell just a product but a system that will contribute to the growth of the company,' says Varadaraj. </p><p>ELGi plans to leapfrog to Number Two position with the market shares in the country versus international from the present 50:50 going up to 20:80. Hence, most of the growth will be coming from outside and the inorganic growth will reach 70 per cent, according to Varadaraj. After consolidating its presence in Europe and Americas, some of the breakthroughs in ELGi's exports have happened in south-east Asian countries including Indonesia in the recent times. The journey to the 10x growth in the next decade has already begun in earnest and ELGi is well on its way to achieve this feat. </p><p> Five things to know about ELGi:<br /></p><ul><li>A legacy of manufacturing air compressors since 1960</li><li>One of the five companies in the world to design and manufacture proprietary oil-free air-ends</li><li>Half of its revenue from outside India and 60 per cent of its international revenue from Europe and America.</li><li>Offers over 400 compressed air systems from the large centrifugal compressors to the world's smallest screw compressor.</li><li>Over 100 years of engagement with varied technologies and industries.</li></ul><p> <span style="font-weight: bold;">- Sudheer Vathiyath</span></p>