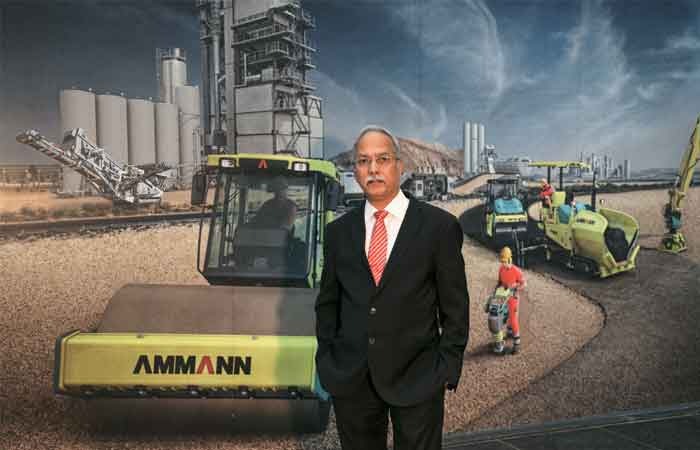
Ammann has scaled up production with a range of 11 models of asphalt plants
What is the current demand trend for asphalt mix in India? Which are the major demand drivers for asphalt mix?
The infrastructure and construction sector especially the road sector has witnessed rapid growth during the past few years primarily Government both at the state and center realising the importance of building a strong road network thereby boosting the economy. Every year, we have witnessed the Government focus to lay 20 km/day to 40 km/day, and rising investments in infrastructure in India are boosting the growth of the asphalt mix demand.
Furthermore, economic growth is driving governments to focus on improving public infrastructure, which is a major end-user segment of the asphalt mixing plants market. Moreover, the rising sale of commercial and passenger vehicles is an indirect indicator of the positive outlook for the global asphalt mix demand. This is because more vehicles mean more sustainable roads would be needed, and since road construction is more on flexible pavements where asphalt mix is predominantly the main ingredient. All this demand has given boots to a petroleum refinery, which is the source of raw material for asphalt mix.
Another major impetus has been given to connectivity of major district roads, resurfacing of roads, strengthening of existing roads, and road expansion of various projects from 2 lanes to 4 lanes to 6 lanes and so on. All these projects are driving the current demand for asphalt mix.
How do you look at the demand trend for asphalt plants? Which type and capacity are in demand?
The growing economy, urbanisation, government spending on public infrastructure, rising sale of commercial and passenger vehicles, improved logistics, and raising the scale of the status of roads – state, highways, super expressways, and village roads are key growth drivers for asphalt mix plants.
Further road renewal, strengthening, extension depending on the traffic density (MAL) induces the type, capacity, and processes, which primarily is used, to derive the longevity of roads and highways, which is only accomplished by asphalt plants. The size of the project with JMF (recipe) helps in zero in the type of asphalt mixing plants - batch mix, continuous and cold mix.
Several key trends are to the fore in the asphalt plant sector offering solutions that meet the demands of projects, as well as customer needs. These asphalt plants can meet varied job demands required for projects that may be featured with RAP (hot or cold), foam bitumen, liquid additives, SMA, plastic additions, and so on.
The need for asphalt plant mobility, ease of transport, and faster commissioning has also increased the demand for compact plants – that fit in standard shipping containers and can be trucked to the site. These generally come ready fitted with electrics to be installed without much difficulty.
With Government focus on green roads and highways creating a great demand for emission-free asphalt plants suitable for construction, road maintenance, etc.
Ammann has scaled up its production with a wide range of 11 models of asphalt plants ranging from 60 TPH to 260 TPH offering complete flexibility to the customer’s demand.
What are your latest products and solutions in asphalt plants?
Ammann AAG, Switzerland with 150 years of its incorporation having core competence in mixing plants has revolutionised the Globe with its innovations and offering the latest advancement in technology, emissions, and processes.
Product innovation: Sometimes, an entirely fresh approach is needed to meet challenges both new and old. Ammann’s advanced engineering team has a history of creative and innovative thinking.
Zero waste system: With continuous asphalt-mixing plants, the first and last few tonnes of every shift are waste. Ammann team of experts developed a patented solution that ensures all mix has the proper percentage of larger aggregates and fines from the very start to the very end. The creative solution prevents the mix from going into the scrap pile.
RAH100: The RAH100 counterflow dryer enables new asphalt mix to be made with up to 100 percent RAP. Essential to the RAH100 is its gentle heating process. The process is unique in itself connecting two sections. One is a hot gas generator that contains a burner and forces air toward the second section, which is a counterflow dryer.
Comprehensive recycling solutions: There are a variety of recycling solutions for Ammann customers ranging from 30 percent, 40 percent, 60 percent, and 100 percent. Recycling can also occur at Ammann asphalt-mixing plants through cold RAP up to 30 percent, recycled material can go directly into the mixer, meaning any plant from Ammann is capable of utilising that percentage of RAP.
Alternative fuels: Ammann has developed asphalt-mixing plants able to burn new, renewable energies – and to even convert waste into fuel. Biofuels, such as rapeseed and sugar cane, support climate protection and lessen dependency on mineral oil. Tall oil, which is a waste product of sulphate cellulose production, can be used, too. Ammann biofuel burners can also use more traditional fuels such as natural gas, LPG, light, and heavy oil, and kerosene.
Manufacturing: A commitment to sustainability is also apparent at Ammann’s manufacturing facilities throughout Europe, South America, China, and India. Modern machinery and streamlined processes minimise energy needs and lessen emissions, while lean practices conserve valuable natural resources.
Some of our latest technology in Ammann plants includes cold mix technology, warm mix, reclaimed asphalt, waste plastic addition, and in-situ polymer modified bitumen manufacturing plant and emulsion plant.
What are the key features offered in your plants?
Ammann plants are equipped with the latest technology features aimed at offering total flexibility to customers. Just to highlight one key difference in Ammann that puts its plants ahead of most other competitors, the complete control systems in Ammann plants are equipped with microprocessor control, which is 1,000 times faster than PLC control systems offered by most of our competitors.
For example, our computerised control burner ensures a very fast response thereby enhancing fuel economy. Besides, each sub-assemblies are designed to outperform offering increased reliability.
Thanks to AS1, a proprietary control system with software from Ammann provides fully automated mix production, plus the flexibility to work in safe manual mode. The system offers a host of other benefits including the use of unlimited recipes, automatic burner control, dynamic in-flight correction abilities, and full integration of electrically heated bitumen storage tanks. It also enables
- Locking of silo loading based on bin content to prevent material from being mixed up
- Composite or individual adjustment of the feeder proportions during production
- Production list for successive processing
- Automatic optimisation function for aggregate-to-bitumen ratio
- Dynamic switch point from coarse to fine batching
- “On-the-fly” recipe change
- Automatic batch reduction during the warm-up phase
- Automatic loading bin control
- Remote maintenance access and online diagnosis
Such advanced technologies in our plants help our customers to achieve high-quality mix, energy, and fuel savings, and high reliability, thereby improving productivity and TCO.
What are the eco-friendly features in your equipment range?
Eco-friendliness and sustainability are at the forefront of everything we do. Some of our initiatives that we have taken towards this are
- Maximise safe and sustainable manufacturing practices while building green plants and machines
- Develop asphalt-mixing plants that maximise the use of recycled materials
- Provide plants and machines that reduce emissions beyond the stated requirements
- Expand the use of alternative, eco-friendly fuels
- Utilise advanced technology to help plants and machines operate efficiently, minimising fuel burn and emissions
- Reduce the volume of oils and other fluids needed for operation, thereby lessening disposal requirements, too
- Partner with eco-focused packagers and transport services
- Other technologies include recycled asphalt up to 100 percent and cold mixing of asphalt
How do you see the importance of using recycled asphalt (RAP) in road projects? Do your asphalt plants support RAP?
Technological advancements have a substantial impact on businesses. Ammann core team works closely on a few projects thereby standing to its commitment to its stakeholders “productivity partnership for a lifetime”. This advancement in technology values high within Ammann thereby all our plants are based on the basic mantra of efficiencies thereby enhancing productivity and quality, reducing emissions, or saving fuel consumption. Besides, the technologies focus has been to have products user-friendly and have intuitive tools that help operators leverage the investment.
Ammann has had a presence in the asphalt plant industry for more than 150 years, even before the advent of recycled asphalt, low-temperature mixes, or automatic control systems.
Talking about recycled asphalt, we find sustainability has been part of the roadbuilding conversation for decades. Yet improvements that make the methods and machines more environmentally friendly continue to gain momentum. Industry leaders in road paving, increasingly see green practices as not only a way to better the world, but a tactic to improve profitability, too. For example, conversations about “green” roadbuilding always start with the use of recycled asphalt (RAP). We should not categorise RAP as waste material. It is a perfectly fine substitute for virgin materials thereby saving huge natural resources. The aggregates in reclaimed asphalt show little aging and are mechanically and geometrically within the quality ranges of new material. Our Ammann technology allows the use of RAP percentages up to 100 percent resulting in the biggest reductions in indirect CO2 emissions.
In one of our deployments with GR Infra projects in India, we are currently delivering up to 60 percent RAP first-of-its-kind in India.
What are the key challenges you face in the current market scenario?
The challenges faced are universal across industries. Largely skilled manpower – operators and engineers were not trained to use advanced technology.
Ammann India has set up “AMMANN ACADEMY” where we have set up different level courses to train operators for customers. Ammann India has gone the extra mile by taking initiative along with IESC and training more and more operators.
Proactively Ammann trained all the after-sales engineers across India and developed simulators for plant operations. Ammann India provides training to the operators through our after-sales team, immediately after the commissioning of plants.
Not too many years ago, smaller contractors saw the technology as something meant only for larger businesses. Small users were less likely to pay for “experimental” technology that would require lengthy training and, as some initially believed, few quantifiable benefits.
Improved telematics once again changed that by providing hard numbers on fuel and labor savings, passes avoided, and a host of quality control efforts. Those matter every bit as much to the small contractors.
The percentage of smaller contractors using the technology is rising, and that number will continue to grow. Governments are slow to adopt change, but some are beginning to require the use of this technology. It eventually will become the norm when bidding on job sites, whether you are a large or small contractor.
The other challenges are largely around the burgeoning cost of raw materials such as steel and copper. They are exponentially rising and the Indian customers are finding it difficult to cope up. It will be great if the government could intervene through policies and rationalise the price of steel and copper.
How do you look at emerging demands/opportunities for asphalt plants?
Ammann has great insight for India as one of the emerging markets where opportunities are enough which has been backed by the Government through various schemes NIP investment of $1 trillion in infrastructure.
Perceiving this Ammann has developed a state-of-art-the-art manufacturing facility in India to cater to all Indian customer needs and as well for the outside market. In short, I can say Ammann has built up a significant manufacturing capacity to suffice emerging demand.
Words like “productivity,” “technology” and “versatility” are pervasive and permeating, which is why Ammann machines are so commonly utilised on job sites of all shapes, sizes, and applications. Technology is not new to the road-building industry. However, if you look back, and then forward, you will realize we are in the midst of a technological revolution that will benefit those who embrace the changes – and leave behind those who do not. If this revolution could be described in a single word, it would be “data.” More Jobsite information is being gathered, stored, documented, and analyzed than ever before. If we were able to add a bit more description beyond “data,” the phrase “real-time” would be most appropriate.
We have hard information on what is happening right now. That knowledge enables Jobsite adjustments that lead to better machine utilisation, reduced fuel consumption, and dramatic quality improvements.
The associated cost savings are enormous, and those who do not take advantage of the opportunities will increasingly be unable to compete in the construction industry.
Ammann being a global company and a customer-centric organization, we always believe in having our customers at the center of everything that we do, such as continuous improvement processes and inventing new technologies aimed at addressing their operational issues and reducing their total cost of ownership.
The industry will witness substantial demand from economies all over the world, but emerging economies will play a major role in this.
Some of the vital trends that will promote the growth of the Asphalt plants market are listed below:
- Maximum usage of RAP
- Retrofitting
- Remote Maintenance access and Online diagnosis
- Mobile and Modular Plants offering ease of trucking and installation
- Fuel saving
- Trained manpower
- Dependable After-sales service
- Swift availability of genuine spare parts
At Ammann India, we are fully geared up on all the above and thus we believe our customers will have exciting times ahead with our technology-enabled plants.