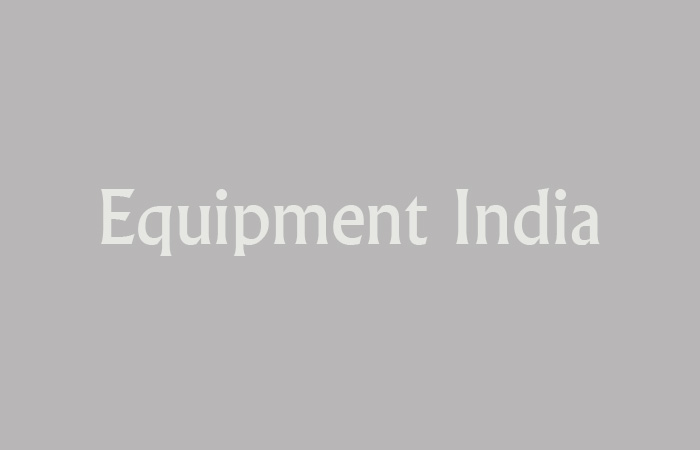
Atlas Copco India scores high on employee competency and training set-up
Hydropower alone had fuelled the growth of underground drill and blast tunnelling equipment for the last two decades in India, yet the last couple of years has shown a steady decline in such projects. Bhutan has accelerated the growth of such projects because of the ease of clearances and land acquisition. How?ever, the gap is very well managed by underground rail road projects in the north and north-eastern parts of India. Strategic crude cavern projects and lift irrigation tunnels have upped the demand for underground equipment to a new high. Anirban Sen, Business Manager, and Debabrata Sain, Marketing Manager, Underground Rock Excavation, Atlas Copco share the current trends in tunnel constru?ction, especially on automation, with Equipment India. Excerpts from the interview.
What are the core competencies and strength of Atlas Copco with regard to the sophisticated equipment manufactured and supplied for DBM?
Users today do not look at the vendor?s equipment first. They look at competency of people in sales and service organisation, logistical setup for spare parts and rock tools. Customers want to be doubly assured of the competency of the local service and appli??cation organisation before investing in automated machines. Atlas Copco India scores very high on competency of employees and training set-up assisted with simulators, which makes them the tunneller?s first choice.
What is the overall market size for drill and blast tunneling equipment?
The overall market size of drill and blast tunneling equipment is estimated to be around Rs 2-3 billion.
How do you assess the automation that is happening in tunnel construction, especially the use of computer based control systems?
Atlas Copco offers automated boom control with CanBus-based rig control system for precise hole drilling. Precision is the basis of quality tunnelling. When the foundation is sound, the building blocks only make the structure robust. Drilling is the first activity in DBM which sets the foundation for a good tunnel quality and speed. The cornerstone of Atlas Copco?s success with automation is the introduction of CanBus system very early in the late 90s and continuous development thereafter. To add to the strength is the inherent strength of Atlas Copco to retain qualified competent engineers who has contributed enor?mously to the success of automation. The customer is benefitted by means of reduced overbreak, thus saving enor?mously on the concreting and shot?creting costs and better assured advance per blast. At this moment, Atlas Copco India has been able to bring down the overbreak to the level less than 10 per cent in Class III & IV geology and is still working to improve the quality further. Automation has given customer the possibility to foresee the rock hardness and fracture frequency well in advance by means of ?measure while drilling? software plotted in graphical format in different colours.
Do the inadequate investigations in the complex geological strata at the project report preparation stage have any bearing on Atlas Copco as an equipment and machinery supplier and service provider?
The DBM method has been proven a very robust method in tunnelling thro?ugh Himalayan geology. With the acceptance of modern tunnelling met?hod like NATM, DBM has become safer, faster and controllable. Atlas Copco has made the boomers versatile by deve?loping kits like IRIA (Integrated Rotary Injection Adapter), Female Shank for SDA installation, pipe roofing kits for 89 mm and 114 mm for Eccentric and Concentric drilling system. With the ingenious capability of the automated boomers to not only probe-drill well in advance but also analyse the same and provide precise output of hardness and fracture frequency, reduces the necessity of well-defined geological chainage in DPR.
In the drill-and-blast method, what are the major product lines offered by Atlas Copco?
Atlas Copco has products for most of the activities in DBM tunnelling. Boomers for drilling, radial bolting, forepoling; Swedvent ventilation systems, hagg?loaders for continuous and fast loading, matching high capacity Mine trucks for hauling, chargetec emulsion charging equipment, scaletec for scaling after blasting, diesel locomotives with shuttle cars for rail-bound tunnelling system for small diameter tunnelling.
With the infusion of private equity into hydropower and railroad tunnels, customers are opting for automation in drilling to have better tunnel quality, less damage to the surrounding rock, savings on overbreak and therefore concrete cost.
How do you ensure that the lead time is reduced considerably for equipment like jumbo drills / road headers and computerised boomers?
The lead time of boomers has been reduced considerably by standardisation. This is a continuous process and Atlas Copco is in the forefront by taking proactive approach in manufacturing keeping into account project movement. To ensure better deliveries on compu?terised machines, help from consultants, developers are solicited to have the same in tender documents.
Brief us about the additional equipment and service support provided to clients.
Handholding customers on compu?terised machines is being done very actively. Investment in a simulator based in Pune speaks itself for the seriousness of Atlas Copco India on the training needs of operators for computerised machines.
What about the training facilities for these highly sophisticated equipment and machinery?
Atlas Copco India had recognised the need of a training facility for the expa?nding fleet of equipment in early 2006. In 2007, an integrated training-cum-refur?bishment centre was set up in Pune which is on the same premises as the distribution centre. Our aftermarket team publishes a training calendar every year for customers. In 2010, with the surge in computerised machines, Atlas Copco India decided to invest in simu?lators for boomers. Apart from imparting in-house training, this simulator has been transported to far-flung remote locations for convenience of the customer to train their operators. Atlas Copco organises classroom training for customers for their people at site and these training prog?rammes are tailored to suit customers? requirement.
What is the range offered by Atlas Copco in underground drill rigs in the tunnel construction?
Atlas Copco offers single-boom drill jumbos to four-boom drill jumbos for tunnel construction. These machines cover cross sections from 6 sq m to 206 sq m delivering 120 to 500 drill metre per hr.
Brief us on unique feature to ensure safety in the range of products meant for tunnel construction?
All Atlas Copco equipment is loaded with safety features to confirm to various international norms and certification. One of the unique features on our fully automated computerised boomer is the prevention of access to the front when the machine is in full auto mode. No sooner does a person or object cross the front console than the machine stops automatically.
What are the major challenges Atlas Copco faces as an equipment supplier?
Delivery and price. Atlas Copco India is trying to cope up with this very demanding customer requirement from time immemorial and will strive to live with this.
How do you assess the performance of the last two quarters and how do you look at the growth prospects of this fiscal?
As we said earlier, hydro projects are a major stumbling block at this moment. Delayed clearances are taking its toll. Other underground construction seg?ments like railroad, irrigation and crude caverns are on track. Last two quarters has been to our expectation and we hope that our government does its bit to come out from the state of inertia.
What are the core competencies and strength of Atlas Copco with regard to the sophisticated equipment manufactured and supplied for DBM?
Users today do not look at the vendor?s equipment first. They look at competency of people in sales and service organisation, logistical setup for spare parts and rock tools. Customers want to be doubly assured of the competency of the local service and appli??cation organisation before investing in automated machines. Atlas Copco India scores very high on competency of employees and training set-up assisted with simulators, which makes them the tunneller?s first choice.
What is the overall market size for drill and blast tunneling equipment?
The overall market size of drill and blast tunneling equipment is estimated to be around Rs 2-3 billion.
How do you assess the automation that is happening in tunnel construction, especially the use of computer based control systems?
Atlas Copco offers automated boom control with CanBus-based rig control system for precise hole drilling. Precision is the basis of quality tunnelling. When the foundation is sound, the building blocks only make the structure robust. Drilling is the first activity in DBM which sets the foundation for a good tunnel quality and speed. The cornerstone of Atlas Copco?s success with automation is the introduction of CanBus system very early in the late 90s and continuous development thereafter. To add to the strength is the inherent strength of Atlas Copco to retain qualified competent engineers who has contributed enor?mously to the success of automation. The customer is benefitted by means of reduced overbreak, thus saving enor?mously on the concreting and shot?creting costs and better assured advance per blast. At this moment, Atlas Copco India has been able to bring down the overbreak to the level less than 10 per cent in Class III & IV geology and is still working to improve the quality further. Automation has given customer the possibility to foresee the rock hardness and fracture frequency well in advance by means of ?measure while drilling? software plotted in graphical format in different colours.
Do the inadequate investigations in the complex geological strata at the project report preparation stage have any bearing on Atlas Copco as an equipment and machinery supplier and service provider?
The DBM method has been proven a very robust method in tunnelling thro?ugh Himalayan geology. With the acceptance of modern tunnelling met?hod like NATM, DBM has become safer, faster and controllable. Atlas Copco has made the boomers versatile by deve?loping kits like IRIA (Integrated Rotary Injection Adapter), Female Shank for SDA installation, pipe roofing kits for 89 mm and 114 mm for Eccentric and Concentric drilling system. With the ingenious capability of the automated boomers to not only probe-drill well in advance but also analyse the same and provide precise output of hardness and fracture frequency, reduces the necessity of well-defined geological chainage in DPR.
In the drill-and-blast method, what are the major product lines offered by Atlas Copco?
Atlas Copco has products for most of the activities in DBM tunnelling. Boomers for drilling, radial bolting, forepoling; Swedvent ventilation systems, hagg?loaders for continuous and fast loading, matching high capacity Mine trucks for hauling, chargetec emulsion charging equipment, scaletec for scaling after blasting, diesel locomotives with shuttle cars for rail-bound tunnelling system for small diameter tunnelling.
With the infusion of private equity into hydropower and railroad tunnels, customers are opting for automation in drilling to have better tunnel quality, less damage to the surrounding rock, savings on overbreak and therefore concrete cost.
How do you ensure that the lead time is reduced considerably for equipment like jumbo drills / road headers and computerised boomers?
The lead time of boomers has been reduced considerably by standardisation. This is a continuous process and Atlas Copco is in the forefront by taking proactive approach in manufacturing keeping into account project movement. To ensure better deliveries on compu?terised machines, help from consultants, developers are solicited to have the same in tender documents.
Brief us about the additional equipment and service support provided to clients.
Handholding customers on compu?terised machines is being done very actively. Investment in a simulator based in Pune speaks itself for the seriousness of Atlas Copco India on the training needs of operators for computerised machines.
What about the training facilities for these highly sophisticated equipment and machinery?
Atlas Copco India had recognised the need of a training facility for the expa?nding fleet of equipment in early 2006. In 2007, an integrated training-cum-refur?bishment centre was set up in Pune which is on the same premises as the distribution centre. Our aftermarket team publishes a training calendar every year for customers. In 2010, with the surge in computerised machines, Atlas Copco India decided to invest in simu?lators for boomers. Apart from imparting in-house training, this simulator has been transported to far-flung remote locations for convenience of the customer to train their operators. Atlas Copco organises classroom training for customers for their people at site and these training prog?rammes are tailored to suit customers? requirement.
What is the range offered by Atlas Copco in underground drill rigs in the tunnel construction?
Atlas Copco offers single-boom drill jumbos to four-boom drill jumbos for tunnel construction. These machines cover cross sections from 6 sq m to 206 sq m delivering 120 to 500 drill metre per hr.
Brief us on unique feature to ensure safety in the range of products meant for tunnel construction?
All Atlas Copco equipment is loaded with safety features to confirm to various international norms and certification. One of the unique features on our fully automated computerised boomer is the prevention of access to the front when the machine is in full auto mode. No sooner does a person or object cross the front console than the machine stops automatically.
What are the major challenges Atlas Copco faces as an equipment supplier?
Delivery and price. Atlas Copco India is trying to cope up with this very demanding customer requirement from time immemorial and will strive to live with this.
How do you assess the performance of the last two quarters and how do you look at the growth prospects of this fiscal?
As we said earlier, hydro projects are a major stumbling block at this moment. Delayed clearances are taking its toll. Other underground construction seg?ments like railroad, irrigation and crude caverns are on track. Last two quarters has been to our expectation and we hope that our government does its bit to come out from the state of inertia.