404
Page Not Found
We're sorry, we seem to have lost this page,
but we don't want to lose you
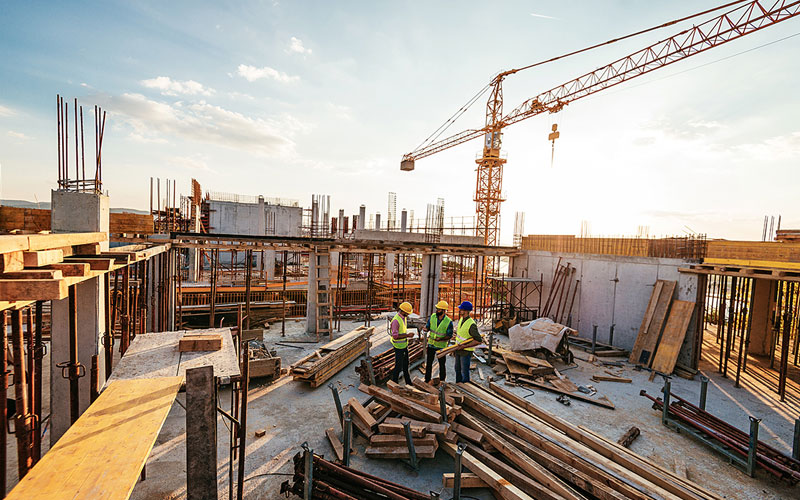
Construction News
Construction World publishes daily construction news, latest infrastructure developments, recent infrastructure projects and timely ...
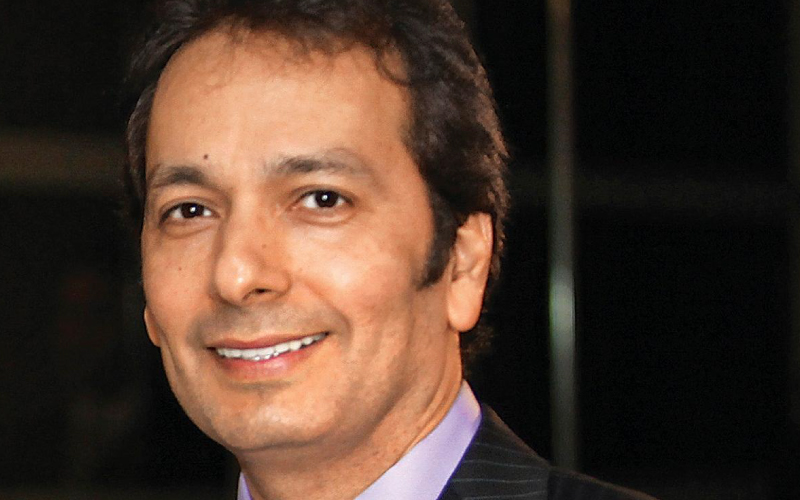
Opinion
Construction World presents opinions shared by Architecture & Construction Industry leaders about the latest construction news, trends etc.
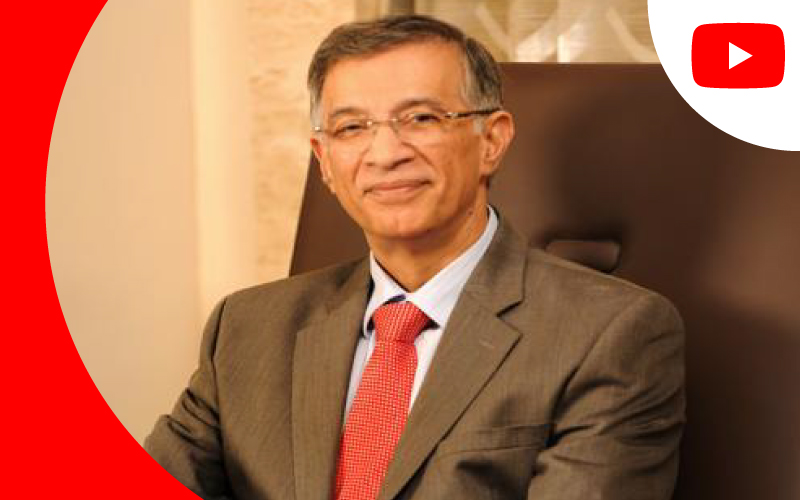
Video Interviews
Watch Video Interviews of Construction Industry Experts