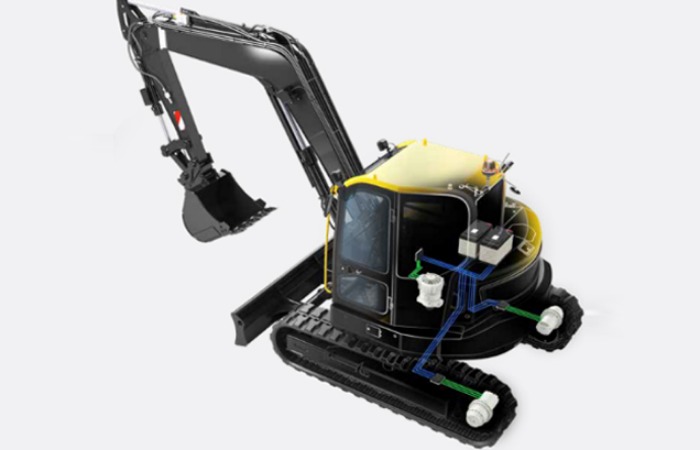
Bonfiglioli India: Winning through product innovations & tech
Bonfiglioli is a market force with its presence spanning in 22 countries. The company makes the most of geographic proximity to offer world-class power transmission and drive solutions by having a relentless commitment to excellence, innovation, and sustainability.
Bonfiglioli India started in year 1999 to develop solutions dedicated for Indian market. With Three manufacturing Plants (two in Chennai and one in Pune), a Global R&D centre and pan India service network Bonfiglioli India is leading towards continued product leadership. In India, the company created breakthrough solutions that integrate the most advanced mechanical, electrical, electronic, and hydraulic technologies to meet the most demanding Indian application requirements. The team research on creating new solutions for Bonfiglioli’s traditional markets of wind, mobility and industrial drives segments. Apart from the traditional markets, Bonfiglioli also focuses on new technologies with IIOT and electromobility segment. The company’s focus is not just about making in India but innovating in India for India and for the worldwide markets.
The R&D team has several research programmes in hybrid and electric technologies providing energy efficient solutions for the electromobility segment and construction equipment markets. For every new product launch, the company uses market intelligence and real-time application know-how with its rich technical expertise. This involves collection of micro to macro level technical detailing where our engineers study end-to-end application details. This team works very closely with OEMs and a detailed study is performed along with the end user of the equipment. The team spends a lot of time with end user for understanding the usage of the equipment and data acquisitions are performed which helps in defining the specifications for product. The defined product undergoes various calculations, analysis and tests based on application study and real time data.
Focus on CE industry: Widest range of products
Bonfiglioli has been enhancing construction equipment performance, efficiency, productivity, and reliability for more than 40 years. Experienced with the world’s major players, our team of experts create, design and produce advanced technology solutions for a wide range of applications, such as excavators, drilling machines, building cranes, milling machines and many others. The range of products, including planetary drives, drum drives, track drives, slew drives and winch drives, is perfectly tailored to meet a broad variety of specifications and is making us global leader in this industry.
Electric powertrain and drive solutions for E-Mobility
The future of mobility is going to be electric and Bonfiglioli is committed to develop innovative and futuristic power train solutions for the growing E-mobility market. The company has been working over the years to provide electric solutions for various types of machines like forklifts, airport tow-trucks, material handling equipment, e-cars and autonomous vehicles, etc., wherever a custom solution is required, manufacturers can benefit from Bonfiglioli’s technical expertise.
Bonfiglioli IIOT technology
The trend towards intelligent, connected products has already started and will be used increasingly. The use of additional sensors increases the ability for diagnosis and thus reduces machine downtime. Smart, connected products offer exponentially expanding opportunities for new functionality, far greater reliability, much higher product utilisation, and capabilities that cut across and transcend traditional product boundaries
Bonfiglioli already started this initiative, and its dedicated team is focused on the connected products also successfully installed on some applications, which are working in the field now
Innovative drive designed in India for girder transporter used in high-speed rail project
In a significant milestone, Bonfiglioli India won the project to supply wheel drives (Bonfiglioli’s 600W drives) for girder transporter vehicles. These vehicles will be used for the Mumbai-Ahmedabad high-speed rail line project considered one of the biggest infrastructure projects in India until now. The 508 km long Mumbai-Ahmedabad bullet train project is one of the leading infrastructure projects envisioned by the Government to take the level of mobility to international standards thereby bringing about a paradigm shift in the perception of transport in our country.
Trains are expected to run at a speed of 320 kmph. A large part of this high-speed rail link will be on elevated tracks composed of many girders. These girders will be the largest one’s ever made in India and could weigh as much as 1,100 metric tonne, evaluation of this massive load carrying on the 600W Bonfiglioli wheel drives was one of the major simulation analysis which was performed by Bonfiglioli India.
Transporting these giant girders to the site required special girder transporter vehicles. One of the main systems for these vehicles is wheel drives, which were designed by Bonfiglioli considering the various operating conditions of these vehicles. In the spirit of “Aatma Nirbhar Bharat” these wheel drives were designed and analysed by Bonfiglioli’s India R&D centre and developed by Bonfiglioli’s manufacturing facilities in India.
The reaction force from multiple wheels is transmitted to the machine frame by Bonfiglioli drives, This made it imperative to perform simulation tests (by using finite element analysis) for the load acting on the gearbox at different scenarios in the duty of the machine and accordingly gear profile optimisations and integrated bearing system were designed to have high power density and higher efficiencies. Drives/gearbox were designed with unique features, which can accommodate the readily available standard tyres in Indian market & after wide research, an innovative arrangement was designed to have two standard wheels supported by a single gearbox. As this machine must travel 10 kmph continuously for more than two hours, we also worked on a special lubrication level on the gearbox to dissipate the heat generated and a special sealing system was designed for the drives to work in harsh environment