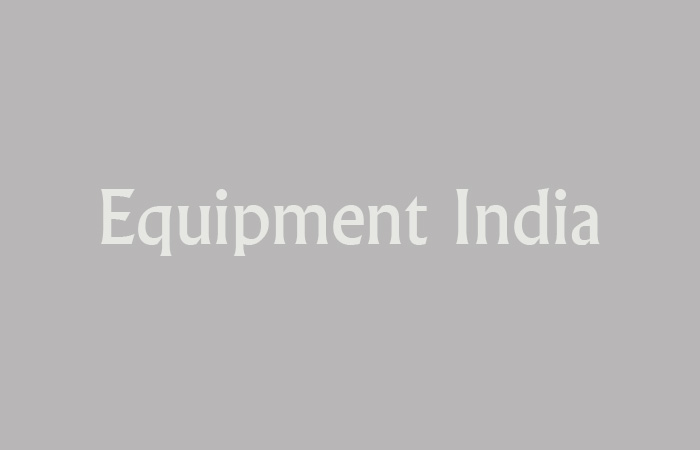
Bridging the Disconnect
Back in the 1930s, a consortium called Six Companies Inc won the right to build a concrete arch dam, costing nearly $49 millionùa staggering amount in the early 1930s (roughly equivalent to $900 million today). Skeptics thought it couldn't be done, others were convinced the contractors would go bust. But they finished the dam in five years, two years ahead of schedule and under budget. The story of the Hoover Dam is triumph of great design and construction, but nearly 90 years later, things aren't always as successful.
In many of today's Capital Projects, there is a disconnect between Front End Engineering Design (FEED) and detailed engineering design. Productivity has not improved in decades - the average Capital Project schedule lags by 20 months and goes over budget by 80 per cent1.
This is why the appetite for Unified Engineering is picking up pace. It enables global multi-discipline teams to work concurrently in a common data-centric environment, controlling and managing change across the entire project. The simulation data created in FEED is readily available for use in detailed design and is checked and validated in real-time, increasing efficiency, minimising risk, and maximising return on investment on your Capital Projects.
The real cost of engineering and design
While the cost of engineering and design typically amounts to just 10 per cent of the overall project cost, the work being carried out here heavily influences what happens in procurement and construction.
The leading cause of rework in project execution is design errors and omissions, and according to research, they contribute to over 5.4 per cent of the total construction cost2. Engineering errors alone make up 14.2 per cent of the total contract value3. Reducing engineering and design errors is therefore an essential factor in lowering project cost and minimising risk of overruns and delays. Action must be taken within the engineering phase to ensure these figures are minimised, and to lower total installed costs (TIC).
Breaking down silos
Unified Engineering breaks down the silos between process and engineering design, and ensures each discipline has ownership of their data and the reassurance that it is always correct. Early, FEED is a highly iterative process but with Unified Engineering data is entered only once. The simulation data created in FEED is readily available for use in Detailed Design, increasing efficiency across projects. Procurement errors and delays are avoided, and rework caused by poor quality deliverables is eliminated.
Unified Engineering is not just about collecting simulation data into a database. It is about empowering your team to take full control, to manage the data effectively. Even when big changes have been made, Unified Engineering ensures they can be easily validated. In simple terms, when teams share knowledge better, they make decisions much faster and improve their workflows compared to traditional ways of working.
Here are some tips to help improve your Unified Engineering approach:
- Leverage your digital strategy: Companies are beginning to make progress on their digitalisation journey, finding the right applications for digital transformation and seeing increasingly better returns on their investment. While the age-old market environment challenges (such as supply and demand, cost and price) haven't gone away, competitive pressures are making the digital transformation opportunity more pressing than ever.
- Discard tools such as MS Excel and move towards a data-centric approach: This will become reality with Unified Engineering - a new way to leverage your EPC 4.0 strategy and support the project lifecycle every step of the way. Doing so, removes the need to re-enter and re-check data and saves time when producing deliverables; time which can then be invested on further innovation within your organisation.
- Take advantage of Digital Twin technology: Have your Digital Twin ready to handover to the owner. Unified Engineering ensures your model is accurate and up-to-date throughout the project lifecycle. The Digital Twin of your plant ensures scope for high margin for EPCs and ease of start-up and operations for the owner.
- Collaboration rather than silos can be rewarding as well as financially impactful: Imagine a project where all your engineering departments are working together in a more seamless way, where the latest validated information is available to all project disciplines instantaneously. Technology can help facilitate better sharing of ideas and improve communication. Unite that with a better work/life balance for employees and organisations will have a combination of working smarter and attracting the best talent, which is a very powerful formula for success.
- Partner with experts in your sector: It is important to choose not only the right technology partner, but also the right people with an understanding of the whole picture and industry. The correct vendor can bring in best practices and avoid costly mistakes.
Engineers are problem-solvers who are used to addressing complex systems issues. Working together as a profession is not a new idea, and a unified approach has real impact. By adopting Unified Engineering, costs are reduced across the project lifecycle, especially from commissioning and start-up and into operations. With the improved profit margins, organisations can ensure their business is in a stronger position to compete for, as well as win and secure new contracts.
References
1.Reinventing Construction - a route to higher productivity, McKinsey, Rice Global E&C Forum Roundtable, September 2017; T.G. Jayanth, Expert û Capital Projects & Infrastructure, McKinsey & Co
2.Measuring the Impact of Rework on Construction Cost Performance, Bon-Gang Hwang1; Stephen R. Thomas, M.ASCE2; Carl T. Haas, M.ASCE3; and Carlos H. Caldas, M.ASCE4
3.Probabilistic Assessment of Design Error Costs Love et al., 2014
Amish Sabharwal, Global Head of Engineering, AVEVA, has over 25 years of experience in North America and internationally within the oil and gas, petrochemicals and power industries.