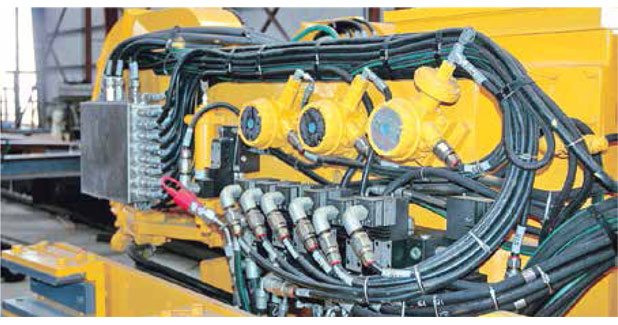
CE Maintenance and Hydrostatic System
Hydraulics, ie, transmitting power by supplying or pushing fluids in a confined area is most common medium of power transmission in almost all construction equipment as it is flexible, can provide high power transmission in small packages, it has variable speeds, can be reversed, has overload protection by means of pressure relief valves and it is self lubricating.
With regards to Indian construction equipment (CE) industry, we have attracted almost all major international players in this segment and they are either manufacturing equipment in India or being represented by some companies and dealers. We can see all major international construction equipment present at any large construction site. It has been a positive development in terms of options someone has in choosing the right equipment but in my own assessment some where there has been lack in developing the desired skills for running and maintaining these high capital intensive equipment.
Growth of construction industry has thrown a crisis of short for manpower in the day-to-day operation of the work as skilled manpower is not available for the plant and machinery. We have seen mechanisation of almost all construction activities. These machines are increasingly becoming tech savvy with the innovation of new technology each passing day. Availability of people with knowledge required to run these machines is becoming difficult with very few sources of generation of skilled people for the specified job. Construction industry has not been able to visualise this demand and supply gap and is now becoming victim of the problem.
Unfortunately, we have not put desired focus on training our maintenance personnel for day-to-day maintenance of all mechanical systems and specially hydraulic system used in different construction equipment which is the most vital part of construction equipment.
For hydraulic systems and components, our approach is more of reactive maintenance when we have failures, whereas it should be more of preventive maintenance. If we put our focus on preventive maintenance, it would result in less failure and huge time and money savings in repair and restoring the hydraulic system.
Cause of failures and precautions
The first major cause of failure of hydraulic system is contamination which is added during refilling of oils, replacement of failed hoses and pipes and non-replacement of filters on the scheduled times as recommended by OEMs.
Second major reason is improper use and overloading of system due to lack of knowledge on proper operation and carrying out repairs and pressure adjustments without proper testing tools and gauges and lack of knowledge.
The following initial steps can be taken to make our machines more reliable and productive:
- Training of operators and maintenance staff for correct operating procedures and day-to-day maintenance.
- Following OEM recommendations in day-to-day maintenance.
- Maintaining log book of all construction equipment running and maintenance record.
- Use correct grade oils and genuine filters only.
- Change filters when replacing oils.
- Use proper oil transfer pumps for direct filling of oil to the reservoir in order to avoid adding contaminants during refilling of oils
- Cleaning of reservoir inside and outside during refilling of oil.
- Use of only cotton clothes and not cotton waste which leaves behind small cotton threads and fibres when we wipe the internal components with it. These small threads block the small orifices and also get stuck between the small clearances and result in malfunctioning of equipment.
- Keep all indicators and gauges in proper working conditions to know correct functioning of components during operation.
- Repair all leaking and damaged parts immediately as they add contamination in the system during operation and thereafter.
- Last but not the least is cleaning and flushing of new hose when we replace the failed hose in any hydraulic system specially high pressure main supply hoses of close loop system used for all rotary motions like transit mixers, travelling and vibration system of vibratory rollers, conveyor and travelling system of paver and hydrostatic transmission systems of loaders and graders as hydraulic oil remains in the close loop between pump and motor.
The high pressure hoses get highly contaminated during their manufacturing process when the required length of hose is being cut from large bundles. During cutting of hose, rubber particles and metal particles enter inside the hose and more often the hose is crimped with fittings without proper cleaning and flushing. These hoses are when assembled to main supply lines of close loop system, cause severe damage to the pumps and motors.
Thorough knowledge is important for maintaining the hydraulic system, but at the same time it is important to clearly spell the responsibility of different maintenance personnel. Maintenance team should comprise mainly people responsible for preventive maintenance and few key persons who can properly read hydraulic schematic circuit of machines, can do proper pressure adjustments as per OEM?s specification and also re-commission machine with new components following standard practices as recommended by OEMs.
Cause of improper operation
If improper operation does occur, the cause can generally be traced to one of the following:
- Use of wrong oil viscosity/type.
- Insufficient fluid in the system.
- Presence of air in the system.
- Mechanical damage/structural failure.
- Internal or external leakage.
- Dirt, decomposed packing, water, sludge, rust, and other foreign material in the system.
- Improper adjustments.
- Heat exchanger that is plugged, dirty, or leaking.
Conclusion
Please note that actuator force is controlled by pressure, actuator speed is controlled by flow and actuator direction is controlled by direction of flow. It is therefore concluded that the pressure, flow and direction of flow are the factors that control and transmit power in a hydraulic system. To zero in on the root cause of malfunctioning of system we need to identify whether the problem is related with force, speed or direction of actuator and proceed with following steps:
- Read and study the hydraulic circuit diagrams.
- Carry out pressure and flow testing of hydraulic system
- Compare the test results with the OEM?s specifications
- Proceed with repairs using genuine parts and following standard procedures as specified by OEM
The author is Director at PHE Institute of Hydraulics. He is also Proprietor, Precision Hydraulic Engineers; Managing Partner, Sunbeam Precision Engineers; and Managing Partner, Precision Tyres.