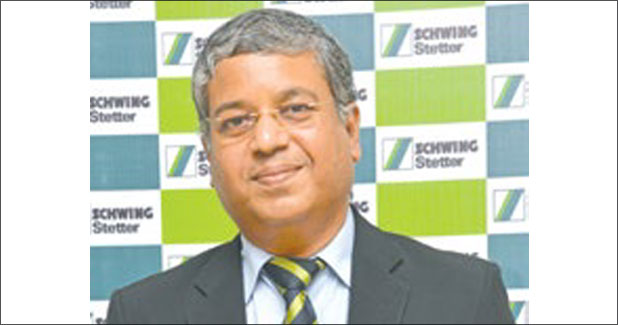
Concrete Delivery System
There is no method which can be termed as 'correct' or 'wrong' in concrete delivery and preparation. The solution is based on the type of project to be executed, time available and nature of construction, strength of concrete, volume of concrete, etc. India is a country where on one end we are launching 104 satellites in one go, while on the other, we do not have the basic level of mechanisation. For example, many of our villages are yet to be connected with proper infrastructure. We have a similar situation in construction sites that require concrete as well. India today has many high-rise constructions in various stages of implementation.
We have close to 15 cities building the Metro rail networks. India is investing big time in non-conventional sources of energy. The concrete required for all such projects is different from one another. For example, in the Subansri dam project, the requirement was for temperature controlled concrete of 880 m3/hr, produced at 10oC and was placed at 12oC at the pouring point. Two numbers of 240 m3/hr higher capacity batching plants ran for 24 hours straight, producing 6,220 m3 of dam concrete, setting a world record for the production of dam concrete.
So, the solutions are customised and the trends are different. For example, high rise projects are requiring concrete plants in higher capacity but with smaller footprints to save the land requirement. Highway projects are requiring plants with minimum setting-up time and no foundation cost so that they can be moved frequently without spending money. This is at one end of the spectrum. On the other end, small contractors who have trouble finding skilled manpower for construction are migrating to entry level mechanisation and are looking for cost-optimised investments to mechanise the project. Their aspiration is to keep the cost low and handle the challenge of mechanisation of related site activities like material handling, etc.
As an organisation, Schwing Stetter India is directly engaged with various trends of mechanisation across the segments of construction sites for both corporate and retail customers. We offer customised solutions that satisfy the project implementation requirements. In general, we are more focused on operating cost, ownership cost, reduction cost and more fuel efficient engines, etc. This is basically because concreting in sites has not changed in the last few years.
As far as automation and control systems are concerned, we are advancing with the latest changes in technology. Today we offer ERP solutions, fleet management, remote access and proactive maintenance for machines, to name a few Schwing Stetter product solutions.
Schwing Stetter India is the only company with in-house electronics and automation set-ups for concrete batching plants. The latest advancements are:
- Membrane keypad control to reduce the control cabin size;
- Automatic calibration to reduce the consumption of calibration time. The automatic calibration will be completed in less than 5 minutes as compared to the manual option which will take a complete shift in case of a H3N plant;
- Optional SMS alerts like alarms, production status;
- Continuation of previous batching or interrupted batching after power recovery. (This is only possible in our MCI 360 & 550);
- Open to connect the control system to ERP like SAP;
- Networkable with our Schwing 996 weighbridge. This feature is not available with any of our competitor's products;
- Maintenance scheduling and reminders;
- Any weigher, any slot configuration (can be done by configuring the software);
- Optional GPS support to plan the production.
Concrete delivery methodologies in making consistent quality concrete have seen a paradigm shift in the batching, pumping and transporting functions. They have been digitised to track, measure, manage, control, record and edit. The information flow from the equipment is through real time data, reports, alerts, instructions and tickets. Returned concrete is recycled and used again to build, which helps to keep the groundwater and environment sustainable. The returned concrete was difficult to be measured for certain factors of slump, water, temperature, load size and age previously, but now with technology advancements, it can be easily measured. Our equipment are made to run for a long lifetime. Few examples, in Bengaluru, a 21-year-old Stetter H1N plant has produced 15 lakh m3 of concreting and is continuing its production of concrete at ACC Yelahanka. A 14-year-old Stetter CP30S plant has produced more than 10 lakh m3 of concreting and is working at Hulmani Constructions, Davanagere.