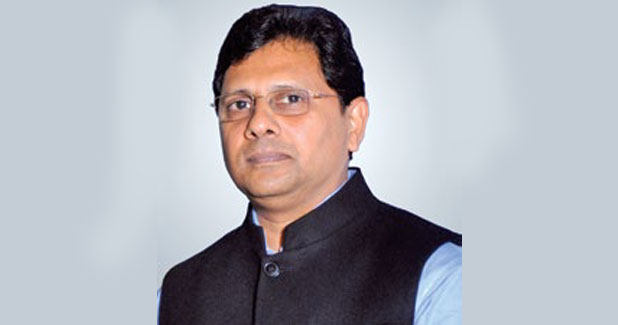
Conveyor systems are lifeline to mining industry
Conveyor systems provide a quick and effective transportation solution in mining with a high degree of safety. <span style="font-weight: bold;">Y Srinivas Reddy, Managing Director, Bevcon Wayors Pvt Ltd, </span>elaborates more on the importance of this bulk material handling system in mining.<p></p><p> <span style="font-weight: bold;">What are the different types of conveyors used in mining? What are the major components in a conveyor system?</span><br />Major types of conveyors used in mining include mobile/shiftable conveyors, overland belt conveyor, overland pipe conveyor, apron conveyor, reclaim feeders and sandwich belt high angle conveyor and pony belt conveyor for underground mining. In sandwich belt high-angle conveyor and pipe conveyors, the materials being conveyed are covered to avoid any contamination and dust generation. Major components in a belt conveyor system are technological structures, chains, belt, idlers, pulleys, motor, gearbox, scrappers, safety switches etc. </p><p> <span style="font-weight: bold;">Could you explain the range of conveyor systems offered by Bevcon Wayors and their important features? What is the capacity range and applications of these systems? </span><br />Bevcon gives thrust to 'Value Innovation', which will enhance the operations reliability, brings down the cost and time lines. Bevcon's core strength lies in the use of innovative conveying systems and equipment, which caters the present day demands of Indian mining sector.</p><p><span style="font-weight: bold;">Sandwich belt high angle conveyor:</span> Bevcon Wayors is a pioneer in the domain of bulk material handling solutions. We have introduced new technology in this sector, taking the nation a few notches higher in industrial growth. The sandwich belt conveyor that has been introduced in India by Bevcon Wayors is not a conventional conveyor. It is marked by originality in design, which has added to the machine's competence.</p><p>Introduction of 'Sandwich Conveyors' for open-pit mine (in-pit crushing conveying) is a breakthrough concept of conveying any mineral from the pit bottom to the surface by totally eliminating the use of conventional trucks. It also minimises the environmental degradation, brings down the operational cost drastically, and enhances productivity and product quality. </p><p>Types of material conveyed are coal, limestone, iron ore, woodchips, coke breeze, kimberlite, titanium ore, pebble ore, municipal sludge etc. Material conveying range is up to 4,000 TPH and conveying angle from 25o to 90o with C & S profiles.</p><p><span style="font-weight: bold;">Overland pipe conveyor: </span>This is a modern and environmentally friendly transporting system for all kind of bulk materials by overcoming numerous challenges associated with conventional conveyor systems. Pipe conveyors have best capabilities of transferring materials between two points, managing both horizontal and vertical curves as well as high inclinations, which are difficult in the case of trough conveyors. It eliminates multiple transfer points and exposure of material to atmosphere. Pipe conveyor not only protects the conveyed material against external influences such as climatic conditions, but also avoids material loss and spillage and thus, protects the environment.</p><p>Pipe conveyor has been used in various industries including power plants, steel, cement plants, refineries, port terminals etc for: transporting raw materials (limestone and ore from mine to process plant); In port terminals, loading and unloading materials in environmentally sensitive areas; In power plants, transporting coal; and In refineries, transporting sulphur. Material conveying range is up to 3,500 TPH, pipe diameters can be between 150 and 650 mm, and conveyor centre distance up to 10 km.</p><p>Overland troughed conveyor: In power and mining industries, moving large quantities of materials long distances reliably is an everyday necessity and requires a special type of conveyor which runs day in and day out. Overland troughed belt conveyors are designed to carry high tonnage loads over long distances.</p><p> Bevcon's long distance conveyor design ensures lowest power consumption per tonne of conveying. Overland belt conveyors have been proven to be an efficient method of transporting bulk material over long distances and costs are often lower compared to truck transportation. Types of materials conveyed are coal, petcoke, lignite, limestone, phosphate rock, bauxite, iron ore, sand, woodchips, quartz, feldspar, coke breeze, kimberlite, titanium ore, pebble ore, aggregate etc. Material conveying range is up to12,000 TPH.</p><p> <span style="font-weight: bold;">What are the advantages of conveyors in mining compared to conventional transportation methods? </span><br />Introduction of sandwich conveyors for open-pit mine (IPCC or in-pit crushing conveying) is a breakthrough concept of conveying any mineral from pit bottom to the surface by totally eliminating the use of conventional trucks. It also minimises the environmental degradation and brings down the operational cost drastically and enhances productivity and product quality. IPCC systems transport material by conveyor belt inherently and is more energy efficient than trucks due to the large empty vehicle mass required to power truck movement. However, conveyor belts will only accept material within a fine particle size distribution. A conveying system of any type requires primary and secondary crushing systems and or conveyor belt feeder/breakers to load them as well. This is the function of the crushing component of the IPCC. For hard rock applications, this will often be a gyratory crusher, but for soft rock, it will be a lower profile sizer or roll crusher. </p><p>Truck operations are currently the basic mining method employed by most surface mining operations worldwide. They have comparatively low capital acquisition cost and permit for flexibility in mine planning. On the negative side, however there are high labour requirements (each truck requires around seven operating and maintenance personnel for 24x7 operation), energy inefficiency related to alternatives, and dependence on the logistics of diesel fuel and consumables such as tyres etc. Safety implications of operating large fleets of mobile mining operations; roughly one-third of all fatal accidents in surface mines are related to vehicle accidents.</p><p> <span style="font-weight: bold;">What are the important measures to be taken for a smooth and continuous flow of materials through the conveyor system?</span><br />Operational performance of conveyor systems is based on a chain of actions taking place from concept to commissioning by the project supplier totally aligning with project deliverables and is followed by operation and maintenance (O&M) practices implemented by the project owner.</p><p> <span style="font-weight: bold;">What is the level of adoption of transportation of crushed minerals through conveyors in India?</span><br />At Bevcon, technological innovation is life line. We always strive to bring the best technologies to India with most cost-optimised manner and in the end, our customers will have winning edge in their processes and business. We always ensure the following aspects for every sale goes through which will create a goodwill and confidence to our customers: Equipment are reliable and efficient in operation; Best-in-quality - manufactured under in-house IME - Integrated Management System (ISO 9001:2015, ISO 14001:2004, OHSAS 18001:2007) certified manufacturing unit; Cost-effective; Best-in-service; Innovative features in the product; Low maintenance/low downtime; Low wear costs; Lowest product lifecycle cost; Technology transfer from collaborations; and Customised product development to meet the client needs.</p><p> <span style="font-weight: bold;">What is the current market trend for conveyor systems? </span><br />Automation in every industrial segment has become an integral part of industrial operations. Conveyor system is an important part of the overall material handling system that is required in every industrial process for various applications. Conveyor systems are mechanically-operated material handling equipment, which are used to transport material. They provide a quick and effective transportation solution with a high degree of safety. Growing demand for cost-effective material handling systems and increasing automation in the industrial sector are two of the major driving factors of global conveyor systems market. On the basis of their design modification, conveyor systems can be categorised as roller conveyor, belt conveyor, overhead conveyor and others. In order to meet the needs and demands of customers, manufacturers provide highly customised products. </p><p> <span style="font-weight: bold;">How do you look at the future of conveyor systems for mining in India?</span><br />Material conveying through conveyors is lifeline to mining industry. Considering future demands, we look forward to good prospects for the material handling industry in mining sector.</p>