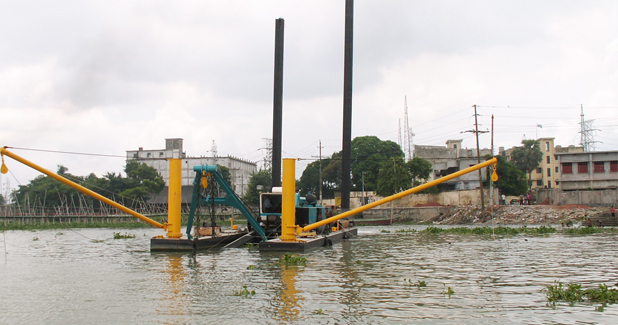
DSC Dredge bags Bangladesh order for portable cutter suction dredges
DSC Dredge recently shipped one of three new 18-inch Shark Class portable cutter suction dredges to contractors in Bangladesh. The second dredge will ship in July while the third dredge in February 2018. The contractors will use the new dredges to restore navigability to Bangladesh?s 24,000 km of rivers, streams and canals under Bangladesh Inland Water Transport Authority (BIWTA) and Bangladesh Water Development Board (BWDB) projects.
Following a 2009 study, the BIWTA has been calling on private contractors to help meet the demand for river dredging in Bangladesh. DSC delivered its first 18-inch Shark dredge to a contractor there in 2010. In 2011, DSC delivered the country?s largest dredges ? two 24-inch Marlin Class dredges, each with 23-m (75 ft) digging depth capability. During their first three years of service, the units worked 20 hours per day, six days per week. They both have well over 10,000 hours of use to date, and are still hard at work.
Each of the three new Shark dredge units is powered by a single Caterpillar C32 ACERT diesel engine, rated 1,125 hp, and features 17-m (55 ft) digging depth capability. The modern DSC design of a single engine and advanced hydraulic system provides maximum fuel efficiency and long component life. Older designs require two engines for peak performance, one for the dredge pump and one for the hydraulic system. With fuel being the highest single cost of operating a dredge, the fuel savings realised by the elimination of one engine are significant. The DSC hydraulic system design provides the same peak level of performance with just one engine.
All DSC dredges utilise integrated load sensing, pressure-compensated hydraulic components as standard. This not only reduces the power consumption, but also reduces the required cooling, tank capacity, and filtration. In a typical hydraulic system, where 50 per cent of the system?s flow and 75 per cent of the pump?s pressure are required for the task, a conventional fixed displacement system (found on older portable dredges) will consume 75 per cent of the pump?s power. Alternately, a pressure compensated system (typically found on modern dredges) consumes approximately 50 per cent of the pump?s power. DSC?s advanced hydraulic systems, however, consume only 37.5 per cent of the pump?s power. This lower power consumption relates directly to cost of operation, resulting in dramatic energy savings, longer component life and higher profits.
DSC provides its clients with complete OEM spare parts information, allowing them to keep their dredges operating at peak efficiency with commonly sourced parts ? a practice that is critical for international clients. Many other dredge manufacturers change OEM part numbers to their own numbering system, resulting in a single source for spares that is often located on the other side of the world. With the DSC spare parts policy, clients can purchase parts from a local distributor, and quickly be back into operation, rather than waiting on international air shipments, customs and all the costs associated with lengthy downtime.
Following a 2009 study, the BIWTA has been calling on private contractors to help meet the demand for river dredging in Bangladesh. DSC delivered its first 18-inch Shark dredge to a contractor there in 2010. In 2011, DSC delivered the country?s largest dredges ? two 24-inch Marlin Class dredges, each with 23-m (75 ft) digging depth capability. During their first three years of service, the units worked 20 hours per day, six days per week. They both have well over 10,000 hours of use to date, and are still hard at work.
Each of the three new Shark dredge units is powered by a single Caterpillar C32 ACERT diesel engine, rated 1,125 hp, and features 17-m (55 ft) digging depth capability. The modern DSC design of a single engine and advanced hydraulic system provides maximum fuel efficiency and long component life. Older designs require two engines for peak performance, one for the dredge pump and one for the hydraulic system. With fuel being the highest single cost of operating a dredge, the fuel savings realised by the elimination of one engine are significant. The DSC hydraulic system design provides the same peak level of performance with just one engine.
All DSC dredges utilise integrated load sensing, pressure-compensated hydraulic components as standard. This not only reduces the power consumption, but also reduces the required cooling, tank capacity, and filtration. In a typical hydraulic system, where 50 per cent of the system?s flow and 75 per cent of the pump?s pressure are required for the task, a conventional fixed displacement system (found on older portable dredges) will consume 75 per cent of the pump?s power. Alternately, a pressure compensated system (typically found on modern dredges) consumes approximately 50 per cent of the pump?s power. DSC?s advanced hydraulic systems, however, consume only 37.5 per cent of the pump?s power. This lower power consumption relates directly to cost of operation, resulting in dramatic energy savings, longer component life and higher profits.
DSC provides its clients with complete OEM spare parts information, allowing them to keep their dredges operating at peak efficiency with commonly sourced parts ? a practice that is critical for international clients. Many other dredge manufacturers change OEM part numbers to their own numbering system, resulting in a single source for spares that is often located on the other side of the world. With the DSC spare parts policy, clients can purchase parts from a local distributor, and quickly be back into operation, rather than waiting on international air shipments, customs and all the costs associated with lengthy downtime.