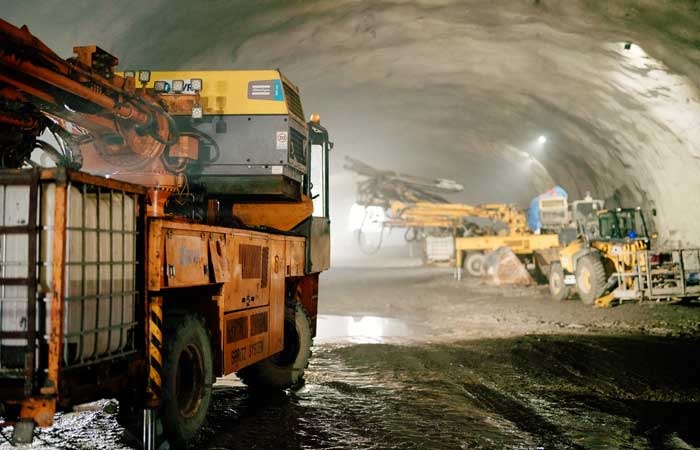
Driving Efficiency
Role of mobile compressors in modern construction
Mobile air compressors are indispensable in the construction and infrastructure sectors. Their primary function is to provide compressed air for various pneumatic tools and machinery essential in construction, maintenance, and repair activities at project sites. According to Ramesh Kumar G, Vice President of Portables at Elgi Equipments, air compressors are utilised across a broad spectrum of applications, including piling, road cleaning, rock anchoring, and shotcrete operations. The rising demand for these compressors is driven by global infrastructure development, spurred by governmental initiatives and economic growth.
Advancements and applications
In the contemporary construction landscape, both electric and diesel-powered screw air compressors are used extensively. Electric compressors are preferred for sites with reliable electricity due to their higher energy efficiency, reduced operational costs, and lower environmental impact. For instance, the use of Atlas Copcos electric E-Air compressor in the Mumbai-Pune Expressway project exemplifies the effectiveness of these units in confined and environmentally sensitive settings. These compressors helped maintain a continuous flow of clean, dry air, crucial for shotcreting within the tunnels, showcasing their capability to operate under stringent quality demands.
Conversely, diesel compressors are favored in locations lacking consistent power supply or where mobility is a necessity. These units are designed for easy transportation and robust performance in harsh environments, making them suitable for more demanding tasks. The versatility of diesel compressors enables them to function efficiently in remote or off-grid areas, supporting critical construction activities where high airflow and pressure capabilities are required.
Key uses across construction phases
Mobile compressors power numerous tools and machinery across various construction phases:
Technological innovations
The integration of technologies like Atlas Copcos PACE (Pressure Adjustable through Cognitive Electronics) system in their E-Air compressors illustrates the ongoing innovations within this field. The PACE technology allows for adjustable pressure settings, enhancing the efficiency and quality of applications such as shotcreting. Additionally, advancements in filtration and cooling systems, as seen in ELGis new portable compressor models, cater to extreme working environments, ensuring reliability and longevity of the equipment.
Cost-effectiveness and efficiency: One of the primary advantages of modern mobile compressors is their cost-effectiveness. Electric compressors, particularly, reduce the operational costs associated with traditional diesel-powered units. Their low power consumption and minimal maintenance requirements make them economically viable choices for long-term projects.
Sustainability: The shift towards sustainability is evident in the compressor manufacturing sector. Companies like Atlas Copco are aiming for net zero emissions by incorporating electric models that offer significant reductions in carbon footprint. Similarly, ELGi Equipments is enhancing its product line with low-noise, energy-efficient models to meet the increasing environmental standards and reduce overall energy consumption.
Dasika Ramarao, General Manager “ Sales & Marketing, Doosan Portable Power, highlighted the importance of localisation and advanced engine technologies in enhancing the efficiency and environmental compatibility of air compressors. He said, The focus on developing low-fuel consumption models and adapting to advanced emission norms are steps towards making air compressors more sustainable and economically viable.
Looking ahead, the air compressor market is expected to evolve significantly. Kumar notes that the trend is moving towards electric-powered solutions that offer higher energy efficiency and reduced emissions. The adoption of digital technologies for remote management and performance monitoring of compressors is also on the rise, paving the way for smarter, more connected construction sites.
Conclusion
As the construction equipment industry continues to grow, mobile compressors will play an increasingly vital role in shaping the landscapes of tomorrow. With advancements in technology and a focus on sustainability, these machines are set to revolutionise the way construction and infrastructure projects are executed. The insights provided by industry experts underscore the potential for innovation and efficiency, promising a future where construction not only builds but enhances global living standards.
CFM requirements: All air tools will have cubic feet per minute (cfm) requirement. It is important that the air compressor you choose to purchase will be able to drive the power tools you wish to use. For example, an air tool intended for general use will usually require 0 to 5 cfm at 70 - 90 psi (pounds per square inch).
Power type: Your air compressor power source is another factor to consider. Options include gas powered, electric as well as diesel options. Diesel compressors are very reliable and high performing, plus you do not need to worry about connecting to the electric grid to have power. Diesel particle filters (DPF) are often fitted to compressors to clean the emissions before they are released.
Size: For construction applications, your compressor must be small and compact enough to be easily towed whilst still being powerful enough to provide you with the flow of compressed air you need to power your equipment.
Noise: Depending on the type of construction work you are doing, noise may be a relevant factor to consider. In busy urban areas, a low-noise compressor would be the most beneficial as it would cause the least disruption.