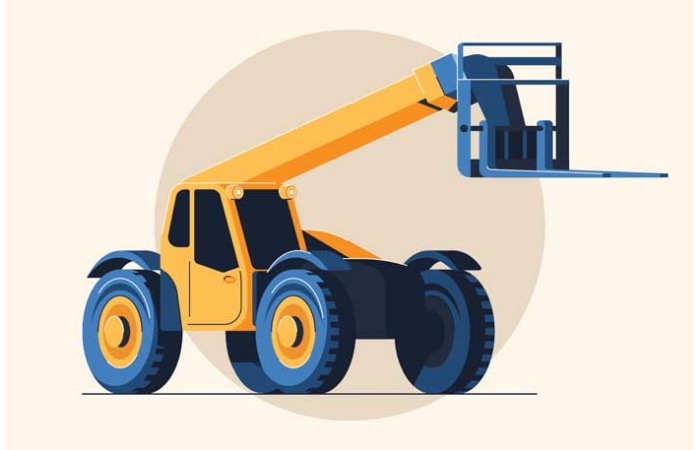
Enhancing Efficiency and Safety
Telehandlers, with their ability to lift heavy loads and navigate various terrains, inherently carry risks that demand meticulous attention. The telescopic boom, a defining feature of these machines, poses challenges such as instability during improper operation or on uneven surfaces. Additionally, the risk of falling objects and collisions underscores the need for stringent safety protocols and operator vigilance.
The telehandler market in India is characterised by the presence of both domestic manufacturers and international players. Companies such as JCB India, Mahindra Construction Equipment, TIL, and Escorts Construction Equipment are prominent domestic manufacturers. International players like Manitou, Caterpillar, and Bobcat also have a significant presence, leveraging their global expertise and technological advancements to cater to diverse customer requirements.
Manitou, one of the leading manufacturers of telehandlers in India, has a wide range of telehandlers for every segment, for every application and Manitou’s offering on telehandlers are broadly classified into the below categories; Manitou fixed telescopic, Manitou rotating telescopic, Manitou loader telescopic, Manitou heavy telescopic. Manitou rotating telehandler range is widely used in construction, maintenance, oil and gas, aeronautical applications where operating conditions face stiff space constraints and/or require quick operational maneuverability.
Said Hafeez Khan, Managing Director, Manitou South Asia, “Telehandlers have developed from conventional landscaping and farming machinery to much more sophisticated construction equipment. Manitou is heavily investing in R&D to develop and incorporate changes in its product line. Areas such as alternative fuels and energy sources as well as automation of controls and operations are some of the key areas where we are working and meeting our customer expectations. The growing shift of industries towards automation calls for the need to reduce the time taken for maintenance of industrial equipment such as overhead cranes.”
Manitou Group has indigenised two of its Best Seller models of the Asia Pacific region in its manufacturing facility in Greater Noida. These models are with the same safety and operational specifications as other models of Manitou manufactured in Europe and are being extensively sold to both Domestic and International markets.
Safety is paramount in all Manitou machines and all its products are equipped with critical features that guarantee this. About 70 per cent of accidents involving a handling machine could be prevented with the right machine for the right application and adequate safety training and measures. Accordingly, Manitou Group places user safety at the forefront of its priorities through two clearly-identified channels: risk prevention and the bespoke addition of safety systems on its machines.
Says Deepak Shetty, MD & CEO, JCB India, “As the Indian market matures, global best practices are making their way into the Indian material handling industry. There is an increased focus on productivity and safety on worksites, which presents us with the opportunity of introducing solutions with the latest and state-of-the-art technology in India. The demand for safe and reliable material handling products is fast growing across India’s wide spectrum of applications.”
He added, “Telehandlers are gaining popularity and are today being used in three core sectors – agriculture, construction and industry. Some examples are hopper loading in ready mix concrete, ceramic products and metal scrap recycling plants. In rail/road/hydel tunnel projects, the JCB telehandler with Man Platform provides a safe working platform for technical personnel. Telehandlers are used for horizontal and vertical movement of prefabricated components and aggregate material in the construction and infrastructure sector. The unique Q-Fit feature in JCB telehandlers enables easy and quick changeover of attachments, thereby increasing the versatility of the machines. An unloading rake attachment enables easy unloading of aggregate material from trucks. Different sizes of standard and grab buckets enable usage in industries like paper, metal scrap rehandling and coal rehandling. The Man Platform attachment has made the JCB telehandler a ‘must have’ for construction companies for any rail, road and hydel tunnel and bridge construction projects.”
Recently, JCB India celebrated the roll out of its 500,000th construction equipment. The 500,000th machine, a telehandler, is a versatile machine for material handling. It is a revolutionary new way to handle material at heights in a safer and more productive manner as compared to traditional options.
Said Shetty “It is only fitting that the 500,000th machine to roll out from JCB is a telehandler. This machine, ever since it was introduced in India, has made work sites safer and more productive with its superior design and engineering. JCB is a world leader in telehandlers and as India grows, we see opportunities for this machine in the material handling sector.”
Haulotte India, a 100 per cent subsidiary of the Haulotte Group of France and a leading global manufacturer of aerial work platforms, is regularly expanding its reach and range of telehandlers, adapting them to meet the specific needs of the end-users. All Haulotte HTL ranges comply with EC standards and TUV directives and regulations for safety. They are operator-friendly with a single joystick control for all types of operations. Their most distinguishable feature is the quick and easy recalibration of the Load Moment Indicator, which can be done by simply raising and lowering the boom for a few minutes. Haulotte telehandlers are being used across the world in different sectors and are also popular in the SAARC countries.
As part of the ongoing innovation at Haulotte, an entirely new line of telehandlers has been developed, specifically adapted for handling heavy loads of 5.2 to 7.2 tonne. With this, the company’s product portfolio now covers a wider range of solutions for every type of user.
HTL 5210, the latest addition, offers the best load rating for the 10 m segment with a lift capacity of 5.2 tonne up to a height of 10 m, representing a maximum forward reach at 3.5 tonne to 5.8 m, with the stabilizer. It is most suited for all types of applications in the heavy construction, mining, oil, ports, and recycling sectors. It enables optimal productivity, directly rivaling the 10 -12 tonne range with an unbeatable price to performance ratio.
The stabilizers included in the standard configuration ensure an excellent horizontal outreach. The rear axle locking system enables greater lateral stability for a very high load rating performance for the upper section. Easy to operate on non-stabilized surfaces, HTL5210 is a four-wheel drive and steer all-terrain telehandler. It is equipped with a hydrostatic transmission for high precision movements, and an inching pedal system for smooth and easy approach. The result is an extremely versatile range of applications based on the availability of numerous compatible accessories.
Road ahead
Looking ahead, the market for telehandlers in India is poised for substantial growth driven by ongoing and planned infrastructure projects, increasing mechanisation in agriculture, and the expansion of warehousing and logistics sectors. Key trends such as the adoption of electric and hybrid telehandlers to meet sustainability goals, advancements in autonomous and semi-autonomous technologies, and the integration of IoT for predictive maintenance are expected to shape the market's evolution.
Telehandlers have emerged as indispensable equipment in India’s burgeoning infrastructure and industrial sectors, offering versatility, efficiency, and safety in material handling operations. While the market presents lucrative opportunities, challenges related to initial costs, skills development, and regulatory compliance need to be addressed collaboratively by stakeholders. With sustained investments in technology, innovation, and skill enhancement, the telehandler market is well-positioned to capitalise on India's growth trajectory and contribute significantly to its economic development in the coming years.
Accidents with telehandlers happen on a regular basis. If you keep in mind the 7 tips below, you can avoid them from happening.
Follow the right telehandler training course: First of all, it's important to follow a suitable training course for telehandlers. Increase your safety and get to know the type of machine you'll be working with. Go over the manual of the machine thoroughly and familiarise yourself with all safety symbols.
Always inspect the telehandler before use: Conduct a daily visual and functional inspection before you get to work and only start working if the machine is in good condition.
Pay attention when loading the telehandler: Always make sure that the load does not exceed the maximum weight. An excessively heavy load could cause the telehandler to tilt. Most telehandlers are equipped with a safety system, which prevents the lifting of loads that are heavier than allowed. You can find the maximum weight of your telehandler in the user manual.
Pay attention when driving: Don't get distracted while driving. Make sure that the view of the route is always optimal. If you're not able to look more than two metres beyond your load, it is recommended to drive backwards. Also do this when you're carrying unstable loads or pallets that can slide off the forks. Ask for assistance if you have to drive forward with an unsurveyable load.
Always keep the forks 30 cm off the ground: The distance between the ground and the forks or attachment always has to be 30 cm when driving a telehandler. When transporting a load, keep it +/- 30 cm above the ground and always tilt the fork carriage backward. Pay special attention to the fork height on uneven surfaces and adjust it if necessary. When moving loads across larger distances, the telescopic boom must always be retracted. Make sure that assistants or other people keep their distance while loading. Never allow anyone to walk or stand still under to load.
Adjust your driving behaviour: Telehandlers can reach speeds of up to 40km/h on public roads. This is different on construction sites. Here, you have to adjust your speed to the situation. When you're driving on rough terrain at an excessive speed, you can lose control of the steering wheel and the telehandler. So always take into account the terrain and the telehandler load. When cornering, the centrifugal force comes into play. This means the goods are being drawn to the outside of the turn. Never start, stop or suddenly change direction at high speed. Always go up or down slopes in a controlled way and at an appropriate speed. These sudden and unexpected movements can cause the telehandler to lose its load or to tilt.
Always drive forwards when going uphill: Always drive straight forward when going uphill. So never drive uphill diagonally and never start turning on a slope. When loaded, the load must be in the highest position in relation to the slope (forwards uphill and backwards downhill). On slopes you need to increase the fork height and lean backwards more, to prevent contact with the ground.