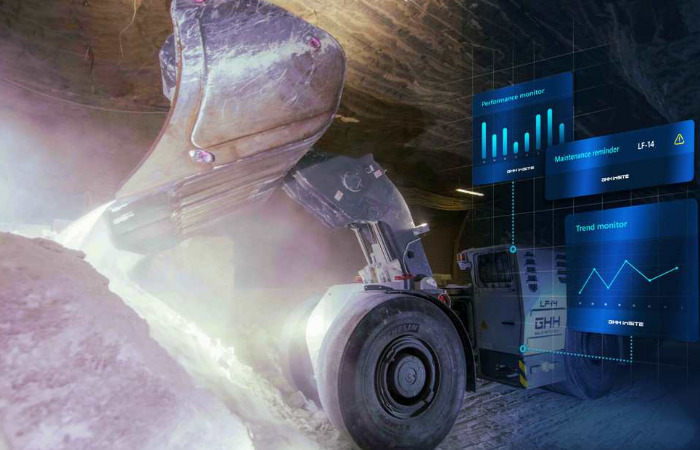
GHH releases new data analytics software
GHH has introduced GHH inSiTE, the latest digital analytics software from the company for monitoring and managing mining and tunnelling projects and large construction sites. This software can be used on any equipment regardless of brand. “Smart management is the future,” says Dr Felix Straßburger, Product Manager. “This increases the mining operations’ return on investment.”
Speed is the core benefit. “Today, mining and maintenance processes are often already so well coordinated that the smallest deviations can have undesired, costly consequences.” In view of the high workload and productivity targets, it is clear that costs must be kept under control.
Together with a vast team of external experts, GHH has created a digital analytics platform solution that transparently depicts the expensive on-site operations: ‘GHH inSiTE’ provides for a digital performance and condition monitoring, as well as the baseline for the future of digitally optimised mining operations. Its use is worthwhile due to the gain in operational safety and cost control, without requiring a substantial effort on the part of the user.
Sensors provide data
The system receives the input directly from the machines on site. Location, payload, distances, consumption, exhaust gas values, temperatures and much more: the measured data have long been available on many machines. According to Straßburger, the only thing lacking so far is comprehensive consolidation, meaningful evaluation and clear presentation.
This is where ‘GHH inSiTE’ comes into play. The software is regarded as a powerful tool that is adaptable and scalable, and thus designed to be future-proof. The connection to common IT infrastructures is guaranteed. All components are connected to each other via network. The data converge at the control station controller, partly in real time depending on the source. The responsible persons have all information available at any time via PC, tablet or smartphone. If something goes wrong or a change of schedule is required, they can intervene immediately: Networked rock logistics thus stands for more precise process sequences and minimum deviations. “The technology is proven and works reliably,” says Straßburger.
Major customer joins in
Even before the market launch, GHH took a major customer on board in 2019 to put the solution through its paces in practice. The results were so convincing that an order was placed in mid 2020: The contract covers a considerable part of the plant and equipment, around 150 machines. This is understandable, as the customer was able to achieve fuel savings of 7 per cent and an increase in efficiency of 12 per cent in the monitored sub-fleet alone.
Market observers agree: smart systems for rock logistics have come to stay. The benefits of central control, the contribution to real-time situation awareness and, in particular, the gain in operational safety and cost optimisation are just great. And the development is progressing rapidly. GHH is preparing to play a committed role in shaping this market: The company is already regarded as one of the world’s leading suppliers of almost everything in the field of rock logistics that drives on wheels.