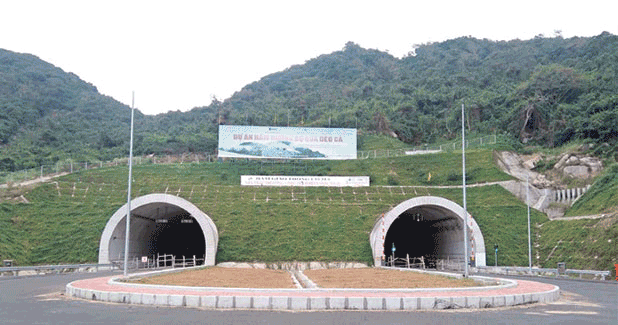
Genie Scores in Tight Tunnels
Ca Mountain Pass is a steep and torturous mountain pass in Vietnam. The 33 m high and 8 km long mountain pass crosses Dai Lanh Mountain that sits between Phu Yen and Khanh Hoa, two south-central provinces. While the pass offers a scenic ride, it is also the site of many traffic mishaps due to its dangerous bends and steep slopes. With the rising industrial zone and big-scale economic hub and tourism development projects in the provinces, the Vietnamese government saw a dire need to build a safer, more direct route between these neighbouring provinces.
On November 12, 2012, Vietnam?s Ministry of Transport launched a project to build a tunnel through the Ca Mountain. The tunnel is expected to reduce travel time by 75 per cent and save at least $10 million in transportation cost annually. The Deo Ca Tunnel, as it is called, will be 3.9 km twin tunnels, each with two traffic lanes. The project is expected to be completed by end of 2017.
The main construction work was completed in June 2015, and the project moved into installation work of mechanical and electrical components of the interior structures, such as fire alarm, camera and electrical circuitry. One of the main jobs was the installation of huge air ducts. Each duct measured approximately 5 ft in diameter, 3.3 m in length and 980 kg and needed to be installed one by one in a tight space of not more than 8.5 m wide per tunnel.
The Genie GTHTM-844 telehandler and two Genie ZTM-45/25 booms were used to carry out the installation work. What seemed like an insurmountable task was made seamless for the workers with each air duct installed within five days. Furthermore, only four workers were needed on the booms and one on the telehandler to carry out the operations. The tricky aspect of it was that the GTH-844 and Z-45/25 machines have to be well coordinated in their operations despite the tight space of the tunnel. ?A width of 8.5 m is very tight space for installing such large air ducts. But, Genie booms and telehandlers proved to be perfect for the job,? says Vo Thuy Linh, Vice President of Hai Thach Group, the company contracted to do the installation. ?We made a lot of careful consideration by studying the right machines to use for this project. Three main factors were looked into - the versatility of the machines in tight space, productivity and safety. We are also very fortunate to be supported by a professional team from TNC who were always listening to our needs and advising the right machines for the job. Genie was able to match up to all our expectations.? The project was serviced by Tuyet Nga Co, Ltd (TNC), a Genie distributor that has offices in Ho Chi Minh City, Hanoi and Danang.
Versatility of GTH-844 and Z-45/25 made it a good fit for the job
GTH-844: GTH-844 was used to lift the air ducts. This telehandler was specifically chosen because of its versatility. It not only periscopes vertically, but it can also reach out horizontally. This helps position an air duct quickly and smoothly while workers standing in Z-45/25 booms can work on the final installations efficiently. GTH-844 has width 2.48 m (8 ft 1.5 in), 3,629 kg (8,000 lb) maximum lift capacity and has a maximum lifting height of 13.41 m (44 ft). It is perfect for heavy-duty work for loading, unloading and moving the air ducts without having to move the machine much. This is a critical benefit when working in a tight space like the road tunnel.
Z-45/25: Z-45/25 was used to lift workers to the appropriate heights. Its platform rotation 180? and its turntable rotation 355? lets the workers move the platform exactly where they need it to be. It has a working height of 15.87 m (51 ft 6 in) and a lift capacity of 227 kg (500 lb). The models with jib boom moves with a range of 135? vertically for extra working range. The Z-45/25 also has a tight turning radius and zero tail swing for manoeuvering in confined work areas. The electric-operated Z-45/25 offer quiet, emission-free operation, which is important in a poorly ventilated road tunnel environment.
Productivity increased
The project required only five workers to complete the installation job in five days. The key reason for the machines? productivity is its ability to be deployed in the correct position quickly and efficiently. Hence, workers can proceed with other installation work and bring the project to completion much earlier than planned. This greatly helped mitigate deadline issues.
Safety was assured
There were zero accidents during the operation. This is a testament to the Genie policy of putting safety first into the design and engineering of every one of its machines. The GTH-844 and Z-45/25 machines have multiple safety features that are easy to use. Additionally, operators are always trained extensively on how to use these machines properly. The safety features coupled with hands-on training provided help to significantly reduce accidents through human errors.