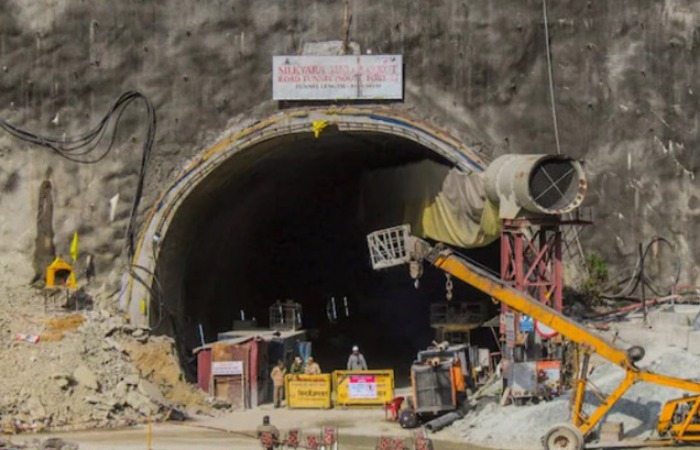
How critical equipment helped rescue trapped workers in Uttarkashi tunnel collapse
On the auspicious day of Diwali, 12 November 2023, the idyllic landscapes of Uttarkashi district in Uttarakhand, witnessed an unforeseen tragedy”the collapse of a section of the Silkyara Bend-Barkot tunnel under construction. This incident left 41 workers trapped inside, setting the stage for a remarkable tale of resilience, determination, and the collaborative efforts of various teams involved in the harrowing 17-day rescue operation.
The monumental rescue mission, aptly named Operation Zindagi, was spearheaded by the state government to free the trapped workers. The operation faced an array of challenges from the outset, primarily due to the absence of escape shafts in the tunnel and its construction in a geological fault. The initial rescue attempts were hindered by the type of debris generated during the collapse, prompting the deployment of rat-hole miners who employed manual mining methods to create an access pipe to reach the trapped workers.
The complexities of the operation required a multi-agency approach, involving the National Disaster Response Force, the State Disaster Response Force, Uttarakhand Police, Indian Army Corps of Engineers, and Project Shivalik of the Border Roads Organisation. Geologists from the state government and educational institutions were dispatched to the site to investigate the root cause of the incident.
As the rescue efforts unfolded, a series of setbacks, including drilling machine malfunctions and difficulties in navigating through debris, tested the mettle of the teams involved. The use of a US-made tunnel drilling machine proved challenging, eventually breaking and getting stuck inside the tunnel. Manual tools, such as hammers and chisels, became the instruments of choice to break through the debris and reach the trapped workers.
Despite the setbacks, alternate methods were intensively explored. Vertical drilling by Satluj Jal Vidyut Nigam and pipeline installations by Rail Vikas Nigam were initiated, adding strategic dimensions to the rescue operation. A road construction project by the Border Roads Organisation facilitated access to a hillock above the tunnel for potential vertical shaft drilling.
Vinod Kumar, ex-NHPC, who was also involved in 760-km long Konkan Railway project, connecting Mumbai to Bengaluru said, Tunnel rescuing is different from rescuing someone from building collapse. During building collapse, everything is visible, you just need to remove the rubble and rescue the people. Whereas in tunnel rescue operation, it is very difficult as rock falls through the roof. In this scenario, about 99 per cent of people across the world, remove the muck and water. When you remove the muck, more and more muck keeps coming in.
So which equipment works best in this scenario Says Kumar, We dont need large equipment. Small loaders like Bobcat or any 0.5 cum scoop tram, welding and gas cutting equipment, etc. are enough. Otherwise, a micro drilling equipment is the best with the 800 dia pipes.
The rescue operation is viewed as a remarkable achievement considering the challenging circumstances and the length of time the workers were trapped. The success of the rescue mission is attributed to the combined efforts of various teams, including rescue agencies, experts, and the Indian Army, who worked relentlessly to ensure the safety and liberation of the trapped workers, said SP Rajan, Head “ Plant & Machinery, Larsen & Toubro.
The collapse of the tunnel has raised questions about the preparedness and safety measures in place, suggesting that there were failures in preventing such a tragedy from occurring in the first place. Said SP Rajan, The encounter with various obstacles, such as the sluggish performance of the auger machine and the entanglement of its blades, were seen as failures that delayed the rescue efforts.
A laser equipment from Pune-based Suresh Indu Lasers was crucial. The company was charged with removing the drilling machine's 40-meter blade, which was blocking entrance to the rescue tunnel. The rescue teams had already begun cutting the blade with traditional equipment, but it took too long. The laser machine was then decided to be used. "Our equipment arrived on site on November 26 and completed the job on the same day," stated firm Director Vardhaman Shah.
It was a collective operation¦Being civilians we could not enter the tunnel. We gave the rescue personnel impromptu training on how to operate the equipment. The machine was lowered into the tunnel through a dummy pipe, Shah said.
One of the other equipment that was deployed during the rescue operation was Pro Engineers flexiprobe P540c portable video inspection system. The powerful controller provides a comprehensive and intuitive user interface, simple menus and dedicated function buttons. It incorporates reporting templates to comply with multiple standards to meet most needs. It has a built-in rechargeable battery that provide up to 7.5 hours usage.
The flexiprobe P540c system is managed by the most powerful and intuitive Controller ever designed by Pearpoint. A quick boot-up, an intuitive user interface and a high definition 10.1-inch TFT display, the P540c lets you concentrate on the job in hand. An MSCC-compliant report will be ready to share as soon as your survey is completed, using the condition codes of your chosen standard. The on-board WiFi connectivity allows to use communications device or dongle as a hotspot, letting one to share survey with the customer, manager or accounts department, creating productive time for you.
The success of the rescue mission is a testament to the collective efforts of various teams, including rescue agencies, experts, and the Indian Army, who worked tirelessly to ensure the safety and liberation of the trapped workers. The Silkyara Bend-Barkot tunnel incident serves as a poignant reminder of the importance of meticulous planning, geological awareness, and the relentless pursuit of innovative solutions in the face of adversity.