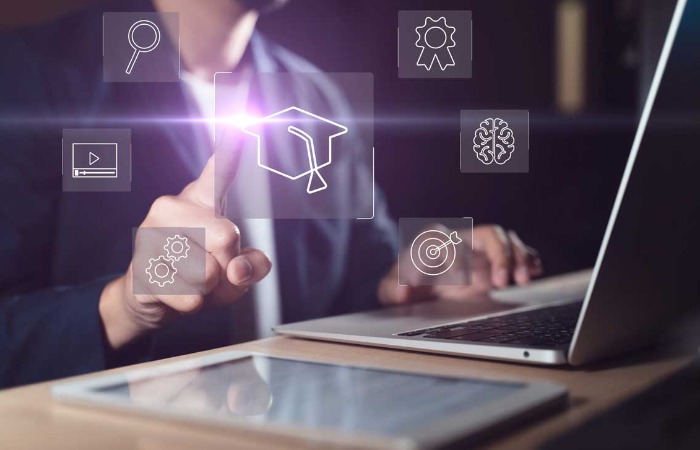
Innovations, Training, and Future of Upskilling
India's construction industry has experienced significant expansion over the past few decades, fueled by rapid urbanisation, large-scale infrastructure developments, and government initiatives like the Smart Cities Mission, expansion of metro in tier 2 and tier 3 cities, the Bharatmala project, the high-speed rail project, and renewable energy projects. As construction activities grow, the demand for a skilled workforce, especially in the construction equipment sector, continues to rise.
With advancements in automation, artificial intelligence (AI), telematics, and electric machinery transforming the industry, the need for specialised training and continuous skill enhancement has become more crucial than ever.
Importance of Skilling in CE Industry
The construction equipment sector plays a crucial role in infrastructure development, with a significant impact on productivity, efficiency, and safety. Skilled operators and technicians ensure that machinery is used optimally, reducing downtime and improving project timelines.
Despite the sector’s growth, a persistent skills gap exists. A large portion of the workforce lacks formal training, leading to inefficiencies, increased maintenance costs, and higher accident rates. To bridge this gap, structured training programs, industry-led certification initiatives, and continuous learning opportunities are essential.
Today, specialised training is no longer optional—it’s essential. Industry leaders are investing in programmes that prepare young professionals to operate heavy machinery efficiently and safely, boosting overall productivity. These efforts also create job opportunities for youth, empowering them to build sustainable careers in construction.
Moreover, the collaborative approach between training institutions and industry stakeholders enables aspiring professionals to gain both theoretical knowledge and hands-on experience. Practical learning in the operation of cranes, excavators, and advanced equipment ensures workers contribute effectively to projects, fulfilling specific business needs.
Specialised Training and Development
OEM-led training programmes: Original Equipment Manufacturers (OEMs) such as JCB, Caterpillar, Schwing Stetter and Volvo have recognised the importance of a skilled workforce and have established operator training centers across India. These programmes focus on hands-on training, safety protocols, and advanced machinery operations.
Government Initiatives for Skill Development: The Government of India, through schemes like the Pradhan Mantri Kaushal Vikas Yojana (PMKVY) and the Skill India Mission, has been instrumental in promoting vocational training. The Infrastructure Equipment Skill Council (IESC), established under the National Skill Development Corporation (NSDC), provides specialised training modules for construction equipment operators and technicians.
The Union Budget 2025-26 has introduced plans to establish five National Centers of Excellence for Skilling and a Centre of Excellence in AI over the next five years. According to the government, these centers will be developed with global expertise and partnerships to equip the youth with essential skills for the manufacturing sector.
Launched in 2015, Pradhan Mantri Kaushal Vikas Yojana (PMKVY), the government's flagship skill development program, has trained over 1.57 crore individuals, with more than 1.21 crore receiving certification under the scheme. Having evolved through four phases, PMKVY 4.0 now emphasises Industry 4.0 skills, including AI, machine learning, and robotics, to align with emerging industry demands.
Digital and Simulation-Based Training: The use of Virtual Reality (VR) and Augmented Reality (AR) is transforming training methodologies. These technologies provide immersive, risk-free environments for trainees to practice machinery operations, troubleshooting, and safety protocols before handling real equipment. Simulation-based training helps in reducing learning curves and improving retention rates.
E-Learning and Remote Training: With digital transformation accelerating across industries, e-learning platforms are becoming a popular mode for skilling. Webinars, online certification courses, and interactive modules enable professionals to learn at their own pace, ensuring continuous development without hampering work schedules.
Skill requirements for emerging technologies
The construction equipment industry is rapidly adopting new technologies, creating the need for a workforce proficient in modern tools and methodologies. Some key areas where specialised skills are required include:
Telematics and IoT integration: Modern construction equipment is equipped with telematics and Internet of Things (IoT) capabilities for real-time monitoring of machine health, fuel efficiency, and predictive maintenance. Operators and technicians must be trained in data interpretation and digital diagnostics to leverage these advancements effectively.
- Data interpretation and analytics: Operators and managers must analyse performance data and optimise machine usage.
- Software proficiency: Workers should be comfortable using fleet management platforms to monitor machine health.
- Preventive maintenance planning: Understanding sensor alerts to take proactive maintenance measures.
- Cybersecurity awareness: As machines become connected to networks, protecting data from cyber threats is essential.
Automation and remote operations: Autonomous and remotely operated construction machinery is gaining traction, particularly in large-scale infrastructure projects. Skilled professionals must be trained to operate, manage, and troubleshoot these advanced machines.
Required Skills:
- Understanding of AI and machine learning: Workers need to interpret data from automated systems and make real-time adjustments.
- Equipment programming and calibration: Operators must learn to program machines and fine-tune their operations based on site conditions.
- Remote monitoring and supervision: Familiarity with control interfaces that allow off-site monitoring and adjustments.
- Basic troubleshooting: Technicians should be able to diagnose and resolve errors in automated systems.
Electric and hybrid construction equipment: With sustainability becoming a key focus, electric and hybrid construction equipment is expected to replace traditional diesel-powered machinery. Workers need training in battery technology, energy management, and electric motor maintenance.
AI and robotics in construction: AI-powered systems and robotics are improving efficiency in excavation, material handling, and site surveillance. Professionals with expertise in AI applications, robotics maintenance, and programming will have a competitive edge in the industry.
Required Skills:
- Battery management & charging infrastructure: Workers must understand battery handling, charging cycles, and energy optimisation.
- High-voltage safety training: Since electric machines operate on high-voltage systems, safety training is critical.
- Diagnostics and software updates: Knowledge of firmware updates and remote troubleshooting techniques.
Safety and risk management: With increasing mechanisation, the emphasis on safety has also grown. Training in advanced safety protocols, emergency response, and hazard identification is crucial to minimise accidents and ensure compliance with global safety standards.
Human-machine collaboration & soft skills: While technology is advancing, human oversight remains crucial in ensuring safety, efficiency, and decision-making. Soft skills are becoming just as important as technical expertise.
Required Skills:
- Adaptability & Continuous Learning: Ability to embrace new technologies and upgrade skills regularly.
- Collaboration with AI & Co-Bots: Understanding how to work alongside robotic systems without disruption.
- Problem-Solving & Critical Thinking: Analysing unexpected equipment failures and implementing quick solutions.
Certification and upskilling for the future
Industry-recognised certifications: Certification programs play a vital role in validating skills and ensuring industry-standard proficiency. Globally recognised certifications, such as those provided by the National Institute for Construction Skills (NICS) and the Infrastructure Equipment Skill Council (IESC), help workers enhance their credibility and job prospects.
Cross-skilling and multi-skilling: To improve employability, workers must be trained in multiple skill sets. For example, an equipment operator trained in machine diagnostics, basic repair, and maintenance will be more valuable to employers. Cross-skilling enables workforce adaptability, reducing downtime in case of workforce shortages.
Continuous Professional Development (CPD): With technological advancements reshaping the industry, professionals must engage in lifelong learning. CPD programs through industry associations, OEMs, and online learning platforms ensure that workers stay updated with the latest developments.
Industry-academia collaborations: Collaboration between industry leaders and academic institutions can bridge the skill gap by designing curriculum aligned with industry requirements. Polytechnic institutes and technical universities should incorporate emerging technology modules into their courses.
Apprenticeship and on-the-job training: Hands-on experience through structured apprenticeship programs is essential for real-world application of theoretical knowledge. Leading companies are increasingly offering paid apprenticeship opportunities to nurture future talent.
Conclusion
The construction equipment industry in India is at a transformative stage, driven by infrastructure expansion and technological innovation. However, the lack of skilled professionals remains a significant challenge. Addressing this issue through specialised training, upskilling programs, and certification initiatives is critical for the industry's sustained growth.
Government support, industry collaboration, and innovative training methodologies will play a crucial role in equipping the workforce with the necessary skills to adapt to emerging technologies. By investing in skill development today, India’s construction equipment sector can build a more efficient, safe, and future-ready workforce.
For industry professionals, embracing continuous learning and upskilling will not only enhance career prospects but also contribute to the overall advancement of the construction sector. The future of construction equipment in India depends on a skilled and competent workforce—one that is ready to navigate the challenges and opportunities of tomorrow.
ABOUT THE AUTHOR:
The article is authored by Ratan Lal Kashyap, President – Supply Chain Management, DRAIPL