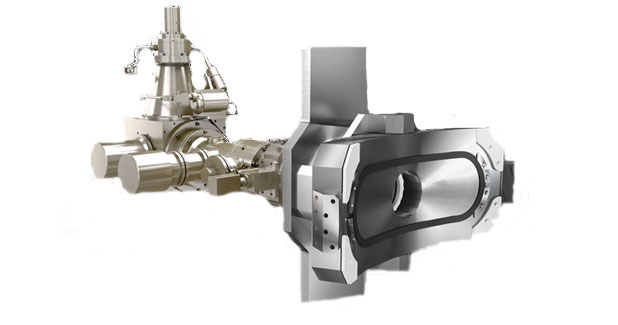
Innovative welding technology transforms productivity
A pioneering new type of local vacuum electron beam welding technology developed in the UK by Cambridge Vacuum Engineering (CVE) is helping to revolutionise the power generation sector. The EB ManPower project is a joint collaboration between CVE, U-Battery, Cammell Laird and TWI. <br /><br />Large scale nuclear reactors require high capital investment and heavily rely on the infrastructure of nuclear sites. The challenge has therefore been to develop smaller scale reactors, especially for developing countries and remote areas off main power grids. The current development of micro modular reactors presents a host of economic, industrial and environmental opportunities, contributing to the solution of <br />what is known as the 'energy trilemma' (low carbon, secure and affordable energy) and enabling a low carbon economy. <br /><br />Globally, 79 per cent of electricity is generated by thermal processes, in which conventional power plants provide over 62 per cent of global electricity supply and the remaining 17 per cent is by nuclear fission processes. This is expected to increase further (IEA, 2015). The demand for 'thick section' steel structures in power generation is already strong and continues to grow. The ability to fabricate these thick section structures cost-effectively is in part limited by the welding time and associated cost; to produce a typical 40-m long monopile (60 mm thick), for example, can take more than 6,000 hours of 'arc-on' welding time. <br /><br />To reduce cost, the manufacturing time therefore needs to be significantly reduced. CVE has developed the 'EBFlow' system, based on high productivity electron beam welding, which can reduce the welding time involved to less than 200 hours, equivalent to a reduction in cost of over 85 per cent. The EBManPower project, due to complete in 2021 and at a value of ú1.5 million, will implement and validate the first EBFlow system within a large-scale fabrication facility (in Birkenhead, UK) in order <br />to enable cost-effective manufacture of large scale power generation infrastructure. <br />The project is at its heart focused on reducing the cost of 'thick section' steel structures applicable for both nuclear and offshore wind structures. EBManPower will exploit CVE's revolutionary EBFlow system and will innovate, demonstrate and provide a near to market result; validation in a real world environment is the ultimate aim. <br /><span style="font-weight: bold;">Bob Nicolson, Managing Director at Cambridge Vacuum Engineering, </span>commented on the project, 'Our revolutionary EBFlow technology, fully developed and pioneered in Britain, will transform the productivity of fabrication processes throughout the world of heavy engineering. In many cases, the speed of welding can be 30 times faster than current methods.'<br /><br />CVE has developed the 'EBFlow' system, based on high productivity electron beam welding, which can reduce the welding time involved to less than 200 hours, equivalent to a reduction in cost of over 85 per cent.<br /><br />(Communication provided by company)<br />