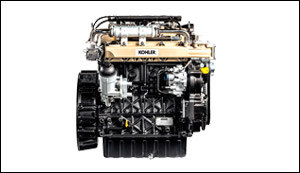
JCB Steps up Engine Strategy Development
JCB has gone from being a new entrant in engine manufacturing to an innovative global producer with the first JCB engine rolling off the production line in the UK in November 2004. Since then, production has been extended to JCB India's head quarters at Ballabgarh and to date, more than 250,000 engines have been produced globally.
JCB went into production this year with the innovative JCB Ecomax engine, which meets EU Stage IIIB/US Tier-4 Interim emissions standards without the need for a diesel particulate filter (DPF) or external exhaust after treatment.
Now, JCB has announced it is adopting a range of fuel-efficient Stage IIIB/Tier-4 Final engines from Kohler Engines, for many of its compact machine lines. The water-cooled Kohler Direct Injection (KDI) engines - which will be branded JCB Diesel by Kohler - meet the next stage of emissions regulations without the need for a DPF.
The first JCB machine to be fitted with the new engine, a JCB 35D 4x4 Teletruk, was unveiled at the RWM waste management show at the NEC in Birmingham. The Teletruk is JCB's innovative and award-winning telescopic forklift, saving customers time and money with its unique ability to reach forwards, enabling single-side loading and accurate placement of loads.
JCB's Director of Engine Programmes, Alan Tolley, said, "The decision to partner with Kohler for JCB compact machines was driven by the synergy in the technologies used by JCB and Kohler to achieve stringent Tier 4 Final emissions legislation. Kohler's achievement of Tier-4 Final without the need for a bulky DPF is fully in line with our own engine strategy and allows our designers maximum flexibility when it comes to meeting machine design and packaging requirements. These highly efficient engines will offer our customers improved performance and lower fuel consumption."
The European-built engines will be progressively introduced in JCB products, including midi excavators, the Teletruk TLT35D, 406 and 409 compact wheeled loaders, the 190 and 205 skid steers and 190T and 205T compact tracked loaders, smaller 135, 155 and 175 skid steers and TM180 and TM220 articulated wheeled loading shovels.
High torque output
The KDI engines use a common rail fuel injection system working at 2,000 bar pressure, liquid cooled exhaust gas recirculation (EGR), four valves per cylinder and a diesel oxidation catalyst (DOC) within the exhaust system. Thanks to the no DPF strategy, fuel consumption is up to 10 per cent better than a similar performance engine equipped with lower injection pressures in conjunction with a DPF. There are two 1.9-litre three-cylinder engines, the KDI 1903M and the KDI 1903TCR, delivering 31 kW (41 hp) with 133 Nm of torque and 42 kW (56 hp) with 225 Nm of torque, respectively. The 2.5-litre, four-cylinder KDI 2504M and KDI 2504TCR delivering 36.4 kW (48.8 hp) with 170 Nm and 55.4 kW (74 hp) with 300 Nm, respectively. The engines meet all JCB standards, with 500 hr maintenance intervals available on all models. Strong, low-rpm torque characteristics will result in improved machine performance and added engine responsiveness, delivering improved productivity for JCB customers.
"Innovation is a common thread running through the design of this completely new family of engines by Kohler," says Giuseppe Bava, Chief Executive Officer of Kohler's Diesel Engine Business Unit. They feature highly advanced technology for clean combustion and limited emissions without the use of after-treatment systems. KDI Engine family is designed to be compact, yet providing best-in-class performance in terms of power density of up to 23 kW/litre and torque density of up to 120 Nm/litre, becoming the new benchmark even for larger displacement engines. "Kohler is extremely proud to be appointed as JCB's engine supply partner for a wide range of construction equipment with the Kohler KDI engines," adds Tom Cromwell, President, Kohler Engines.