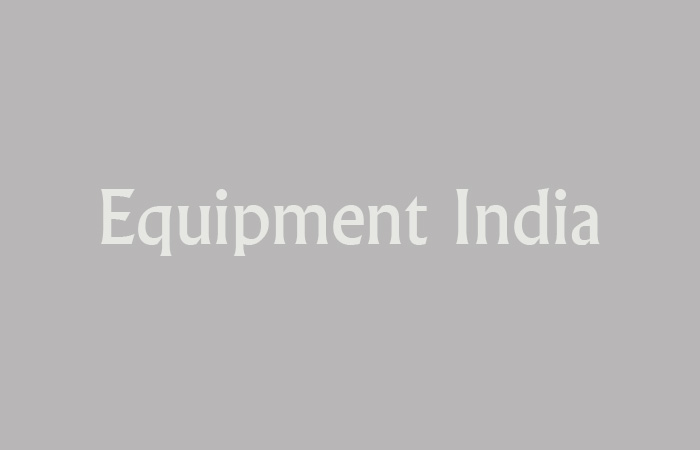
Keep Equipment Moving with the Right Viscosity Modifiers
Modern lubricants rely on additives, viscosity modifiers (VMs), and the base oils working together to deliver the required performance over the life of the lubricant. Changing any part of the formulation without confirming its impact on performance is a risk for lubricant-related failure, writes William (Bill) Dimitrakis of The Lubrizol Corporation.
Lubricant formulators may at times be tempted to exchange one viscosity modifier (VM) for another for a host of reasons, such as a lower cost or greater availability. On the surface, it may appear that substituting a different type of viscosity modifier - or even a viscosity modifier of the same polymer type - is a logical move. But actually, it?s very risky and its consequences can be disastrous.
Viscosity modifiers and how they work in lubricants
Viscosity modifiers are oil-soluble polymers that take the place of the heavier base stock when formulating the lubricant, as they provide the thickening needed. Additionally, the VM will raise the lubricant?s viscosity index (VI) by changing the rate at which the viscosity changes with temperature. At high temperatures, the polymer chains uncoil occupying more volume and thickening more. At low temperatures, polymer chains coil more, thickening less. In doing so, they maintain the viscosity of the oil as it cools and heats. A fluid without VMs becomes much more viscous when cold and loses viscosity more quickly when hot. Further, by significantly reducing or eliminating the need for heavy base stocks in the formulation, the effect of the wax in those oils crystalising at very cold temperatures is also reduced.
History of VM use in transportation lubricants
Viscosity modifiers made their first appearance in lubricants in the 1930s. During the 1950s, passenger car motor oils containing VMs hit the market as all season oils and quickly achieved success due to their convenience ? they eliminated the need for seasonal oil changes.
These new multi-grade oils could meet the low-temperature viscosity requirements of lighter viscosity grade oils in cold weather or during cold start-ups, as well as the high-temperature viscosity requirements of heavier grades for protection in hot climates and severe service.
The situation was similar for driveline lubricants. Beginning in the mid-1950s with General Motors Type A, Suffix A automatic transmission fluid, vehicle manufacturers recognised the benefit of VMs in ensuring their transmissions performed well year-round in all climates. Over time, the fluid performance requirements, such as low temperature viscosity, became more challenging. Today, multi-grade fluids are ubiquitous in most parts of the world, providing year-round service in a wide range of equipment and service conditions.
As vehicle technology advances in the 21st century to reduce emissions and increase fuel economy, the role of viscosity modifiers becomes significantly more critical. As the industry places greater demands on the lubricant to be more efficient, last longer, and protect better, the viscosity modifier is often called upon to provide performance beyond simply controlling viscosity. Today, VMs help improve piston cleanliness and deposit control, reduce viscosity increase from oxidation, control soot and sludge-mediated viscosity increase, and maintain durability of seals and friction materials. This performance can be obtained through the use of novel polymer structures or by chemical modification to existing polymer types.
Polymer properties
Many characteristics of polymers affect VM performance, including:
? Chemical composition (backbone and side chains).
? Solubility in base stocks.
? Molecular weight.
? Extent, length and composition of side chains.
? Polymer architecture (radial or block vs. random).
? Presence, type, and amount of functionalisation (such as dispersant nitrogen).
Performance to consider when selecting the right VM
Formulators should consider a number of factors when choosing the right VM to deliver optimal performance benefits for a specific application:
? Shear stability, or resistance to viscosity loss, especially under longer duration mechanical shearing in the base stocks of interest for the application. This determines how long the lubricant stays in grade and retains sufficient viscosity to properly lubricate.
? Low temperature performance. Achieving low temperature fluidity and pumpability required for the application is important, using the desired base stocks and without sacrificing other performance attributes.
? Ability to increase the lubricant?s VI as this correlates with improved efficiency and proper lubrication at low and high temperatures.
Other parameters which are very important in specific applications:
? Ability to provide dispersancy to the formulation.
? Capacity to control oxidation related deposits and viscosity increase.
? Ability to control soot-related viscosity increase and wear in heavy-duty engine oils.
? High temperature, high shear viscosity (HTHS) capability. This affects both efficiency and durability performance of engine oils.
? Dynamic and static coefficient of friction, which affects transmission clutch performance.
? Fluid traction properties, or internal fluid friction under load, which correlates with efficiency and fluid operating temperature.
? Elastohydrodynamic (EHD) film thickness properties which correlates with wear and durability of components.
The VM as an integral part of the approved formulation
Transportation lubricants generally have recognised industry standards and approvals that define the appropriate quality and ensure formulations have undergone rigorous testing to meet requirements. For example, high- quality engine oils in North America usually have the ILSAC starburst and the API service category prominently displayed on the label signifying that the oils are formally approved against these standards. In Europe, high quality engine oils generally carry both ACEA and various European OEM credentials. Automotive gear oils have the industry recognised SAE J2360 performance standard which requires the lubricant to meet bench and rig tests plus undergo a significant field trial to gain approval.
Once a lubricant has been tested and approved as meeting a specific quality standard, no part of the formulation can be changed without specific testing to confirm that the performance is not compromised. The industry has implemented guidelines as to how this must be done. In Europe, ATIEL, the technical association for the lubricant industry has developed a code of practice for engine oil development and testing which includes guidelines for VMs. These guidelines state that `viscosity modifiers can differ in their molecular structure and chemical composition, which may result in differences in the performance of formulated engine oils in engine tests and in service.` The guidelines further state that `any VM (interchange) must be supported by specific engine tests and rheological testing before implementation is permissible.` The required tests are outlined in the code of practice.
Similarly, in North America, the American Chemistry Council (ACC) product approval code of practice requires Level 2 support including chemical, rheological and engine testing before the VM in the approved formulation may be changed once the test programme is completed.
For factory-fill driveline applications specifically, maintaining the integrity of the formulation is even more critical. The original fill transmission or axle fluid is considered an OEM part. Once the transmission or axle is filled at the factory, the lubricant remains in the vehicle much longer than engine oil. For this reason, OEMs have very specific performance requirements and a stringent testing protocol that must be completed to gain approval. The approvals are very specific and no part of the formulation can be changed without rerunning much of the original approval program usually in conjunction with the OEM.
To ensure the right VM chemistry and quality is being used in the application, the use of a fully tested and approved formulation is recommended, which would include the performance package, the VM and the base oils that are part of the OEM approval or the ILSAC, API, ACEA or SAE credential programmes.
Changing the viscosity modifier can lead to loss of performance
Often, formulators or blenders are tempted to change the VM once a formulation has completed testing and the industry or OEM approval has been gained. The two main reasons for this are cost and convenience. An alternate VM product might cost less-per-kg or might have a lower treatment level. The blender may also have a VM in bulk storage that is more convenient to use.
There are real concerns with this approach. VMs are not all the same and should not be interchanged without following the specific industry or OEM guidelines and without developing the supporting data proving that modified formulas pass the critical tests. Some performance areas that could be affected by a change include:
Low temperature viscosity: Low temperature viscosity is critical to cold start up lubrication and has a large effect on operating efficiency. If the VM is not properly matched to the formulation including the base oils, the low temperature viscosity can be seriously compromised.
If a lubricant is unable to flow to critical wear surfaces during cold operation, the transmission will experience increased wear, reducing operating life or possibly equipment failure. This leads to unscheduled equipment downtime and loss of productivity.
Viscosity loss: Viscosity loss during service is another critical performance area. OEMs and end-users expect the transmission lubricant to remain in service for a minimum of 50,000 km, and in some cases as long as 500,000 km or more. It is critical to ensure the VM can withstand this service interval without viscosity break down. Viscosity loss in service also directly leads to increased wear on gear surfaces.
Oil film thickness: Oil film thickness is another fluid property affected by the VM. A proper oil film maintains lubrication to gear and bearing surfaces under load. As such, a lubricant should reduce apparent friction between surfaces while also reducing wear. This mechanism of protection is referred to as elastohydrodynamic (EHD) lubrication. An EHD testing apparatus can measure the effect of VM on lubricating oil film thickness, and reduced oil film thickness has been linked with greater wear on gear surfaces.
Beyond viscosity ? the real world impact of changing VMs without proper testing
The main requirement of OEMs and end-users is for lubricants to protect equipment in service. When that doesn?t happen, when the wrong VM is unable to help provide the needed protection, the largest problems begin to occur ? the beginning stages of equipment failure.
A gear pitting test analysis provides a strong comparison between a lubricant?s ability to provide protection to gear surfaces in the field. Photos help visualise the dramatic effect that two different viscosity modifiers, in lubricants with the same additive package, can have on gear pitting.
In the test, the lubricant containing the appropriate VM had strong resistance to shearing and necessary EHD oil film thickness to provide required performance and protection. A lubricant containing a different VM performed poorly on viscosity loss and oil film thickness, and as the photos clearly show, resulted in dramatic pitting. It is clear from this testing that substituting the specified VM with a different VM without confirming wear protection properties will put equipment in the field at risk for early failure.
Ensuring the lubricant delivers all the performance necessary
The formulator or blender can take steps to ensure the lubricant performs as the OEM or end-users expect:
Use a formulation including the performance additive, viscosity modifier and base oils that were tested and approved for the application. Follow the appropriate industry code of practice and do the required testing before changing any part of the approved formulation. For OEM-approved fluids, make sure to follow the OEM?s direction on what testing is required to validate performance before making formulation changes. For the VM, do not limit testing to simple viscometrics. VMs today provide important non-viscometric performance that is vital to the correct functioning of the lubricant. It is necessary to evaluate low temperature performance, viscosity retention after shear, deposit formation, oxidation, and wear performance in the appropriate tests before making a formulation change.
To sum up, viscosity modifiers play a larger role in today?s lubricating fluids than ever before. Keeping this in mind is important so that performance is not removed by interchanging the right VM with one that simply doesn?t meet the carefully designed lubricant requirements. Using the right VM goes a long way towards keeping equipment running as intended.
William (Bill) Dimitrakis joined Lubrizol in 1986 and has held commercial management positions in a number of Lubrizol?s business units. Since 2003, Bill has been Regional Busi?ness Manager in Lubrizol?s Viscosity Modifiers group and is responsible for commercial management for the Americas region as well as leading the commer?cialisation of new techno?logy for spe?cialty viscosity modifiers used in driveline and industrial lubricants and pour point depressants. Bill has written a number of articles and presented at industry conferences on the bene?fits of viscosity modifiers in modern lubricants. Bill earned a BS in Chemistry from the University of Pittsburgh in 1979 and a MBA from the University of Michigan in 1986. Email: William.dimitrakis@lubrizol.com
Lubricant formulators may at times be tempted to exchange one viscosity modifier (VM) for another for a host of reasons, such as a lower cost or greater availability. On the surface, it may appear that substituting a different type of viscosity modifier - or even a viscosity modifier of the same polymer type - is a logical move. But actually, it?s very risky and its consequences can be disastrous.
Viscosity modifiers and how they work in lubricants
Viscosity modifiers are oil-soluble polymers that take the place of the heavier base stock when formulating the lubricant, as they provide the thickening needed. Additionally, the VM will raise the lubricant?s viscosity index (VI) by changing the rate at which the viscosity changes with temperature. At high temperatures, the polymer chains uncoil occupying more volume and thickening more. At low temperatures, polymer chains coil more, thickening less. In doing so, they maintain the viscosity of the oil as it cools and heats. A fluid without VMs becomes much more viscous when cold and loses viscosity more quickly when hot. Further, by significantly reducing or eliminating the need for heavy base stocks in the formulation, the effect of the wax in those oils crystalising at very cold temperatures is also reduced.
History of VM use in transportation lubricants
Viscosity modifiers made their first appearance in lubricants in the 1930s. During the 1950s, passenger car motor oils containing VMs hit the market as all season oils and quickly achieved success due to their convenience ? they eliminated the need for seasonal oil changes.
These new multi-grade oils could meet the low-temperature viscosity requirements of lighter viscosity grade oils in cold weather or during cold start-ups, as well as the high-temperature viscosity requirements of heavier grades for protection in hot climates and severe service.
The situation was similar for driveline lubricants. Beginning in the mid-1950s with General Motors Type A, Suffix A automatic transmission fluid, vehicle manufacturers recognised the benefit of VMs in ensuring their transmissions performed well year-round in all climates. Over time, the fluid performance requirements, such as low temperature viscosity, became more challenging. Today, multi-grade fluids are ubiquitous in most parts of the world, providing year-round service in a wide range of equipment and service conditions.
As vehicle technology advances in the 21st century to reduce emissions and increase fuel economy, the role of viscosity modifiers becomes significantly more critical. As the industry places greater demands on the lubricant to be more efficient, last longer, and protect better, the viscosity modifier is often called upon to provide performance beyond simply controlling viscosity. Today, VMs help improve piston cleanliness and deposit control, reduce viscosity increase from oxidation, control soot and sludge-mediated viscosity increase, and maintain durability of seals and friction materials. This performance can be obtained through the use of novel polymer structures or by chemical modification to existing polymer types.
Polymer properties
Many characteristics of polymers affect VM performance, including:
? Chemical composition (backbone and side chains).
? Solubility in base stocks.
? Molecular weight.
? Extent, length and composition of side chains.
? Polymer architecture (radial or block vs. random).
? Presence, type, and amount of functionalisation (such as dispersant nitrogen).
Performance to consider when selecting the right VM
Formulators should consider a number of factors when choosing the right VM to deliver optimal performance benefits for a specific application:
? Shear stability, or resistance to viscosity loss, especially under longer duration mechanical shearing in the base stocks of interest for the application. This determines how long the lubricant stays in grade and retains sufficient viscosity to properly lubricate.
? Low temperature performance. Achieving low temperature fluidity and pumpability required for the application is important, using the desired base stocks and without sacrificing other performance attributes.
? Ability to increase the lubricant?s VI as this correlates with improved efficiency and proper lubrication at low and high temperatures.
Other parameters which are very important in specific applications:
? Ability to provide dispersancy to the formulation.
? Capacity to control oxidation related deposits and viscosity increase.
? Ability to control soot-related viscosity increase and wear in heavy-duty engine oils.
? High temperature, high shear viscosity (HTHS) capability. This affects both efficiency and durability performance of engine oils.
? Dynamic and static coefficient of friction, which affects transmission clutch performance.
? Fluid traction properties, or internal fluid friction under load, which correlates with efficiency and fluid operating temperature.
? Elastohydrodynamic (EHD) film thickness properties which correlates with wear and durability of components.
The VM as an integral part of the approved formulation
Transportation lubricants generally have recognised industry standards and approvals that define the appropriate quality and ensure formulations have undergone rigorous testing to meet requirements. For example, high- quality engine oils in North America usually have the ILSAC starburst and the API service category prominently displayed on the label signifying that the oils are formally approved against these standards. In Europe, high quality engine oils generally carry both ACEA and various European OEM credentials. Automotive gear oils have the industry recognised SAE J2360 performance standard which requires the lubricant to meet bench and rig tests plus undergo a significant field trial to gain approval.
Once a lubricant has been tested and approved as meeting a specific quality standard, no part of the formulation can be changed without specific testing to confirm that the performance is not compromised. The industry has implemented guidelines as to how this must be done. In Europe, ATIEL, the technical association for the lubricant industry has developed a code of practice for engine oil development and testing which includes guidelines for VMs. These guidelines state that `viscosity modifiers can differ in their molecular structure and chemical composition, which may result in differences in the performance of formulated engine oils in engine tests and in service.` The guidelines further state that `any VM (interchange) must be supported by specific engine tests and rheological testing before implementation is permissible.` The required tests are outlined in the code of practice.
Similarly, in North America, the American Chemistry Council (ACC) product approval code of practice requires Level 2 support including chemical, rheological and engine testing before the VM in the approved formulation may be changed once the test programme is completed.
For factory-fill driveline applications specifically, maintaining the integrity of the formulation is even more critical. The original fill transmission or axle fluid is considered an OEM part. Once the transmission or axle is filled at the factory, the lubricant remains in the vehicle much longer than engine oil. For this reason, OEMs have very specific performance requirements and a stringent testing protocol that must be completed to gain approval. The approvals are very specific and no part of the formulation can be changed without rerunning much of the original approval program usually in conjunction with the OEM.
To ensure the right VM chemistry and quality is being used in the application, the use of a fully tested and approved formulation is recommended, which would include the performance package, the VM and the base oils that are part of the OEM approval or the ILSAC, API, ACEA or SAE credential programmes.
Changing the viscosity modifier can lead to loss of performance
Often, formulators or blenders are tempted to change the VM once a formulation has completed testing and the industry or OEM approval has been gained. The two main reasons for this are cost and convenience. An alternate VM product might cost less-per-kg or might have a lower treatment level. The blender may also have a VM in bulk storage that is more convenient to use.
There are real concerns with this approach. VMs are not all the same and should not be interchanged without following the specific industry or OEM guidelines and without developing the supporting data proving that modified formulas pass the critical tests. Some performance areas that could be affected by a change include:
Low temperature viscosity: Low temperature viscosity is critical to cold start up lubrication and has a large effect on operating efficiency. If the VM is not properly matched to the formulation including the base oils, the low temperature viscosity can be seriously compromised.
If a lubricant is unable to flow to critical wear surfaces during cold operation, the transmission will experience increased wear, reducing operating life or possibly equipment failure. This leads to unscheduled equipment downtime and loss of productivity.
Viscosity loss: Viscosity loss during service is another critical performance area. OEMs and end-users expect the transmission lubricant to remain in service for a minimum of 50,000 km, and in some cases as long as 500,000 km or more. It is critical to ensure the VM can withstand this service interval without viscosity break down. Viscosity loss in service also directly leads to increased wear on gear surfaces.
Oil film thickness: Oil film thickness is another fluid property affected by the VM. A proper oil film maintains lubrication to gear and bearing surfaces under load. As such, a lubricant should reduce apparent friction between surfaces while also reducing wear. This mechanism of protection is referred to as elastohydrodynamic (EHD) lubrication. An EHD testing apparatus can measure the effect of VM on lubricating oil film thickness, and reduced oil film thickness has been linked with greater wear on gear surfaces.
Beyond viscosity ? the real world impact of changing VMs without proper testing
The main requirement of OEMs and end-users is for lubricants to protect equipment in service. When that doesn?t happen, when the wrong VM is unable to help provide the needed protection, the largest problems begin to occur ? the beginning stages of equipment failure.
A gear pitting test analysis provides a strong comparison between a lubricant?s ability to provide protection to gear surfaces in the field. Photos help visualise the dramatic effect that two different viscosity modifiers, in lubricants with the same additive package, can have on gear pitting.
In the test, the lubricant containing the appropriate VM had strong resistance to shearing and necessary EHD oil film thickness to provide required performance and protection. A lubricant containing a different VM performed poorly on viscosity loss and oil film thickness, and as the photos clearly show, resulted in dramatic pitting. It is clear from this testing that substituting the specified VM with a different VM without confirming wear protection properties will put equipment in the field at risk for early failure.
Ensuring the lubricant delivers all the performance necessary
The formulator or blender can take steps to ensure the lubricant performs as the OEM or end-users expect:
Use a formulation including the performance additive, viscosity modifier and base oils that were tested and approved for the application. Follow the appropriate industry code of practice and do the required testing before changing any part of the approved formulation. For OEM-approved fluids, make sure to follow the OEM?s direction on what testing is required to validate performance before making formulation changes. For the VM, do not limit testing to simple viscometrics. VMs today provide important non-viscometric performance that is vital to the correct functioning of the lubricant. It is necessary to evaluate low temperature performance, viscosity retention after shear, deposit formation, oxidation, and wear performance in the appropriate tests before making a formulation change.
To sum up, viscosity modifiers play a larger role in today?s lubricating fluids than ever before. Keeping this in mind is important so that performance is not removed by interchanging the right VM with one that simply doesn?t meet the carefully designed lubricant requirements. Using the right VM goes a long way towards keeping equipment running as intended.
William (Bill) Dimitrakis joined Lubrizol in 1986 and has held commercial management positions in a number of Lubrizol?s business units. Since 2003, Bill has been Regional Busi?ness Manager in Lubrizol?s Viscosity Modifiers group and is responsible for commercial management for the Americas region as well as leading the commer?cialisation of new techno?logy for spe?cialty viscosity modifiers used in driveline and industrial lubricants and pour point depressants. Bill has written a number of articles and presented at industry conferences on the bene?fits of viscosity modifiers in modern lubricants. Bill earned a BS in Chemistry from the University of Pittsburgh in 1979 and a MBA from the University of Michigan in 1986. Email: William.dimitrakis@lubrizol.com