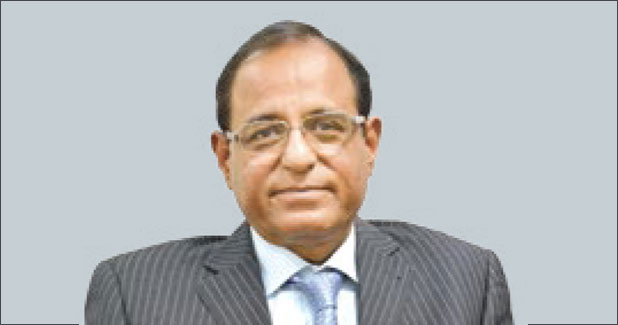
Maintenance Management
After three-four years of economic slowdown, now infrastructure development activities like roads, rail and Metro projects are coming up. It is very challenging to execute projects under these changing paradigms.
All the upcoming projects are time-bound, competitive and challenging in nature. In modern projects, equipment plays a leading role and 7-10 per cent of project costs are incurred in buying equipment.
Due to economic slowdown in the recent past, there is a lot of idle equipment with all the executing teams, and they are planning to execute the projects with this equipment without additional capital investment.
In most cases, for these existing idle equipment, proper maintenance was not executed for economic reasons, and now to maximise availability of these machinery is a challenging proposition.
As most of the equipment was idle for a long period, it now needs thorough repairing or overhauling, for which high cost is involved.
After commissioning, systematic and regular maintenance of construction equipment is an essential part of equipment management for smooth, uninterrupted and economical operation of a project.
Preventive maintenance is the backbone of the entire maintenance programme. The maintenance work should be entrusted to experienced personnel in such works. Most malfunctioning is detected by close inspection and can be corrected through scheduled maintenance and repair, so that downtime is minimised.
Spare parts management is also a part of the sound policy of preventive maintenance and goes a long way in improving maintenance and increasing productivity and profitability.
Good maintenance management is an important input for achieving the desired quality of product and services. Maintenance of a piece of equipment is the operation of keeping its various components in their original form as far as possible, with a view to ensure safety and production in operations.
It includes servicing, inspection and adjustments, small repairs in the field, major repairs and overhauls in main workshops and proper care of laid-up machines. Regular and proper supervision is a vital aspect of maintenance; another important factor being the upkeep of equipment records. Unless records are maintained, the validity of benefits of maintenance cannot be asserted
Construction equipment, besides being expensive, has often to work under rough conditions. Since the timely and economical completion of work essentially depends upon a satisfactory performance of all equipment, the need for proper maintenance cannot be overemphasised. However, the task of maintenance is rendered more difficult due to the heterogeneous collection of machines on a large construction project and their distribution over a large area. Planning for maintenance must include all these aspects.
Maintenance planning
Planning of maintenance is essential for any construction project. The maintenance plan determines the quality of work. A singular aspect of maintenance activities is the difficulty of assessing the quality of work done. If maintenance work is poorly done, it may lead to a breakdown; because of the intervening time lag, however, it is hard to judge whether the breakdown was due to maintenance errors or defective parts. In other words, the quality of maintenance must assure the quality of work itself.
To accomplish this, each individual member of the maintenance crew must have required expertise and a sense of responsibility, and consider methods for preparing, executing and validating his or her own work to raise the level of maintenance quality and efficiency.
It is essential to create a maintenance plan and make tenacious preparations prior to execution; the benefits of creating a maintenance plan can be summarised as below:
The number of operational steps can be identified and works can be rectified;
Human resources requirements can be planned so that required personnel are available;
Quality can be checked and better materials can be procured;
Errors in the procurement of materials and subcontracting work can be prevented;
By devising related work detail plans, schedules can be set so that they are coordinated with production plans;
Repair cycles can be identified so that measures can be taken in a timely fashion;
Standardised patterns for repair work can be identified, enabling the work to be done efficiently;
Simultaneous repair plan can be devised;
People's sense of responsibility can be encouraged. Through planned work activities, a larger volume of work can be efficiently accomplished.
Predictive maintenance
Predictive maintenance pertains to inspections to investigate deteriorating conditions. It is applicable in the following conditions:
- For equipment in which there is a distinct advantage in determining the maintenance period based on actual observation of the deterioration;
- For equipment that does not show any steady trend in deterioration, making it difficult to determine maintenance cycles.
- For equipment that lacks sufficient historical records, making it difficult to easily define maintained cycles.
To improve the rate of equipment effectiveness and reduce maintenance costs, it is necessary to promote corrective maintenance, to conduct thorough investigations into predictive maintenance, to carry out breakdown maintenance based on sound economic justification, and to promote preventive maintenance. The objective should be improving the rate of equipment effectiveness and to reduce maintenance costs through vigorous inspection techniques.
Preventive maintenance
Preventive maintenance systems reduce the likelihood of failures to the absolute minimum, and preventive planned servicing is carried out with the specific objective of detecting weak areas and ensuring perfect functioning (by even replacing certain critical parts, as required), for the assurance or reliability that users demand. Thus, after each servicing, the equipment is considered to be as good as new and is expected to give a high level of reliable performance.
This activity refers to taking measures for extension of machine life span and reduction of repair time and costs.
The documents to be procured are:
- Defect reports and investigation reports;
- Accident and incident reports;
- Premature failure of equipment report;
- Value engineering reports;
- Cost reduction techniques employed.
Benefits from preventive maintenance:
- Reduction in total downtime and consequent reduction in production losses;
- Reduction in the number of major repairs and consequently reduced maintenance expenses;
- Reduction in the number of rejects and an improvement in product quality;
- Reduction in the inventory of spare parts;
- Reduction in the number of accidents in the plant;
- Reduction in the unplanned or crisis management in maintenance.
Corrective maintenance
Corrective maintenance is defined as maintenance carried out to restore (including adjustment and repair on item) machinery, which has ceased to meet an acceptable condition. For example, you may have looked after your equipment fairly well and managed to keep it in good condition, yet a time will come when wear and tear will begin. So, the old and defective parts of that equipment are to be replaced with new ones.