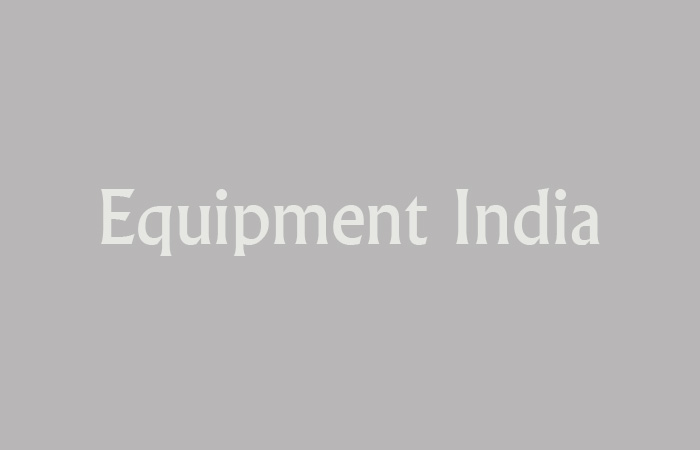
Maintenance of Tapered Bearings
Bearings increase efficiency of equipment by reducing friction to deliver higher performance. The useful life of any bearing depends to a great extent in the care and maintenance it receives, writes Brian Strunck.
Bearings are vital components in major industrial equipment. They increase efficiency of equipment by reducing friction, enabling the machine to deliver higher performance.The useful life of any bearing depends to a great extent on the care and maintenance it receives.This is especially true in industrial applications, where operating conditions tend to be harsh, loads are heavy and contamination from dirt and scale is a common affair.Tapered roller bearings include a cage that is susceptible to damage because it is not made of hardened steel. Mishandling or dropping the bearing can create damage that may result in a significantly shorter bearing life.
Tapered bearings consist of four interdependent components: the cone (inner ring), cup (outer ring), tapered rollers (rolling elements) and cage (roller retainer). They manage both thrust and radial loads on rotating shafts and are available in three configurations.
Single-row tapered roller bearings: These are the most basic and widely used tapered bearing, usually fitted as one of an opposing pair. During equipment assembly, this can be set to the required clearance (end play) or preload condition to optimise performance.
Double-row bearings: Two-row tapered bearing arrangements offer increased load capacity over single types.
Four-row bearings: This combines the inherent high load, radial/thrust capacity and direct/indirect mounting variables of tapered roller bearings into assemblies of maximum load rating in a minimal space.
Sizes: These bearings come in sizes 8 mm (0.315 inch) bore to 2,222.5 mm (87.5 inch) outside diameter (OD).
Applications: The bearings find a variety of industrial applications including rolling mills, crane wheels and sheaves.
Design attributes: These are available in single, double and four-row configu?rations.Custom surface geometries and coatings are available for enhanced performance.
Customer benefits: These bearings have the ability to manage both thrust and radial loads, providing for enhanced performance.
Removing bearing
Tapered roller bearings can frequently be re-used if properly removed and cleaned before returning to service.Remove bea?rings with extreme care. If not done correctly, you can damage the bearings, shaft and housing, requiring expensive repairs.
There are a variety of mechanical and hydraulic bearing pullers available (Fig 1) to enable you to remove bearings. When removing a bearing, the puller should be positioned against the back face of the inner ring assembly. Be careful that the puller does not contact the cage. This can be checked by hand rotating the cage once the puller is in position.
In some cases, the shaft shoulder extends as high as the inner ring rib OD.In this case, special pullers are available that pull the bearing through the rollers.The puller segments are in the two pieces that grip the back of the roller without contacting the cage. The adapter ring holds the split segments together and prevents them from spreading under the load.
Removal of rolling mill bearings
Heavy-duty TQO and TQIT bearings are four-row bearings designed specifically to handle exceptionally high loads like those found in the rolling mill industry. The large size and weight of bearings used in these applications pose special concerns during removal.
Handling these bearings requires a crane and some simple fixtures to safely conduct maintenance.Lifting fixtures can be used to remove the bearings from the chock and re-install them after completing maintenance (Fig 2).This example is designed to lift the entire bearing. Other simple designs can be used to handle the bearing one component or sub assembly at a time.
TQIT tapered bore bearings
The TQIT bearing was developed for high-speed and precision rolling mills. Its tapered bore design permits a tight interference fit on the roll neck. This tight fit ensures greater stiffness in the design as well as greater accuracy for precision-type applications.Most large bore bearings have threaded lifting holes in the cage ring that can be used to lift the inner ring assembly.Removing and assembling TQIT bearings is different because the inner ring has a tight fit on the roll neck. Hydraulic pressure should be used to remove and reinstall the inner ring assembly on the roll neck.
Cleaning
After removing a bearing from a piece of equipment, thoroughly clean it to remove all scale, water, lubricant, debris and any other contaminants. Bearings must be cleaned thoroughly to allow for proper bearing inspection.
Smaller bearings can be cleaned in a wash tank that circulates a cleaning solution such as kerosene, mineral sprits or a commercial solvent through the bearing (Fig 3). Use the cleaning solution to remove all lubricant and contamination, making sure that the internal rolling elements are completely clean.
Alkaline cleaners such as trisodium phosphate (TSP) mixed with two or three ounces per gallon of hot water, may also be used. Hot cleaning solutions are often used as a final cleaning or rinse after the initial cleaning.
For large bearings, or to clean large numbers of bearings, special cleaning equipment such as a large tank containing appropriate cleaning solution is required.Tanks are typically heated with electrical solution is required. Tanks are typically heated with electricity coils, and a plump is used to agitate the cleaning solution (Fig 4).Final cleaning is done by suspending the bearing and using a hose to flush away any contamination.
After a tapered roller bearing has been cleaned, dry it with compressed air. The air stream should be directed from one end of the roller to the other while holding the cage with your thumb to prevent the cage from spinning (Fig 5). Make certain there is no water in the air line. Spraying a bearing with moist air can result in rust or corrosion. Careful attention must be paid to the condition of the large roller end.To reduce bearing contamination from other sources, all parts of the housing, shaft and gears should be thoroughly cleaned.
Inspection
After cleaning the bearing, housing and shaft, and ensuring that the seats and backing are in good condition, evaluate the bearing to determine if it can be reinstalled or should be replace. Bearings should be replaced if they show:
?Fatigue spalling.
?Heat discolouration.
?Rust.
?Damaged cage.
?Noticeable wear.
While it may be possible to return bearings with those conditions to service, there is increased risk of bearing damage after the unit is reassembled.
All components of tapered roller bearings must be closely inspected before returning the bearing to service (Fig 6). The OD of the outer ring and ID of the inner ring should be inspected for any nicks or burrs that may interfere with the fit when reinstalling the components.
The race of the outer ring should be inspected for unusual wear. Special attention should be given to identify any nicks or spalls in the race. These types of damage can quickly propagate, leading to equipment failure.
The surface of each roller should be inspected for unusual wear or spalls.On the inner race, inspect the large rib damage, wear or discolouration. The rib provides an essential role in maintaining proper bearing function. Also inspect the race of the innerring.
On smaller bearings, the roller and cage prevent you from getting a clear view of the inner ring race. You can check for nicks or spalls by using a metal probe inserted in the small end of the inner ring to feel for damage on the race. A paper clip with a 90-degree bend in the end will serve the same purpose. Slide the probe under the small end of the cage and work it back and forth across the cone race. Spalls and nicks are caught quite easily with this tool.
Larger bearings may have one inspection roller that is held in place with removable pins that are not welded in place. These threaded pins can be removed by prying out the locking wire and screwing the pin out. By removing these pins and the roller, it will allow you to conduct a more thorough inspection of the inner ring race. After completing the inspection, reinstall the inspection roller and re-tighten the threaded pins and the locking wire.
Seals
If the unit uses seals or closures, they should also be inspected for wear or damage. Worn seals can allow dirt or water to enter the bearing. In most instances, seals are automatically replaced when a bearing is torn down for inspection. Inspect the seal surface on the shaft to ensure it is in good shape and working properly.
Bearing damage
Bearings may become damaged through improper handling and storage or through normal water in use despite taking proper precautions. Small areas of corrosion or rust, small nicks or spalls, can probably be repaired and the bearing returned to service. Large spalls on the bearing races will not be able to support the rollers under load, so repair of these areas is questionable. Spalls that exceed 25 to 30 per cent of
the width of the race are usually not repairable.
Installation
Do not remove the bearing from its packing until you are ready to mount it. The packaging provides protection from contamination. When installing a new bearing, do not remove the lubricant or preservative applied by the manufacturer. The preservatives used on almost all bearings are fully compatible with commonly used oils and other lubricants. Leaving it in place will protect the bearings from fingerprints and corrosion.
Bearings should be installed in a clean environment, free from dust, debris, moisture and other contaminants. When installing a bearing in the field, make an effort to ensure clean work area. Use protective screens around the work area, and provide a clean resting surface for the bearing and other components until they can be installed.
Before beginning the installation, plan your work. Be certain that you have the correct replacement bearing and necessary additional adjustment tools if appropriate, and have them on hand. Finally, if the bearing needs to be lubricated as part of the installation process, have the appropriate lubricants and tools available. Planning your work will enable you to perform the installation more quickly with few delays, shortening the amount of time the bearing is out of the equipment and exposed to contamination and possible handling damage.
Do not install bearings in a damaged or worn housing, or on a damaged or worn shaft. Inner and outer ring seat damage should be repaired by using properly fitted sleeves.Shafts can be built up by metal spray and re-machined to the correct size. If there is not a press fit on the shaft, a weld overlay and regrind process is recommended to bring the shaft back to specification.
Bearing fit
Mounting a tapered roller bearing with proper fit helps ensure that it will meet performance expectations. In general, the rotating ring must be mounted with a tight. A loose fir is used on a stationary inner ring or a double outer ring bearing, especially at the floating position.
Inner ring assemblies are usually mounted with a tight fir and should be pressed on the shaft using proper drivers (Fig 7). When pressing the inner ring on the shaft, be careful to avoid any misalignment. Also ensure that the cage is not damaged. Cages are relatively fragile, and can be easily damaged by contract with the driver.
When outer rings are installed with a tight fit, they can be pressed into the housing with a simple driver. The driver should contact the face of the outer ring (Fig 8).
In applications that require a tight fit, it can be easier to install the bearing if it is first heated to expand it slightly.
Outer rings mounted in aluminium housing must have a minimum tight fit of 0.001 times the outer ring OD. For magnesium housings, the inimum tight fit must be 0.0015 times the outer ring OD.
Precision bearings require a special fit that depends on its precision class. In addition to the proper fit and bearing alignment, desired accuracy of the spindle, outer ring and inner ring seat roundness, and square backing shoulders for both the inner and outer ring are critical.
Unsatisfactory spindle run out may result if any of these areas are out of tolerance.
Rolling mill bearings also require special fitting practices, depending on the type of bearing involved.
Machined surface finishes: The inner and outer ring seats should be smooth and within specifications-filed tolerances for size, roundness and taper. Ground finish is usually suggested for shafts whenever possible.
The suggested finish for ground and turned surfaces is:
?Inner ring seats ?
Ground: 1.6 Ra micrometers
(65 micro-inches) maximum.
?Inner ring seats ?
Turned: 3.2 Ra micrometers
(125 micro-inches) maximum.
?Outer ring seats ?
Turned: 3.2 Ra micrometers
(125 micro-inches) maximum.
Bearing seat finishes rougher than these limits reduce the contact area between the bearing and the seat. This can create a more loose fit, especially if the ring is pressed on and off several times.
Mounting
When heating tapered roller bearings, inner ring temperatures should not exceed 120oC (250oF) for standard class bearings and 66oC (150oF) for precision class bearings. Higher temperatures can change the bearing?s hardness and geometry.
Aluminium or magnesium housed outer rings require a tight fit. To ease installation, they can be reduced in size by freezing. Standard class bearings should not be chilled below -54oC (-65oF), and precision class not below -29oC (-20oF).
Whenever inner or outer rings are heated or cooled during assembly after mounting and returning to room temperature, they should be checked with a 0.001-0.002 inch feeler gauge.This ensures that the inner ring is pressed tightly against the shaft shoulder (Fig 9) or the outer ring is pressed tightly against the housing shoulder.Before checking, ensure that both the inner and outer rings are pressed tightly against the shaft or housing shoulder.
When using a press to install bearings, avoid damage to the inner ring assembly. Tapered roller bearings should be separated (the inner ring assembly removed from the outer ring) during installation. When installing the inner ring assembly, use great care to ensure that no force is applied to the cage or rolling elements.
Tapered roller bearing adjust?ment techniques
One advantage of Timken tapered roller bearings is that their setting can be adjusted for better performance in a given application. Some applications require a pre-load setting while other applications require end play. The amount of preload or end play depends on the particular application.
The proper bearing setting depends on many application requirements, including the flexibility of the housing and shaft, lubrication, speed, desired life and others. To determine the optimum bearing setting, refer to the original equipment manufacturer?s maintenance and repair literature to determine the setting used in the original application.
Methods of measuring bearing settings
When bearing pre-load is required, the most convenient way to determine the preload is to read the torque from the shaft?s rotation. To measure torque, wrap a string around a gear or other known diameter (Fig 10). Attach a spring scale to the string and pull the spring scale to rotate the shaft at a slow, steady aped. Read the force indicated on the spring scale. Multiply the force times the radius to determine the bearing torque.
You can obtain a direct torque reading by using a torque wrench (Fig 11 and 12). If necessary, you can convert torque into preload force or dimensional preload.
Bearing end play
If bearing end play is required, then a different method must be used to measure the amount of end play.
Locate a dial indicator against the end or shoulder on the shaft to measure the amount of axial movement (Fig 13). Load the shaft in one direction and oscillate it several times while the load is applied. A handle can be mounted on the shaft to make it easier to apply the load while oscillating the shaft. Oscillate the shaft at least 20 times to firmly seat the bearings and ensure an accurate reading.
After seating the bearings in one direction, set the indicator to zero. Then apply the load in the opposite direction, oscillating the shaft as before, and read any movement on the indicator. The difference between the two readings is the end play.
Adjusting the bearing
These are two common bearing adjustment methods: threaded shaft with a nut and a housing with an outer ring follower. If end play is desired, back off the nut until no drag is felt. If the bearings are to be preloaded, advance the nut until the required torque is measured on the shaft.
Where shims are used, the bearing is set by tightening the end cap or bearing outer ring follower without shims in place until the bearings bind slightly while rotating. The gap between the end plate and the housing is measured with a feeler gauge. This gap plus the desired end play will determine the total shim pack required.
Fitting practices
Stationary cone fitting practice depends on the application. Under conditions of high speed, heavy loads or shock, interference fits using heavy duty fitting practice, should be used. With cones mounted on underground shafts subjected to moderate loads (no shock) and moderate speeds, a metal to metal or near zero average fit is used. In sheave and wheel applications using underground shafts, or in cases using ground shafts with moderate looseness which varies with the cone bore size is suggested. In stationary cone applications requiring hardened and round spindles, a slightly looser fit may be satisfactory. Special fits may also be necessary on installations such as multiple sheave crane blocks.
Rotating cup applications where the cup rotates relative to the load should always use an interference fit.
Stationary, nonadjustable and fixed single-row cup applications should be applied with a tight fit whenever practical. Generally, adjustable fits may be used where the bearing setup is obtained by sliding the cup axially in the housing bore. However, in certain heavy duty, high load applications, tight fits are necessary to prevent pounding and plastic deformation of the housing. Tightly fattened cups mounted in carriers can be used. Tight fits are suggested when the load rotates relative to the cup.
To permit through boring when the outside diameters of single-row bearings mounted at each end of a shaft are equal and one is adjustable and the other fixed, it is suggested that the same adjustable fit be used at both ends. However, tight fits should be used if cups are backed against snap rings, to prevent excessive dishing of snap rings, groove wear and possible loss of ring retention. Only cups with a maximum housing fillet radius requirement of 1.3 mm (0.005 in) or less should be considered for a snap ring backing.
Two row stationary double cups are generally mounted with loose fits to permit assembly and disassembly. The loose fit also permits float when a floating bearing is mounted in conjunction with an axially fixed bearing on the other end of the shaft.
The fitting practice tables that follow have been prepared for both metric and inch dimensions.
For the inch system bearings, classes 4 and 2 (standard) and classes 3, 0, and 00 (precision) have been included.
The metric system bearings that have included are classes K and N (metric system standard bearings) and classes C, B, and A (metric system precision bearings).
Precision class bearings should be mounted on shafts and in housings which are similarly finished to at least the same precision limits as the bearing bore and OD.High quality surface finishes should be provided.
Two row and four row bearings, which are provided with spacers and shipped as matched assemblies, have been preset to a specifically bench end play. The specific end play setting is determined from a study of the bearing mounting and expected environment. It is dependent on the fitting practice and the required mounted bearings setting. Failure to use the designated fitting practice in the bearing application can result in improper bearing performance or sudden malfunction of the bearing, which may cause damage to machinery in which the bearing is a component.
Bearings are vital components in major industrial equipment. They increase efficiency of equipment by reducing friction, enabling the machine to deliver higher performance.The useful life of any bearing depends to a great extent on the care and maintenance it receives.This is especially true in industrial applications, where operating conditions tend to be harsh, loads are heavy and contamination from dirt and scale is a common affair.Tapered roller bearings include a cage that is susceptible to damage because it is not made of hardened steel. Mishandling or dropping the bearing can create damage that may result in a significantly shorter bearing life.
Tapered bearings consist of four interdependent components: the cone (inner ring), cup (outer ring), tapered rollers (rolling elements) and cage (roller retainer). They manage both thrust and radial loads on rotating shafts and are available in three configurations.
Single-row tapered roller bearings: These are the most basic and widely used tapered bearing, usually fitted as one of an opposing pair. During equipment assembly, this can be set to the required clearance (end play) or preload condition to optimise performance.
Double-row bearings: Two-row tapered bearing arrangements offer increased load capacity over single types.
Four-row bearings: This combines the inherent high load, radial/thrust capacity and direct/indirect mounting variables of tapered roller bearings into assemblies of maximum load rating in a minimal space.
Sizes: These bearings come in sizes 8 mm (0.315 inch) bore to 2,222.5 mm (87.5 inch) outside diameter (OD).
Applications: The bearings find a variety of industrial applications including rolling mills, crane wheels and sheaves.
Design attributes: These are available in single, double and four-row configu?rations.Custom surface geometries and coatings are available for enhanced performance.
Customer benefits: These bearings have the ability to manage both thrust and radial loads, providing for enhanced performance.
Removing bearing
Tapered roller bearings can frequently be re-used if properly removed and cleaned before returning to service.Remove bea?rings with extreme care. If not done correctly, you can damage the bearings, shaft and housing, requiring expensive repairs.
There are a variety of mechanical and hydraulic bearing pullers available (Fig 1) to enable you to remove bearings. When removing a bearing, the puller should be positioned against the back face of the inner ring assembly. Be careful that the puller does not contact the cage. This can be checked by hand rotating the cage once the puller is in position.
In some cases, the shaft shoulder extends as high as the inner ring rib OD.In this case, special pullers are available that pull the bearing through the rollers.The puller segments are in the two pieces that grip the back of the roller without contacting the cage. The adapter ring holds the split segments together and prevents them from spreading under the load.
Removal of rolling mill bearings
Heavy-duty TQO and TQIT bearings are four-row bearings designed specifically to handle exceptionally high loads like those found in the rolling mill industry. The large size and weight of bearings used in these applications pose special concerns during removal.
Handling these bearings requires a crane and some simple fixtures to safely conduct maintenance.Lifting fixtures can be used to remove the bearings from the chock and re-install them after completing maintenance (Fig 2).This example is designed to lift the entire bearing. Other simple designs can be used to handle the bearing one component or sub assembly at a time.
TQIT tapered bore bearings
The TQIT bearing was developed for high-speed and precision rolling mills. Its tapered bore design permits a tight interference fit on the roll neck. This tight fit ensures greater stiffness in the design as well as greater accuracy for precision-type applications.Most large bore bearings have threaded lifting holes in the cage ring that can be used to lift the inner ring assembly.Removing and assembling TQIT bearings is different because the inner ring has a tight fit on the roll neck. Hydraulic pressure should be used to remove and reinstall the inner ring assembly on the roll neck.
Cleaning
After removing a bearing from a piece of equipment, thoroughly clean it to remove all scale, water, lubricant, debris and any other contaminants. Bearings must be cleaned thoroughly to allow for proper bearing inspection.
Smaller bearings can be cleaned in a wash tank that circulates a cleaning solution such as kerosene, mineral sprits or a commercial solvent through the bearing (Fig 3). Use the cleaning solution to remove all lubricant and contamination, making sure that the internal rolling elements are completely clean.
Alkaline cleaners such as trisodium phosphate (TSP) mixed with two or three ounces per gallon of hot water, may also be used. Hot cleaning solutions are often used as a final cleaning or rinse after the initial cleaning.
For large bearings, or to clean large numbers of bearings, special cleaning equipment such as a large tank containing appropriate cleaning solution is required.Tanks are typically heated with electrical solution is required. Tanks are typically heated with electricity coils, and a plump is used to agitate the cleaning solution (Fig 4).Final cleaning is done by suspending the bearing and using a hose to flush away any contamination.
After a tapered roller bearing has been cleaned, dry it with compressed air. The air stream should be directed from one end of the roller to the other while holding the cage with your thumb to prevent the cage from spinning (Fig 5). Make certain there is no water in the air line. Spraying a bearing with moist air can result in rust or corrosion. Careful attention must be paid to the condition of the large roller end.To reduce bearing contamination from other sources, all parts of the housing, shaft and gears should be thoroughly cleaned.
Inspection
After cleaning the bearing, housing and shaft, and ensuring that the seats and backing are in good condition, evaluate the bearing to determine if it can be reinstalled or should be replace. Bearings should be replaced if they show:
?Fatigue spalling.
?Heat discolouration.
?Rust.
?Damaged cage.
?Noticeable wear.
While it may be possible to return bearings with those conditions to service, there is increased risk of bearing damage after the unit is reassembled.
All components of tapered roller bearings must be closely inspected before returning the bearing to service (Fig 6). The OD of the outer ring and ID of the inner ring should be inspected for any nicks or burrs that may interfere with the fit when reinstalling the components.
The race of the outer ring should be inspected for unusual wear. Special attention should be given to identify any nicks or spalls in the race. These types of damage can quickly propagate, leading to equipment failure.
The surface of each roller should be inspected for unusual wear or spalls.On the inner race, inspect the large rib damage, wear or discolouration. The rib provides an essential role in maintaining proper bearing function. Also inspect the race of the innerring.
On smaller bearings, the roller and cage prevent you from getting a clear view of the inner ring race. You can check for nicks or spalls by using a metal probe inserted in the small end of the inner ring to feel for damage on the race. A paper clip with a 90-degree bend in the end will serve the same purpose. Slide the probe under the small end of the cage and work it back and forth across the cone race. Spalls and nicks are caught quite easily with this tool.
Larger bearings may have one inspection roller that is held in place with removable pins that are not welded in place. These threaded pins can be removed by prying out the locking wire and screwing the pin out. By removing these pins and the roller, it will allow you to conduct a more thorough inspection of the inner ring race. After completing the inspection, reinstall the inspection roller and re-tighten the threaded pins and the locking wire.
Seals
If the unit uses seals or closures, they should also be inspected for wear or damage. Worn seals can allow dirt or water to enter the bearing. In most instances, seals are automatically replaced when a bearing is torn down for inspection. Inspect the seal surface on the shaft to ensure it is in good shape and working properly.
Bearing damage
Bearings may become damaged through improper handling and storage or through normal water in use despite taking proper precautions. Small areas of corrosion or rust, small nicks or spalls, can probably be repaired and the bearing returned to service. Large spalls on the bearing races will not be able to support the rollers under load, so repair of these areas is questionable. Spalls that exceed 25 to 30 per cent of
the width of the race are usually not repairable.
Installation
Do not remove the bearing from its packing until you are ready to mount it. The packaging provides protection from contamination. When installing a new bearing, do not remove the lubricant or preservative applied by the manufacturer. The preservatives used on almost all bearings are fully compatible with commonly used oils and other lubricants. Leaving it in place will protect the bearings from fingerprints and corrosion.
Bearings should be installed in a clean environment, free from dust, debris, moisture and other contaminants. When installing a bearing in the field, make an effort to ensure clean work area. Use protective screens around the work area, and provide a clean resting surface for the bearing and other components until they can be installed.
Before beginning the installation, plan your work. Be certain that you have the correct replacement bearing and necessary additional adjustment tools if appropriate, and have them on hand. Finally, if the bearing needs to be lubricated as part of the installation process, have the appropriate lubricants and tools available. Planning your work will enable you to perform the installation more quickly with few delays, shortening the amount of time the bearing is out of the equipment and exposed to contamination and possible handling damage.
Do not install bearings in a damaged or worn housing, or on a damaged or worn shaft. Inner and outer ring seat damage should be repaired by using properly fitted sleeves.Shafts can be built up by metal spray and re-machined to the correct size. If there is not a press fit on the shaft, a weld overlay and regrind process is recommended to bring the shaft back to specification.
Bearing fit
Mounting a tapered roller bearing with proper fit helps ensure that it will meet performance expectations. In general, the rotating ring must be mounted with a tight. A loose fir is used on a stationary inner ring or a double outer ring bearing, especially at the floating position.
Inner ring assemblies are usually mounted with a tight fir and should be pressed on the shaft using proper drivers (Fig 7). When pressing the inner ring on the shaft, be careful to avoid any misalignment. Also ensure that the cage is not damaged. Cages are relatively fragile, and can be easily damaged by contract with the driver.
When outer rings are installed with a tight fit, they can be pressed into the housing with a simple driver. The driver should contact the face of the outer ring (Fig 8).
In applications that require a tight fit, it can be easier to install the bearing if it is first heated to expand it slightly.
Outer rings mounted in aluminium housing must have a minimum tight fit of 0.001 times the outer ring OD. For magnesium housings, the inimum tight fit must be 0.0015 times the outer ring OD.
Precision bearings require a special fit that depends on its precision class. In addition to the proper fit and bearing alignment, desired accuracy of the spindle, outer ring and inner ring seat roundness, and square backing shoulders for both the inner and outer ring are critical.
Unsatisfactory spindle run out may result if any of these areas are out of tolerance.
Rolling mill bearings also require special fitting practices, depending on the type of bearing involved.
Machined surface finishes: The inner and outer ring seats should be smooth and within specifications-filed tolerances for size, roundness and taper. Ground finish is usually suggested for shafts whenever possible.
The suggested finish for ground and turned surfaces is:
?Inner ring seats ?
Ground: 1.6 Ra micrometers
(65 micro-inches) maximum.
?Inner ring seats ?
Turned: 3.2 Ra micrometers
(125 micro-inches) maximum.
?Outer ring seats ?
Turned: 3.2 Ra micrometers
(125 micro-inches) maximum.
Bearing seat finishes rougher than these limits reduce the contact area between the bearing and the seat. This can create a more loose fit, especially if the ring is pressed on and off several times.
Mounting
When heating tapered roller bearings, inner ring temperatures should not exceed 120oC (250oF) for standard class bearings and 66oC (150oF) for precision class bearings. Higher temperatures can change the bearing?s hardness and geometry.
Aluminium or magnesium housed outer rings require a tight fit. To ease installation, they can be reduced in size by freezing. Standard class bearings should not be chilled below -54oC (-65oF), and precision class not below -29oC (-20oF).
Whenever inner or outer rings are heated or cooled during assembly after mounting and returning to room temperature, they should be checked with a 0.001-0.002 inch feeler gauge.This ensures that the inner ring is pressed tightly against the shaft shoulder (Fig 9) or the outer ring is pressed tightly against the housing shoulder.Before checking, ensure that both the inner and outer rings are pressed tightly against the shaft or housing shoulder.
When using a press to install bearings, avoid damage to the inner ring assembly. Tapered roller bearings should be separated (the inner ring assembly removed from the outer ring) during installation. When installing the inner ring assembly, use great care to ensure that no force is applied to the cage or rolling elements.
Tapered roller bearing adjust?ment techniques
One advantage of Timken tapered roller bearings is that their setting can be adjusted for better performance in a given application. Some applications require a pre-load setting while other applications require end play. The amount of preload or end play depends on the particular application.
The proper bearing setting depends on many application requirements, including the flexibility of the housing and shaft, lubrication, speed, desired life and others. To determine the optimum bearing setting, refer to the original equipment manufacturer?s maintenance and repair literature to determine the setting used in the original application.
Methods of measuring bearing settings
When bearing pre-load is required, the most convenient way to determine the preload is to read the torque from the shaft?s rotation. To measure torque, wrap a string around a gear or other known diameter (Fig 10). Attach a spring scale to the string and pull the spring scale to rotate the shaft at a slow, steady aped. Read the force indicated on the spring scale. Multiply the force times the radius to determine the bearing torque.
You can obtain a direct torque reading by using a torque wrench (Fig 11 and 12). If necessary, you can convert torque into preload force or dimensional preload.
Bearing end play
If bearing end play is required, then a different method must be used to measure the amount of end play.
Locate a dial indicator against the end or shoulder on the shaft to measure the amount of axial movement (Fig 13). Load the shaft in one direction and oscillate it several times while the load is applied. A handle can be mounted on the shaft to make it easier to apply the load while oscillating the shaft. Oscillate the shaft at least 20 times to firmly seat the bearings and ensure an accurate reading.
After seating the bearings in one direction, set the indicator to zero. Then apply the load in the opposite direction, oscillating the shaft as before, and read any movement on the indicator. The difference between the two readings is the end play.
Adjusting the bearing
These are two common bearing adjustment methods: threaded shaft with a nut and a housing with an outer ring follower. If end play is desired, back off the nut until no drag is felt. If the bearings are to be preloaded, advance the nut until the required torque is measured on the shaft.
Where shims are used, the bearing is set by tightening the end cap or bearing outer ring follower without shims in place until the bearings bind slightly while rotating. The gap between the end plate and the housing is measured with a feeler gauge. This gap plus the desired end play will determine the total shim pack required.
Fitting practices
Stationary cone fitting practice depends on the application. Under conditions of high speed, heavy loads or shock, interference fits using heavy duty fitting practice, should be used. With cones mounted on underground shafts subjected to moderate loads (no shock) and moderate speeds, a metal to metal or near zero average fit is used. In sheave and wheel applications using underground shafts, or in cases using ground shafts with moderate looseness which varies with the cone bore size is suggested. In stationary cone applications requiring hardened and round spindles, a slightly looser fit may be satisfactory. Special fits may also be necessary on installations such as multiple sheave crane blocks.
Rotating cup applications where the cup rotates relative to the load should always use an interference fit.
Stationary, nonadjustable and fixed single-row cup applications should be applied with a tight fit whenever practical. Generally, adjustable fits may be used where the bearing setup is obtained by sliding the cup axially in the housing bore. However, in certain heavy duty, high load applications, tight fits are necessary to prevent pounding and plastic deformation of the housing. Tightly fattened cups mounted in carriers can be used. Tight fits are suggested when the load rotates relative to the cup.
To permit through boring when the outside diameters of single-row bearings mounted at each end of a shaft are equal and one is adjustable and the other fixed, it is suggested that the same adjustable fit be used at both ends. However, tight fits should be used if cups are backed against snap rings, to prevent excessive dishing of snap rings, groove wear and possible loss of ring retention. Only cups with a maximum housing fillet radius requirement of 1.3 mm (0.005 in) or less should be considered for a snap ring backing.
Two row stationary double cups are generally mounted with loose fits to permit assembly and disassembly. The loose fit also permits float when a floating bearing is mounted in conjunction with an axially fixed bearing on the other end of the shaft.
The fitting practice tables that follow have been prepared for both metric and inch dimensions.
For the inch system bearings, classes 4 and 2 (standard) and classes 3, 0, and 00 (precision) have been included.
The metric system bearings that have included are classes K and N (metric system standard bearings) and classes C, B, and A (metric system precision bearings).
Precision class bearings should be mounted on shafts and in housings which are similarly finished to at least the same precision limits as the bearing bore and OD.High quality surface finishes should be provided.
Two row and four row bearings, which are provided with spacers and shipped as matched assemblies, have been preset to a specifically bench end play. The specific end play setting is determined from a study of the bearing mounting and expected environment. It is dependent on the fitting practice and the required mounted bearings setting. Failure to use the designated fitting practice in the bearing application can result in improper bearing performance or sudden malfunction of the bearing, which may cause damage to machinery in which the bearing is a component.