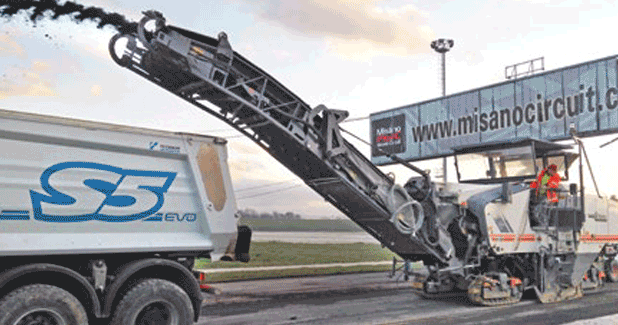
Making Faster and Safer Tracks
To make the 'Marco Simoncelli' Misano World Circuit faster and safer, Pesaresi Giuseppe SpA decided to take advantage of the cutting-edge technologies of Wirtgen and Trimble. In less than three weeks, all irregularities were removed from the track, leaving it ready for more spectacular motor sports competitions.
The 'Marco Simoncelli' Misano World Circuit is a motorcycle race track in the Italian town of Misano Adriatico in the Emilia-Romagna region on the Adriatic Riviera, a few kilometres to the south of the provincial capital Rimini. Since 1991, the town has regularly hosted the World Superbike Championships and - since 2007 - the San Marino Grand Prix.
When Santa Monica SpA issued a call for tender to modernise the track, the construction of two new track sections was also planned. These plans additionally included measures to enhance safety as well as increase the speed.
Winning the race
The person responsible for optimising the race track was Jarno Zaffelli, owner of Dromo Italian Applied Circuit Design, one of the world's leading experts in race track design. Pesaresi Giuseppe SpA from Rimini, a company that has specialised in road construction projects for more than 50 years, was commissioned with carrying out the work.
The goal was to pave around 5,000 t of new road surface - a job requiring 80 workers and 50 vehicles. The demands were high. In addition to changing the longitudinal and cross slope of the track, all existing undulations and other irregularities had to be rectified. The use of 3D technology was expressly stipulated in the technical specifications during both the planning and the implementation phases, in order to ensure the necessary precision.
The milling depth needed to be adjusted with millimetre accuracy during the milling work to remove all irregularities from the track. It was the only way to ensure that the surface of the finished asphalt track was absolutely even. This prompted Pesaresi Giuseppe to select its Wirtgen W 210 cold milling machine for this job, together with a 3D solution from Trimble.
Delivering perfect results
Once the terrain had been surveyed in collaboration with a topology and engineering construction company, the exact 3D terrain profile for the Wirtgen cold milling machine W 210 was created and uploaded. Equipped with the Trimble PCS900 paving control system, the W 210 was then able to achieve outstanding precision down to the last millimetre using the 3D profile.
Trimble 'Hot Swap' technology ensured instant transitioning between the individual total stations for uninterrupted milling work. As a result, no bumps were caused by the machine stopping on the track.
The Wirtgen cold milling machine, W 210 is the ideal choice for fast and economical handling of such construction projects, as milling drum units with working widths of 1.50 m, 2.0 m and 2.20 m and selectable milling drum speeds mean that the compact large milling machine can be flexibly modified on the job site to cater to local conditions. A high milling performance, optimum manoeuvrability as well as the fuel-saving drive concept with two diesel engines ensure maximum economy in all working situations.
The use of 3D technology also speeds up job processing, as the trucks do not have to avoid stringlines or stakes and they can move faster and more easily on the surface when transporting material away.
Fast, successful job completion
Work was completed in as little as 14 working days, following which the asphalt paving work could begin. Just four days later, the entire job was finished - on time and in compliance with all specifications. The new track is now completely smooth. What's more, with the additional track sections, all spectators on the grandstands will now have a much better view of the entire course. This project has paved the way for more spectacular, world-class motor sport competitions.
'The use of 3D technology speeds up job processing, as the trucks do not have to avoid stringlines or stakes and they can move faster and more easily on the surface when transporting material.'