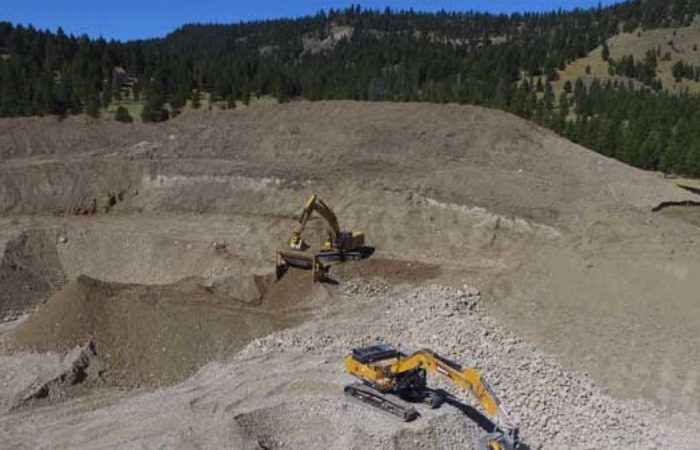
Making mission possible
Carrying a crusher on a helicopter
With the Bavarian Alps in the background: a lodge at a 1,844 m (6,050 ft) summit needed to be partially demolished and rebuilt, this is also the starting point of a very long hiking trail. Traditionally the demo waste material would have to be hauled downstream and discarded.Solution: They used a BF60.1 MB mobile crusher to process the material and use it as road base for the surrounding paths. How did they bring it to the lodge when a helicopter can only carry a maximum of 1,200 kg? A few of the crusher bucket’s heavier components were removed and then reassembled quickly on site.
Result: Significant savings on both waste disposal and hauling fees, and reuse of the resulting material directly on site.
To demolish a 16 floor building
In the centre of a large city in Japan, the goal was to tear down a 16-floor reinforced concrete building, surrounded by other properties and city life. Compact and agile machines were required to work on the roof of the building to demolish it one floor at a time. The demo waste was then tossed down a hole that was opened in the centre of the building, to protect the surrounding area.Solution: they chose a BF70.2 MB mobile crusher that processed reinforced concrete in a narrow space. The crusher bucket was lifted to the 16th floor with a crane: thanks to the unit’s size and weight this task was very easy.
Result: Material hauling time saved, and significant reduction of dust and sound emissions.
To build an underground drainage canal
In Southern California in Mexico, to avoid flooding a high traffic road, an underground drainage canal had to be constructed. The long, difficult, and dark tunnel didn’t allow access to the traditional equipment used on similar projects, and the use of a hammer would have caused excessive vibrations.Solution: They used an MB-R500 drum cutter to dig a tight and long tunnel, a compact machine packed with power. Result: No vibrations or cracked walls, and a precise removal of only the required material.
Saving cost while developing new site
In a vast area in Montana, in the US, a contractor had the task of preparing the site of a new residential area. During the excavation phase they ran into large amounts of river rock.Solution: They used a BF120.4 mobile crusher to break down river rock for immediate reuse as fill.
Result: Savings on hauling and material handling fees while eliminating buyback expenses. They estimated tens of thousands of dollars of savings.
Quick and precise moving of hazardous material
A hazardous material recycling company in Latvia needed a tool to handle large drums containing diesel fuel and paint.Solution: They used a MB-G900 grapple to easily grab hold and position the containers.
Result: Saved on both time and trucking, more work in safety and with a higher profit.