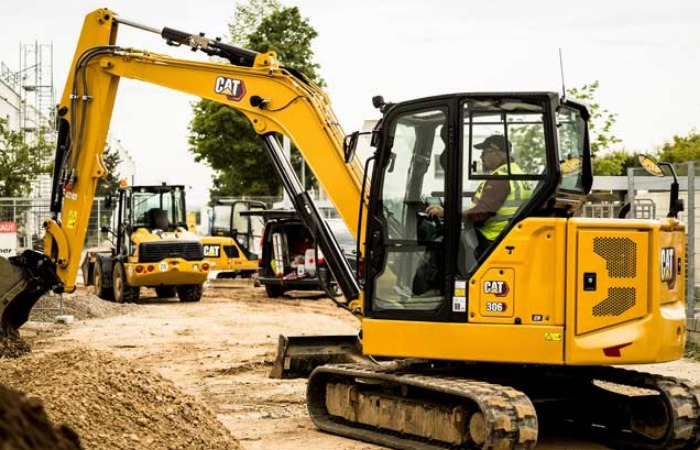
Mini Machines, Maximum Demand
Compact machines span mini excavators, mini compactors (rollers) and skid-steer loaders. All eyes are on this niche segment in India because demand for compact machines has been growing contrary to the overall declining trend in the construction equipment industry.
Last year, demand for construction equipment was down around 20 per cent while the market for compact equipment was up by 20 per cent, observes Ramesh Palagiri, Managing Director & CEO, Wirtgen India.
Palagiri expects this demand upswing to continue, despite the impact of COVID-19, driven by projects in confined spaces and smaller jobs. Some industry experts cite the shortage of workers as a potential reason for growth in the mini and compact machine segment. But Palagiri points out that expansion in previous years happened irrespective of the shortage of labour.
In the current atmosphere, Rahul Shorey, Head Sales, Construction, Tata Hitachi, believes hirers are unlikely to make any major decision to invest in machinery (unless justified for captive use), much less mini excavators, which is an evolving market. However, in the long term, he expects demand for mini machines to continue to expand faster than the rest of the market.
Let’s examine the prospects of different mini machines.
Compact excavators: Compact excavators are similar to regular excavators in structure, with a crawler undercarriage and revolving superstructure fitted with a boom, arm and bucket as the front attachments. However, they differ from regular excavators by being able to perform in an extremely compact space and reach worksites with a narrow approach road—either by being driven to site or transported on a pickup or a mini truck, explains Shorey.
“Sales of mini excavators in India crossed the 1,000-unit mark in 2018,” he observes. “Mini excavators make up 5 per cent of the excavator market.”
Tata Hitachi’s mini excavator range includes the indigenously developed 2-tonne TMX20 and the zero tail swing models: the 2-tonne ZAXIS 20U and the 3-tonne ZAXIS 33U. The zero tail makes the machine more compact and therefore easier to transport and well suited for trenching in confined spaces.
“Indigenous models are better from the service and spare parts point of view—as these are readily available,” opines Shorey.
“JCB’s full range of mini excavators (JCB30Plus, JCB50Z, JCB51R and JCB55Z) is designed and manufactured in India, at the company’s Jaipur plant, for a tropical/semi-tropical climate and arduous applications,” explains Jasmeet Singh, Head, Corporate Communications and Corporate Relations, JCB India.
JCB’s mini excavators fall in the 3 tonne and 5 tonne operating weight category.
“Domestic (made in India) world-class manufacturing gives customers multiple options to choose from and more value-added features such as a pre-fitted auxiliary hydraulic circuit for the fitment of a hammer and auger drill, and a range of different sized buckets,” adds Singh. “Domestic manufacturing also gives customers seamless serviceability and product support.”
So far, Shorey observes that the use of mini excavators has generally been driven by the high cost of labour in urban and other areas. Therefore, the market is concentrated in the south, largely Kerala, where labour is expensive.
With increasing use, however, appreciation is growing for the compact size of the machine, its higher safety in operation and efficiencies—both in fuel and usage—which in turn is further driving the use of mini excavators. Shorey points to the use of mini excavators even in labour-dominated states like Bihar, which is interesting because, conceptually, mini excavators are built to do work that can mostly be performed only by manual labour. He believes this switch is being driven by the need for speedy, high-quality work, which can be assured by mechanisation.
Among the potential areas of application in the construction industry, Singh lists “urban infrastructure development projects like smart cities, Atal Mission for Rejuvenation and Urban Transformation (AMRUT) and metro rail projects; building foundation digging and multi-storied building projects needing the removal of debris from basements; and industrial projects like oil refineries, ports, steel plants, etc. Municipal corporations/councils and contractors needing compact machines to clean muck from roadside drains would especially benefit from the mini excavators’ unique boom offset feature that facilitates straight-line working without frequent repositioning of the machine.”
“Outside urban areas, there is growing awareness of the utility of mini excavators for tasks like long-distance trenching to lay pipelines for water, sewerage or gas, to lay pipelines along the narrow roads of a village or a town, to build septic tanks, or for irrigation projects to descend the bank of small canals and scoop out silt,” he adds.
In future, Shorey predicts that the Jal Jeewan Mission, with its motto Har Ghar Jal, will also be a big driver of demand for mini excavators, as in many villages, accessibility to houses for laying drinking water pipes is available only to such machines.
Compact compactors: Compact compactors offer a host of features. These machines from Wirtgen group company HAMM offer high gradeability (up to 60 per cent) and maximum ground clearance thanks to the drive provided by modern wheel motors. The modern motors with future-proof technology in HAMM’s compact compactors also ensure extremely low emissions. These are very short, making them ideal for narrow construction sites and compaction work on rough terrain.
“CASE India’s mini 450 DX double-drum roller has also been designed to work in extreme terrains and operate in demanding situations, hence demand for this machine is driven by infrastructure and urban projects such as roads and highways, bridges and transportation,” shares Puneet Vidyarthi, Brand Leader, CASE India.
A few prestigious projects where CASE India’s machines are currently being deployed include Sagarmala, Bharatmala, Pradhan Mantri Gram Sadak Yojna and Trilateral Highway (India-Myanmar-Thailand highway).
Projects in confined spaces and for smaller jobs are drivers for compact compactors, says Palagiri. HAMM’s H-series compactors are high-performance professionals for modern earthwork with a high compaction force. Off-road, their three-point articulated swivel joint and large slope angle front and back make them extremely manoeuvrable while ensuring optimum driving stability.
As for CASE India’s SR130 skid-steer loader, demand is being driven by urban infra projects. “Its compact structure facilitates work efficiently in tight spaces and boosts productivity,” shares Vidyarthi.
While HAMM compactors are currently imported from Germany, CASE India is manufacturing mini drum rollers at its world-class Pithampur facility for both the domestic market as well as for Africa, Southeast Asia, Russia, the Middle East, etc. However, CASE India’s skid-steer loaders are imported. Greater indigenisation would bring down the cost of this class of equipment and expand demand—something to look forward to.
Courtesy: Construction
World