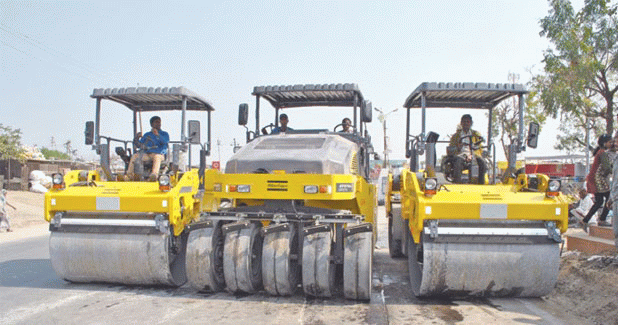
On Course for Success
Road construction is driving the Indian compactors market. This is expected to continue. ?Most of the current demand for both soil and tandem compactors is for road projects,? says Ramesh Palagiri, Managing Director & CEO, Wirtgen India. ?Compaction is one of the most important processes in road construction, as also in airport, railway embankment, port and irrigation construction to achieve the desired load bearing capacity of soil.?
?India has the world?s second largest road network, but it is in clear need of significant upgrade and expansion. So the brightest opportunities for compactors are unquestionably in the road building sector. Last year?s government announcement that it will target 30 km road construction a day for 2016 is very welcome,? opines Dimitrov Krishnan, Vice President and Head, Volvo CE India.
?Vibratory compactors demand reflects the progress of the road sector,? says Ajay Aneja, National Head of Sales, CASE India.
Soil and heavy tandem compactors also find application in the airport segment, observes Vipin Sondhi, Managing Director & CEO, JCB India. ?But still the road segment will demand greater numbers of compactors than airports, and those opportunities will span all three types of compactors - soil compactors, heavy tandem rollers and mini-tandem rollers.?
?Compactors will mainly be in high demand for road and airport projects as more and more greenfield and relaying projects enter the pipeline,? says Hiten Kapadia, Business Line Manager, Atlas Copco Road Construction Equipment. ?Irrigation and railway projects will take some time to take off. All these sectors need to grow simultaneously to improve the country?s infrastructure and for real economic growth to be experienced.?
?Planned roads and highway projects and smart cities will boost demand,? adds Palagiri.
Demand: Today, tomorrow
Demand for compactors hasn?t grown much in the last decade. ?India?s market for compactors has hovered around 2,500 units per year for the last decade,? opines Palagiri.
?Over the last five years, the compactor market has been in the range of 2,200 to 2,600,? says Kapadia. But the market started to pick up in the second half of 2015, according to him. ?Demand crossed the 2,600 threshold. We expect demand to grow to more than 3,000 units in 2016.?
The last three years have experienced a straight fall in volume. ?However, 2015 witnessed less de-growth on a Y-o-Y basis, which indicates green shoots in 2016,? says Aneja. ?We utilised the slowdown to prepare for the next growth wave, which is imminent. We invested in Research & Development, manufacturing quality and process improvements at our plant in Pithampur, and in the launch of new models including the new CASE 1107DX soil vibratory compactor and an improved version of the highest selling tandem compactor, CASE 752. We improved our market share in the vibratory compactor segment on a Y-o-Y basis.?
The general consensus is demand is heading upwards and could even double by 2020. ?India?s annual market for compactors hovers between 2,000 and 2,500 units, across all classes of compactors - double drum and single drum (soil and asphalt) and mini compactors. We expect the market to touch 3,500 units over the next three years,? says Krishnan.
?Compactor sales in 2015 crossed 2,300 units. By 2020 we expect the market to touch about 4,000 units,? says Sondhi.
?CASE is likely to clock sales of 2,100 to 2,400 compactor units in 2015 and exceed 3,000 units by 2020,? says Aneja.
Popular choices
A look at the compactor market shows demand focusing on versatile, highly productive and low maintenance models.
?Road contractors want machines that can complete a project as cheaply and quickly as possible. They also want faster cycle times, reliability and versatility,? says Krishnan. ?We?re seeing a drive towards greater efficiency, with customers demanding greater usage from equipment than ever before, for which they are looking more closely at aspects such as fuel efficiency, uptime and productivity to guide their work.?
?Compactors with improved reliability and fuel efficiency, which promise performance and productivity, play an important role in buying behaviour,? opines Palagiri.
Volvo CE?s most popular soil compactor in India is the SD110 (11 tonne), a powerful and versatile unit that is suited to a lot of projects. ?Operators are able to easily adjust the drum vibration frequency to cater to changing soil types and conditions. The unit also has balanced weight at the drum and tires, for better traction,? shares Krishnan.
Volvo CE?s DD100 asphalt compactor is its most popular in India (10 tonne). According to Krishnan, ?It helps road contractors get the job done in the fewest number of passes, boosting productivity. It is easy to switch between settings, so the operator can adjust the machine?s performance to suit conditions.?
?Popular models in the Indian market, which are also made locally, include the LP6500 walk behind double drum rollers for excellent compaction efficiency in confined spaces, the CC125 3 Ton ride on baby roller offering excellent visibility, operator comfort, low operating and maintenance costs; the CA255, (11 tonne soil) compactor to achieve the end result in minimum passes, and the highly-productive and fuel-efficient CC425, 9 tonne tandem roller,? says Kapadia.
?Customers look for low turning radius, for high manoeuvrability in constricted spaces, fuel efficiency and advanced hydraulics, high drum shell thickness for a robust drum with longer life (17 mm in the CASE 752, 12 mm in the CASE 450DX and 32 mm in the CASE 1107DX), high compaction force to achieve the desired compaction in the minimum number of passes,? says Aneja. In tandem rollers, the Case 752 develops a force of about 25 tonne while the Case 450DX develops 6 tonne. The Case 1107 DX features a compaction force of 34 tonne which is highest in its class.
Feature wise
GPS systems, compaction metres, temperature sensors and cutting edge technology are features that are gaining popularity.
?GPS systems are becoming popular in soil compactors and tandem rollers so that contractors can better monitor their machines with the idea of getting more out of them,? says Sondhi.
?Buyers are also looking for soil compactors with compaction meters, to cut down on the passes needed and boost productivity. Tandem rollers with temperature sensors are in demand, to lower the possibility of too much water being used to maintain the roller?s temperature, as that would damage the top layer. Buyers are also asking for edge cutters in tandem rollers for better finish,? shares Sondhi.
?Customers are also increasingly aware about operator safety and comfort, O&M costs, new technologies like intelligent compaction, Hamm Compaction Quality system for Hamm compactors, 3-point articulation for directional stability, even weight distribution on drum and wheels and driving comfort, and cutting edge technology,? says Palagiri.
Bigger is better
Technology enhancements can drive demand for higher capacity equipment and more purposeful machines.
In tandem rollers, Sondhi speaks of a gradual shift in demand for higher tonnage machines-?9 to 10 tonne class tandem rollers against the 8 to 9 tonne class earlier.? In soil compactors, 11 tonne models have been and continue to be the most preferred, Sondhi adds.
As the pace of road construction picks up, companies will focus more acutely on speed of work and capacity, to meet stringent deadlines. Then, Kapadia expects demand for high capacity machines to increase because these models can optimally handle thicker layers with a powerful engine, wide frequency and amplitude range.
They can reduce operator fatigue while saving on fuel, time and the number of operators. In India, Atlas Copco already offers the market?s biggest pneumatic tyred roller, the Dynapac CP275, a 9-tyre, 14 tonne PTR with ballast up to 30 tonne. Both sides of the CP275 tyres are wider than the frame thus yielding excellent edge compaction. ?This is just the start,? says Kapadia. ?Other higher capacity rollers from our global fleet will eventually enter the Indian market, as the road construction market matures.? Better times and a wider variety of choices lie ahead.
Ministry rules: What size compactors do MoRTH and NHAI projects specify?
?MoRTH and NHAI projects specify the use of minimum 10 tonne single drum rollers for earthwork, 8 to 10 tonne capacity double drum rollers for asphalt work, and 2.5 to 3 tonne mini tandem rollers for highway shoulders,? says Vipin Sondhi, Managing Director & CEO, JCB India.
?2-3 tonne tandem compactors are also specified for confined areas,? adds Ramesh Palagiri, Managing Director & CEO, Wirtgen India.
?Generally speaking, MoRTH and NHAI projects specify 11 tonne soil compactors and 9 tonne asphalt compactors,? opines Dimitrov Krishnan, Vice President and Head, Volvo CE India. Buyer?s preference
?We evaluate compactors for their engine, emission norms, engine power, operating weight, drum width, speed range, vibration frequency, tyre size, fuel tank capacity, gradeability, number of cylinders, nominal amplitude, etc.? shares Kumaravel Seethapathy, Assets Manager, Plant & Machinery, Ramky Infra Ltd. ?On this basis we prefer machines that feature Cummins engines, high drum width, high operating weight, comply with BS III emission norms and other desirable parameters.? Popular compactors in the market are models from Wirtgen, Greaves, JCB, L&T, Caterpillar, Dynapac and Volvo, according to Seethapathy.
?Vibratory compactors are best suited for road and airport projects. They come in two types: smooth drum and padfoot drum. However, for increased versatility, we prefer smooth drum compactors equipped with optional padfoot shell kits. This allows the use of smooth drum rollers in padfoot applications, albeit with limited performance,? shares Krishna Prasad Narasimhan, Engineer Plant & Machinery, Megha Engineering & Infrastructures Ltd.
?We prefer soil compactors with net power 173 Kw and 302 Kw and pneumatic rollers of capacity CW 34 and ps150c torque because these offer greater productivity. We look for time-saving features: models with rammers (bounce up and down), walk-behind plate compactors (light/heavy with reverse), trench rollers (manual unit or radio-frequency remote control) and walk-behind rollers (light with single drum/heavy with double drum).?
To get the most out of your compactor, base your choice on your past usage experience, the type of soil, the project method specification and the equipment you have available, suggests Krishna Prasad.
?2015 witnessed less de-growth on a YoY basis, which indicates green shoots in 2016.?
- Ajay Aneja, National Head of Sales, CASE India
?Opportunities span soil compactors, heavy tandem rollers and mini tandem rollers.?
- Vipin Sondhi, Managing Director & CEO, JCB India
Industry expectations from the government
Ajay Aneja, National Head of Sales, CASE India, outlines a wish-list to improve the prospects for compactors, and for the construction equipment industry as a whole:
- Allocate more funds to infrastructure to encourage construction companies to match global standards.
- Remove dual taxation by recognising leasing as either a ?good? or a ?service?.
- Set up skill development institutes for construction equipment operators to further the usage of construction equipment in Indian infrastructure development.
- Provide incentives for infrastructure companies to adhere to quality and timelines of a project while moving away from L1 criteria as the sole selection criterion.
?Generally, MoRTH and NHAI projects specify 11 tonne soil compactors and 9 tonne asphalt compactors.?
- Dimitrov Krishnan, Vice President and Head, Volvo CE India