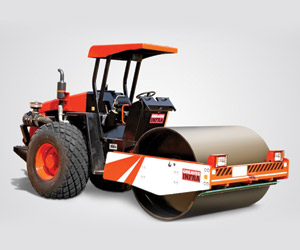
Our advantage lies in our compaction efficiency
Could you tell us about the technological features of the BW212-2(2A)?
By and large, I can say that we have done some good development work on our machines. We are now bringing out machines with water-cooled engines which on proto-testing, was found be to best-in-class in fuel efficiency. And we have an advantage with our compaction efficiency, also.
We have done extensive trials on our in-house, water-cooled engines and we have gone through the process of validations and efficient control compliance. These water- cooled engines are highly efficient in terms of maintenance and operations cost, as well as offering lower diesel consumption. Regarding the last, the customer will be benefitted by savings of about 3-4 litre diesel consumption per hour. And in terms of compactions, a lot of parameters are required like operational frequency, amplitude, vibration frequency, the static linear load and the speed of travel. So it depends upon the soil and the type of frequency and amplitude you are setting to get optimum compaction. Our compactors are the best in this class and we get around 98 per cent compaction.
For the operators, we give a one-by-one visibility that is the required objectives of one-metre height in the front and rear. It gives the operator clear visibility in the forward as well as reverse direction. So, if he is operating in both directions, he can finish the job safely and fast. One aspect we should mention is that our soil compactors come with a higher drum thickness of about 36 mm, which is the highest in the category. Our hydraulics are originally from Bomag, the global leader in terms of compaction technology. This really adds to the compaction efficiency we deliver.
Are you going to be introducing more variants?
When we talk about variants, there are two things that we can do. One is basically the higher class of machines, say in soil compactors move to a 16 -tonne machine or a 19-tonne machine; today, we predominantly switch between 9 to 12 tonne. And similarly in heavy tandem rollers, you only move to a higher tonnage of machines. In India, we have not moved to a higher tonnage of compaction equipment. So from that perspective, I would say the market is not ready to move to a higher capacity of machines.
The other thing is there are other variants like standard machines of a non-drum drive where the drum doesn't have an independent drive and only does the compaction. There is another variant called the drum drive where the drum is driven in addition to the axle power. This machine is typically used for more difficult terrain because they are powerful machines which can take higher inclines. And the third is the padfoot, which is actually an attachment put on the drum. So these are the three variants which are currently in the market and we offer all three variants, different for each application.
How have you addressed the issues of different size of aggregates like coarse, mid size and fine?
We have the same variants of machines; the variants don't change based on the mix of the size that you use. If you have a good combination of linear load frequency and amplitude, it takes care of the compaction. We have a very good compaction frequency of around 31 Hz which gives a good setting of the rude soil. Our front drum module is of the highest tonnage, our front to rear module is around 60-40 which gives very high compaction. And with a 36 mm drum thickness, our total tonnage comes to around 5.7 tonne, which makes for very good compaction.