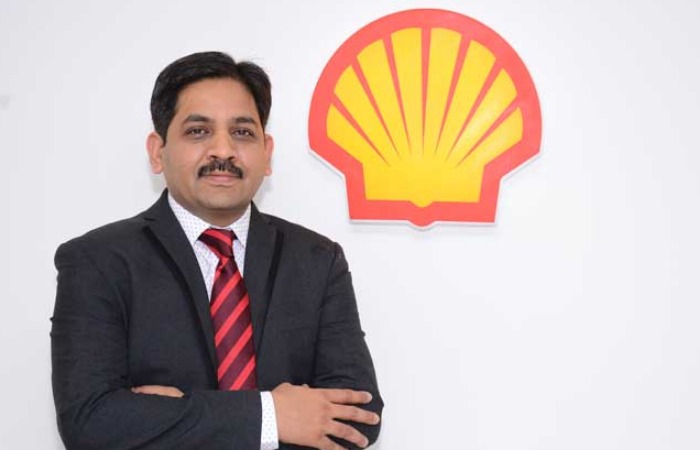
Our focus has expanded to encompass complete oil life cycle management: Praveen Nagpal, Shell
How does your product range ensure the efficiency and uptime of construction equipment through effective lubrication?
Shell’s high-performance lubricants are engineered to maximise protection and ensure the optimal performance of construction equipment, even in the most challenging conditions. Utilising advanced technology, these lubricants drive efficiency and help customers maximise the capabilities of their machines.
For example, Shell Tellus S4 VE hydraulic oil, derived from gas-to-liquid technology, reduces energy losses from hydraulic pumps. Additionally, Shell Gadus S3 V460D 2 high-temperature grease enhances efficiency and extends service intervals, resulting in significant cost savings.
To ensure smooth operation and maintenance of construction machinery, Shell offers expert technical support and digital lubricant solutions, enabling a proactive approach to maintenance. This comprehensive support reduces the impact of unplanned downtime and maintenance costs, contributing to more reliable and cost-effective site operations.
What are the primary factors that construction equipment customers prioritise when selecting lubricants?
Shell's approach to helping customers achieve optimal costs of ownership, reduce emissions, and ensure maximum equipment availability and reliability is grounded in the use of high-quality lubricants and expert lubrication management. Customers can realise significant savings through effective lubrication, which can increase oil change intervals and prevent unplanned equipment downtime. Shell’s integrated solutions address diverse needs related to energy, services, and sustainability, helping improve the Total Cost of Ownership (TCO) by keeping equipment running at peak performance, even under challenging conditions.
Lubricants that provide fuel and energy efficiency benefits, along with extended oil drain intervals, are crucial in reducing operational and maintenance costs, downtime, and emissions. Shell’s consultants, who are trained specialists, work closely with customers to understand their specific business operations, plants, and personnel. They analyse and optimise the impact of lubrication to achieve long-term cost reduction.
There are two core elements to this approach: first, ensuring every piece of equipment uses the right lubricant and second, managing lubrication effectively. This involves providing customers with the necessary training, maintenance solutions, and lubrication handling and analysis, ultimately empowering them to achieve optimal performance and cost savings.
With new emission regulations already impacting the commercial vehicle market, what features have you incorporated into your lubricant range to comply with these regulations?
Shell Lubricants has been a leader in developing next-generation heavy-duty engine oils globally for years. We have ensured that our systems are agile and ready to meet regulatory reforms, allowing us to stay ahead of changes and meet new standards effectively. Our products, such as Rimula R5 and the Fleet NX series, are formulated with advanced additive technology to protect exhaust after-treatment systems, reduce harmful emissions, and improve combustion efficiency.
Designed to enhance fuel efficiency, these products deliver significant value to our customers. Rimula R5, for instance, has more than doubled the drain interval (by 122 per cent) and delivers substantial fuel savings of 2.1 per cent*. As fleets in the construction and mining sectors upgrade to new technology for better fuel economy and lower emissions, our next-generation FA-4 products/molecule are already proven to meet even more stringent future regulations.
By integrating these advanced features, we are setting new benchmarks for the industry while ensuring compliance with existing regulations. Our goal is always to help our customers stay ahead in a rapidly evolving market.
How are you developing lubricants tailored for off-highway applications?
With decades of experience in collaborating with off-highway businesses to maximise machine efficiency, we provide integrated lubricant solutions designed to help customers optimise their lubrication practices. Our long-standing OEM partnerships allow us to co-engineer innovative products and solutions, giving us access to valuable insights and industry trends that enable us to tailor our offerings for the off-highway segment.
Our tailor-made solutions stem from an insights-based approach, incorporating feedback from OEMs, regulatory bodies, and end users. These solutions undergo a rigorous screening process in laboratories, test rigs, durability tests, advanced analytical testing, and extensive field validations. Through this comprehensive and dedicated approach, we ensure our lubricants deliver superior performance and protection, meeting the demanding requirements of off-highway applications.
What other innovations are occurring in lubricants specifically designed for off-highway applications?
While digital innovation has transformed construction sites and off-highway spaces, our focus has expanded to encompass complete oil life cycle management. This shift aligns with our customers’ increasing emphasis on high productivity, reliability, and emission reduction. By adopting a holistic approach, we are pushing beyond conventional practices to offer innovative solutions that span the entire life cycle of lubricants. These innovations include energy-efficient lubricants, onsite and off-site predictive maintenance, AI-powered solutions, waste management, recycling, and reusing recycled products.
For instance, we are scaling up services like MachineMax, which utilises equipment telematics to optimise fleet usage and minimise fuel wastage in the construction industry. Additionally, Shell RemoteSense, our live oil condition monitoring service, leverages IoT, machine learning, and data science to provide real-time health monitoring of machinery and oil, generating actionable insights. Shell LubeOptimiser offers comprehensive onsite solutions for total fluid management and fluid reliability services.
To advance the circular economy within the lubricants industry, Shell has partnered with used oil re-refiners to initiate used oil collection and re-refining across India. A key initiative in this regard is Shell’s used oil management service, which aims to organise India's waste oil disposal system, increase the re-refining rate, and achieve circular economy goals while reducing waste.
Are there any additional insights or aspects regarding industrial lubricants that you would like to share?
Effective lubrication can drive substantial business value by enhancing productivity and cutting costs, though its impact is frequently undervalued. To fully harness this potential, two key factors must be addressed. First, ensuring every piece of equipment uses the appropriate lubricant and second, managing lubrication effectively. This involves equipping customers with the necessary training, maintenance solutions, and methods for lubrication handling and analysis.
Our goal extends beyond merely supplying lubricants; we strive to offer integrated solutions that aid our customers in improving their total cost of ownership. Additionally, we focus on addressing diverse needs related to energy, services, and sustainability.