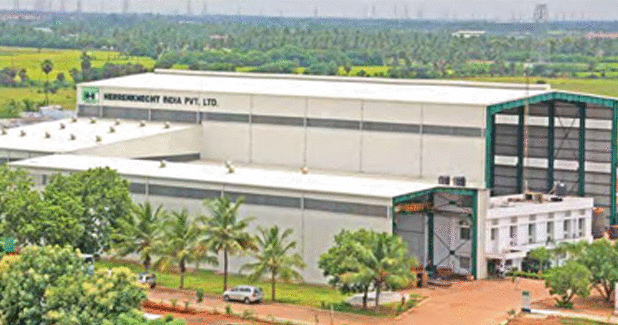
Positive on Indian Market
Since 2007, Herrenknecht has been represented in India with its wholly owned subsidiary Herrenknecht India in Chennai, Tamil Nadu. There are about 90 employees to support projects and customers quickly and competently. In December 2011, a new building at the premises expanded the company?s storage, steel construction and assembly capacities - a total of 3,700 sq m- for the growing Indian market. Herrenknecht is present in two distinct tunnelling segments: Traffic and Utility. ?First of all, this nomenclature is by Herrenknecht. These are two verticals of our company. In Traffic tunnelling, the TBM comes in more than 4.2 m in diameter. The other type is for utilities because any tunnel below 4.2 m dia generally not used for any transportation purposes. Utilities like sea outfall, sewerage, waterline and such purposes can be accommodated in the smaller tunnels. This is the rationale behind this nomenclature,? explains Manoj Garg, Managing Director, Herrenknecht India.
India operations
Initially, the company was providing Sales, Field Service and Spare support to the Indian customers. The machine building activity was started in 2010, in India. Currently, the available facilities can accommodate assembly or complete rebuild of 4-6 units at a time.
Currently, a Traffic category Herrenknecht-make 6.6 m diameter 75 m long TBM meant for metro rail tunnel application is being completely refurbished at this facility. This machine was first used at Singapore. After rebuild, the same will be exported. One witnesses a frenzy of refurbishing activity in progress.
This very complex and technically challenging rebuilding activity is duly supported by qualified and experienced experts from either Germany or other countries. These experts provide guidance and assistance during the various processes involved in the rebuild.
Impressive warehouse support
Both TBM rebuild and on-site support of running equipment are backed by a very comprehensive warehouse located at Chennai plant. The warehouse maintains adequate stocks of all cutting consumables, all fast moving items based on the recommended list provided. Some select long lead but critical items like Rexroth pumps are also kept in stock to meet contingent requirements. Other required components and spares are sourced from the available central inventory at Germany or China. A database is maintained which assists in locating the parts from anywhere in the globe. In many situations, the parts have to be manufactured to order. Obviously, delivery time for such items is much higher. Overall, the average response time is around 4-6 weeks for most parts.
Market size
?There are nearly 50 units of Traffic category TBMs operating in India. Herrenknecht has secured the largest market share of 33 units comprising different diameters, configuration and for various applications. Out of the balance 17 units, China is the major supplier,? informs Garg.
Ongoing projects
Currently, Herrenknecht TBMs are deployed in the Himalayas for a hydro power project; metro rail projects at Delhi, Chennai, Bengaluru and Kolkata and an 18 km long water transportation tunnel at Veligonda in Andhra region. They have recently completed a water tunnel in Mumbai. On the global front, the company has executed numerous tunnelling projects. Prestigious examples being the 88 km long Gotthard Tunnel under the Alps in Switzerland and 15.4 m diameter twin tunnel under the Yangtze River, at Shanghai, China.
Looking ahead
India will need lot of TBMs as there are many new projects coming up as such this facility has a lot to look for the future.
?TBM pays back if the tunnel length is optimum.?
Manoj Garg, Managing Director, Herrenknecht India.
Government needs to create a business environment to ensure that India-made TBMs become cheaper than completely imported machines, says Manoj Garg, Managing Director, Herrenknecht India.
There are two categories of TBMs: Traffic and Micro Tunnelling. How many TBMs in each category are available in India?
There are around 50 units of Traffic TBMs in India, out of which, 33 are from Herrenknecht and 17 units are supplied from competitors. China is the major supplier and some are from Robbins, US and Japanese makes.
For Micro Tunnelling, most are from HK and one other company and the total number is around 25 machines.
How do you see the future of TBMs in India?
Most of the TBMs will be used for metro projects. Such projects are being conceived for some smaller Tier II cities where metro rail is expected to go underground. In Tier I cities, metro projects are already ongoing. In roads segment, wherever you are not permitted to use Drill and Blast tunnelling or the length of the tunnel is in excess of 4-6 km where Drill and Blast creates issues, TBM is viable. Similar case for normal railway tunnels in areas like J&K, Himachal Pradesh or another kind of Konkan railway there may be some possibilities of using TBM in certain stretches. Capex for TBM is high but it pays back if the tunnel length is optimum.
For a typical 6.4 m Traffic TBM, what would be the viable length of the tunnel?
For traffic tunnelling, one has to use TBM because Drill and Blast and cut and cover method is not an option in developed cities like Mumbai because there are so many houses and existing structures.
What are the major projects underway for Herrenknecht?
We have our TBM in Himalayas also. We have completed one water tunnel in Mumbai and the other is in progress at Veligonda. In the metro projects, our TBMs are working at Chennai, Delhi, Bengaluru and Kolkata.
When you are refurbishing a TBM which has done typically 10 km of metro tunnelling, what would be the cost?
It is a very difficult question to answer. But I would say 50-60 per cent of the cost of a new similar TBM. For hard terrain application, the cost will be up to 70 per cent of the initial price as only the structures can be reused and balance is all new. The refurbished equipment carries full warranty as New TBM warrantees.
In terms of technology, how does Herrenknecht differentiate itself?
German technology and mechanical engineering is well known globally. Secondly, the inhouse knowledge base is key strength. We have experts who are highly experienced in various geologies and operating conditions. We also have data and records from our past experience. As such, whenever a problem arises, we refer to them and they always provide workable solutions.
What are the policy related challenges which can be stumbling blocks for TBMs?
Taxation is major issue. Movement of material is another big issue. If I have to transport material from Chennai to Delhi (for eg), it takes several days and sometimes if the item is big like a cutter head.it can be months! This is a criminal waste. Government has to streamline many such issues.
What support do you seek from the government?
I think the government needs to create a business environment to ensure that India-made TBMs could be cost effective compared to fully imported TBM. Currently, the basic custom duty on TBM is zero. As such nobody manufactures TBMs in India except us. This defeats the Make in India movement in this sector.
Currently, Herrenknecht TBMs are deployed in the Himalayas for a hydro power project; metro rail projects at Delhi, Chennai, Bengaluru and Kolkata and an 18 km long water transportation tunnel at Veligonda in Andhra region.
- SHANKAR SRIVASTAVA