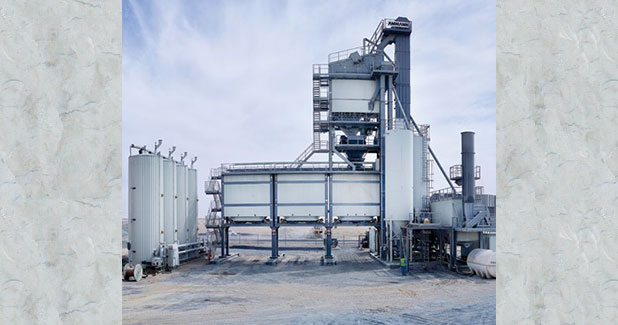
RAP Essential in Asphalt Plants
Many years ago, the asphalt mix, ?Black Mix?, was produced by heating bitumen and manually mixing the aggregates for paving roads. Mechanisation followed and integrated, computer-controlled, batch-mixing type asphalt-mix plants came up, capable of delivering complex asphalt mixes using a wide variety of ingredients. Green initiatives around the world, including India, pushed the adoption of large capacity, alternate fuel, high energy efficiency, environment emission control and automation features in these plants.
However, road builders realised that availability of adequate quantities of crushed aggregates had become a serious challenge in most projects, owing to numerous restrictions on quarrying and crushing being imposed by various administrations to contain pollution. Secondly, the existing high-grade (approved) aggregate residues on roads were simply being excavated and discarded - a colossal waste of good usable material. These discoveries and awareness have led to the use of RAP in hot-mix designs, and in turn, manufacturers are providing RAP-processing capabilities in most new-generation asphalt-mix batching plants.
Market scenario and trends
Sarvesh Prasad, Deputy General Manager - Sales, Equipment and Project Solutions, TIL Ltd, describes the transitions in asphalt mixing, ?Over a decade, there has been a gradual shift from small capacity plants to higher capacity plants, and with the movement towards higher capacity plants, stricter control on mix design and emission norms has also become a priority. Of late, plant capacities of 160 TPH and above are much more in demand as these projects have lesser time for execution. Thus, the work needs to be completed much faster and expeditiously. The major shift in technology was initiated by the National Highways Authority of India (NHAI) and Ministry of Road Transport and Highways (MOSRTH) when the infrastructure boom started in India in the ?90?s. At that point in time, the batch technology was preferred to the drum-mix technology with the objective of producing consistent mix and quality roads. The drum-mix technology is still in use in India and is predominantly used in the Pradhan Mantri Gram Sadak Yojana (PMGSY) roads and state highways.? Prasad adds, ?Drum-mix technology has evolved over the last couple of decades and many countries have adopted this technology wholeheartedly in view of the inherent benefits this technology offers over a batch plant.?
Asit Patel, Managing Director, Ammann Apollo India Pvt Ltd, points out, ?You cannot define key market trends in the asphalt plant business like you define in financial markets. The developer chooses the technology and capacity of the plant based on the ?need? for a given project. The decision on the capacity of a plant is mainly driven by the quality of asphalt required, and the timeframe for completion. Broadly, the trend is to go in for a 120-160 TPH plant for EPC projects of less than 50 km in length. For larger projects, the preference is for 180-260 TPH capacity.?
Journey of technology in asphalt mixing
Prasad says, ?The success of double-barrel technology globally is a classic example of the evolution of the drum-mix technology. The capability of the equipment to use up to 50 per cent RAP without any modification and the ease with which the plant can be operated is the reason for the success of the double-barrel technology. In India, this technology has been approved for use by NHAI and the motivation to use RAP with ease is encouragement enough for a customer to embrace this offering, as it would substantially lower the cost of road construction and also help preserve the environment. As has been proved in many countries, the state-of-the-art drum-mix technology will pave the way for the future in India as well. Further, with a retrofit called Green Pack, this plant can even produce warm-mix asphalt and has been successfully used in a few projects in India.?
Patel offers further clarity, ?Asphalt-mixing technology has come a long way in India over the past 25 years from hand-mixing to sophisticated batch-type mixing plants. The important input material for good-quality asphalt mix, for good-quality roads, is the aggregates. This is the main area of concern in India because the contractor has to source aggregates from different quarries. This makes batch-type plants more suitable to ensure end-quality, because the asphalt batch plant has a multi-deck screen to precisely screen and segregate the input material as per the recipe required for the pavement design. Hence, we have seen that, for higher- and mid-value road projects where the investment is to be protected by building good quality pavements, the batch-type plants are being recommended more and more. Warm mix is still in the initial stage in India, but has big potential to save energy and protect the environment.?
He further elaborates, ?There are several factors that affect the productivity of an asphalt batch-mix plant. The aggregate quality is most important, for which we try to educate the customer and also try to increase some buffers in the plant to increase the tolerance levels. New technology in mixing, weighing and plant controls improves continuous productivity. Hot asphalt storage silo integrated into the batching tower provides a buffer against irregular tipper movement which impacts plant productivity. Improvement in controls to provide more information and alerts to the operator helps him control the plant better for higher productivity and efficiency.?
?However, the adaptation of technology needs to be carefully done, so as to not have an adverse impact on the pavement quality,? sums up Patel, on a cautionary note.
Energy efficiency & emission compliance
Energy conservation and controlling fuel and dust emissions from an asphalt plant are important criteria for selection by users in order to meet stringent statutory regulations and repeated inspections carried out by the authorities.
Patel is committed to plant performance meeting the above mentioned, critical operational requirements. He assures, ?Improved bag-filter designs, burner designs, better control of combustion process and more efficient drum driers ensure that the plant meets tighter environmental norms. In case of continuous plant we have come out with counter-flow technology which allows the use of bag filters and more efficient heat transfer to enhance the environment compliance of continuous plants as well.?
Prasad explains in detail, ?Double barrel has incorporated various features to maintain its green quotient:
- Generous application of insulation throughout the bitumen storage tanks, bitumen pipe lines, hot oil pumps and piping, double barrel itself ? all these result in heat retention significantly and reduce the carbon footprint;
- Ability to run up to 50 per cent RAP;
- Ability to produce warm-mix asphalt using bitumen-foaming technology popularly known as Double Barrel Green System. The WMA foaming system is presently the industry standard for producing warm-mix asphalt and is a giant step forward for the industry because it uses water as an additive to produce warm-mix asphalt. It allows contractors to produce warm-mix material that is equal to hot-mix material in performance while requiring less fuel for drying and it generates fewer emissions. Double-barrel green makes the production of sustainable WMA a reality;
- Adequate capacity of bag house filter system to control emission of particulate matters results in ?zero opacity?.
Use of alternate fuels Depending upon availability of low-cost fuel in a region, users demand alternate fuels or variants in the aggregate and bitumen heating systems of a plant - like high speed diesel, light diesel oil, heavy fuel oil, gas, and in the Indian context, pulverized coal.
Usually for a vendor, catering for this demand entails modifying fuel storage, supply and burning system without making any changes to the rest of the plant. Patel confirms that Ammann?s plants are capable of handling multiple fuels. ?A wide range of fuels can be used like liquid fuels (light oil and heavy oils), natural gas, coal, wood chips, etc. The pros and cons depend largely upon the fuel prices and availability at plant location. From the point of environmental protection, light/heavy oil and natural gas are better. Coal is being used, but unless proper care is taken on the jobsite for storage and handling of coal, and unless the burner is of higher efficiency, serious environmental and safety issues can be caused at the site. Indian coal is not suitable for asphalt plants because of its high ash content, and hence one has to use imported coal only,? he says.
Prasad also confirms, ?The TIL-ASTEC double-barrel plant can use different alternate fuels like diesel, waste oil, natural gas and coal. Different fuels have various advantages - diesel with its high calorific value, would have lower consumption per tonne of hot mix produce compared to waste oil, natural gas or coal. But with waste oil and coal, production cost per tonne reduces due to their lower cost. However, emissions increase. One has to have a compatible capacity bag house filter system to control the emission.? He adds, ?Our offerings like double-barrel technology, high-frequency screens, etc., help in conserving the environment and also provide significant advantage on total cost of ownership.?
Long-term perspective
?TIL believes in making customers more profitable - we have endeavoured to always offer the latest and cutting edge technology to customers, which would add value to their fleet of equipment and offer long-term solutions,? says Prasad.
Patel comments, ?In India, we do not have an agency that undertakes a scientific study of the installed capacities versus capacity utilisation. Large developers have a large equipment bank and if the capacities are idle, they are likely to redeploy the plants for their new projects. And then there is the equipment rental business, albeit nascent in India, which is an option. Having said that, a conservative estimate would put the year-on-year growth till 2020 at 7-8 per cent per annum and an optimistic estimate would be 12-14 per cent per annum.?
He adds, ?The initiatives of the government have infused a high level of optimism and buoyancy into the market. The future for the asphalt plant business looks very bright.?
Profitable, Transportable Technology
- The double-barrel technology is a result of intensive research done by ASTEC Inc on road construction techniques, customer demand, the need for a sustainable road construction methodology, and most importantly, conserving the environment.
- The ability to use up to 50 per cent RAP without any modification to the plant, the fuel efficiency the plant offers, and the ability of the plant to produce consistent asphalt mix are the key differentiators of the double-barrel technology over other technology offerings.
- Other benefits the six-pack double-barrel portable plant offers to the customer:
- Truly portable plants which can be erected and commissioned within 36 to 48 hours. All that would be required is only levelled compacted ground, thus reducing recurring cost of civil foundation;
- Protection of the environment from pollutants and other toxic ingredients which are present in dumped milled bituminous pavements;
- Again, environmental protection by preventing deforestation and conservation of natural resources by using RAP;
- Offsetting the increasing cost of fuel, bitumen and aggregate and reduction of the overall project cost;
- Reduction of carbon footprint of road constructions;
- Making of sustainable asphalt pavements.
- In short, the double-barrel innovation will help meet India?s growing demand for infrastructure requirements effectively - that is why it?s a preferred solution for road construction companies globally.