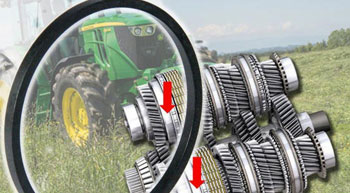
Reliable Sealing Solution
John Deere makes use of the friction and wear behaviour of sealing rings made of DuPont? Vespel? in its pioneering dual-clutch DirectDrive Transmission (DDT) with eight powershift speeds. These rings provide a low-leakage seal against oil pressure of up to 20 bar at oil temperatures of between -30?C and 80?C with transient peaks of up to 110?C over the entire service life of the transmission. John Deere, one of the world?s largest agricultural machinery manufacturers, is offering this particularly efficient and energy-saving DDT system, which permits direct gear shifts without any interruption in traction, in its 6R series of six cylinder tractors.
In John Deere?s DirectDrive transmissions, the Vespel? rectangular sealing rings are located at the wet clutch pressure oil transfer points on the shafts of the two sub-transmissions. As a specialist from John Deere?s Power Train Engineering explains, ?When the clutches are hydraulically actuated, the rings provide a reliable seal for these pressure oil transfer points. As this happens, the conditions change at the sealing points. When the clutch is disengaged, the rings are exposed to low relative speeds between the shaft of hardened and ground 20MnCr5 and the clutch housing with no pressure. When the clutch is engaged, the relative speed is zero, while the differential pressure is at its highest. In both cases, the material?s very low friction and very low wear help to ensure low-maintenance operation of the transmission. Moreover, DuPont?s recommended ring design minimises leakage.?
DuPont and John Deere have closely worked together in order to select the grade of material and tailor the the dimensions of the groove and the rectangular cross-section of the rings. The DuPont development team selected a Vespel? grade with a low coefficient of thermal expansion to provide a consistently high sealing action over the entire temperature range. With its very high creep resistance and excellent friction and wear behaviour, it contributes to the particularly low-maintenance operation of the transmission. Peter Bergmann, European Transportation Market Segment Leader, DuPont? Vespel? & Kalrez?, adds, ?This successful collaboration with John Deere is another demonstration of how companies can benefit from DuPont being a one-stop-shop able not only to manufacture the basic material Vespel? but also to mass-produce high-quality parts. As a result, we are particularly flexible in responding to specific customer requirements and in recommending the most suitable material from our range of grades which are specifically tailored for dynamic applications. Once the material has been selected, we can relatively quickly provide samples for customer testing and for component investigations in our lubricated wear and friction Center Of Excellence, so helping to ensure short development times.?