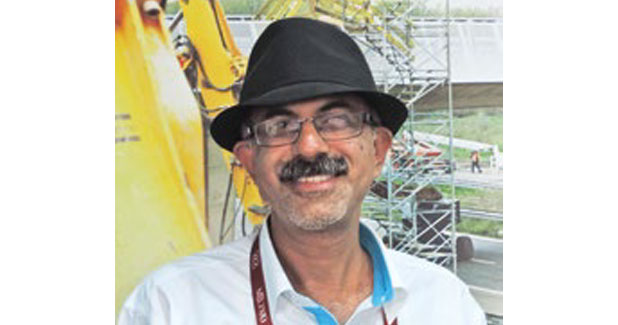
Rock breaker market can grow between 7,000 to 8,000 units in 5 years.
Present in India since 1960 with eleven regional and satellite offices, Atlas Copco offers a wide range of rock breakers. Nitin Lall, General Manager, Atlas Copco Construction Technique, elaborates on its rock breaker range and the market in India.
What are the major application areas of rock breakers?
Rock breakers are mainly used for diverse applications such as secondary breaking, boulder breaking in quarries, primary breaking, foundation, trenching/pipeline, tunnelling/scaling and road cutting.
Specifically, secondary breaking is carried out in aggregate quarries, foundation/breaking is in building projects in cities and primary breaking is in mines. Besides this, applications such as building demolition and tunnelling are some other applications in India. New global applications such as piling and underwater breaking may find some scope in India in the future.
What is the current market trend for rock breakers? Which are the major demand drivers?
Though we have a challenge in India estimating the real market for hydraulic breakers, we can fairly say that it was approximately around 4,600 units in 2012, 3,800 units in 2013 and then close to around 4,000 units in 2014 and 2015. The major drivers for this growth will be the road and infrastructure projects in the pipeline and the positive outlook of the mining industry that will lead to the increased demand in aggregates. Hence, we expect the market to grow to 4,600 units in 2016.
What are the emerging technology trends in rock breakers to reduce maintenance costs and noise pollution?
From a hydraulic breaker, other than optimal output, customers expect higher availability, lower maintenance cost and reduced noise levels. To meet this demand, hydraulic breakers today are loaded with features optimum for maximising productivity as well as long life of the carrier and minimum machine downtime such as:
- High power to weight ratio - Rock breakers should be able to deliver a higher blow energy with the lowest possible dead weight and Atlas Copco hydraulic breakers are world leaders with this concept.
- Minimum components - will ensure low maintenance and auto lubrication ensures the productive time is efficiently utilised.
- Efficiency - will be achieved with less hydraulic power of the excavator, converting it to the maximum hydraulic output keeping the excavator safe while ensuring maximum output.
- Features such as Vibrosilenced available in Atlas Copco hydraulic breakers will ensure that the equipment is able to work in the night with minimal noise even in big cities.
- The rock breaker should invest the required energy on the rock to ensure maximum output and least input cost.
As leaders in hydraulic breaker technology, our breakers are one of the most powerful in the world as compared to other breakers in its class and are designed to perform and provide the lowest cost per tonne. This leads to lower operating and maintenance cost.
What are the parameters of selecting a rock breaker for a project?
Customers evaluate various factors before selecting the suitable brand/type of rock breakers for their project. Type of application for which the breaker is being used for such as boulder breaking, under water, tunnelling or primary breaking is actively considered. Additionally, factors such as the expected productivity where the rock breaker should be able to excavate the required tonnage so as to meet or exceed the productivity requirements of the project and finally what is the working space/site available for the rock breakers to operate within are also considered. Selection of different modes while operating the breaker according to the operating conditions, leads to reduced fuel consumption of the excavator.
What is your take on rock breakers with less hydraulic input power and maximum impact performance? How do you rate your product performance in this aspect?
A hydraulic breaker is like an engine that needs to be of least possible weight, less input to drive the breaker with maximum delivered power. This not only makes the breaker the most efficient but also increases the life of the hydraulic pump of the excavator and in the long run contributes to the increased working life of both the excavator and the breaker.
The high efficiency breakers also consume less fuel, decreasing the input cost and also plays major role in sustaining our green environment.
Impact Power is defined as Impact energy by the Breaker times the blows per minute. Atlas Copco has the highest impact energy for each breaker in every category, coupled with energy recovery mode. So when it comes down to productivity, we deliver maximum power irrespective of any application as compared to other breakers in the market.
Could you brief us on your product range and their major features?
You name the application and we have the breaker! Our hydraulic breakers range from as small as 52 kg in weight that can be mounted on 700 kg class excavator to breakers weighing 10,000 kg that can be mounted on 140 tonne class excavators. Our existing range now caters to every segment in the market. We cover the entire spectrum of the market, that is, for customers needing productivity as their main focus and also for the hiring segment which is our range from the value segment. In India, breakers suitable for 20 tonne excavator class dominate the market. The Atlas Copco MB 1500 medium hydraulic breaker and the EC 136 breaker are the products which are pitched to this specific segment where the MB 1500 is the most popular breaker in our portfolio.
What is your outlook on the Indian market for rock breakers? What are your future plans?
The Indian market offers a huge potential for Atlas Copco rock breakers. Though the market has been stagnant for the last three years, we now expect a realisation of "achhe din'' and good market potential in the next few years to come.
We expect growth in the first quarter of 2016 because of new projects which are getting announced now. Atlas Copco will continue to work towards the launch of improved and different models of breakers to increase our reach to various segments of customers.
If all goes right and the business environment supports the market, then we expect the market size to grow between 7,000 to 8,000 units of breakers in the next five years.
Could you elaborate on Atlas Cocpo's core competencies?
Atlas Copco is present in India since 1960 with eleven regional and satellite offices with highly efficient service support for our world class products to serve our esteemed customers 24x7. Hence, we not only offer a comprehensive product range but we also delight the customer by offering state-of-the art service back up. Our customers are satisfied with Atlas Copco hydraulic breaker quality and product performance. We have many repeat customers in India and the positive word of mouth has resulted in new enquiries and new business.
With a 50+ strong dealer network and growing each year, a healthy stock of equipment and spare parts is maintained across India. Our dealers have a pan India presence from Srinagar in the North to Kochi in the South. Likewise, we have our dealer foot print in Gujarat in West right up to Arunachal Pradesh in the East. With product quality and performance backed by service which is direct and through a well-established dealer network, we are able to meet the market expectation of ensuring productivity with minimum downtime.