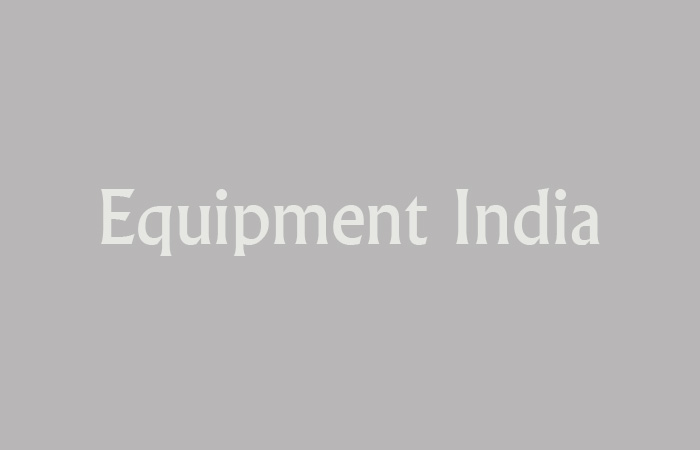
S-valve technology
For the tough daily operation at the construction site, concrete pumps have to be powerful, unflagging, robust, undemanding and reliable. This especially applies to smaller construction sites where they have to render versatile service as inexpensive concrete pumps. In the case of large projects with high-rise and long distance conveying, these machines have to offer real power. It has to be done with minimal mass forces, in a very quiet operation and with a quick switch-over.
The latest concrete pump technology is based on the S-valve technology. In India, it is found that the majority of the market still uses gate valve pumps, which have been outdated and phased out in Europe in the 70s because of high wear and tear. The gate valve technology which still represents the majority of the pump population in India, has too high a liability in wear and tear. That is the reason why customers who have tested the S-valve technology are very pleased with the long service life of the main wear parts and by the low diesel and hydraulic oil consumption.
Beside the lower operation cost, the pump operation is also more comfortable. Due to the close circuit of an S-valve pump, the pump and pipeline can be cleaned by simply pumping water instead of concrete. With S-valve concrete pumps, reverse pumping is also possible, which solves the choking problem in many cases without disassembling and cleaning of the pipeline.
The S-valve technology has been proven to be most economical way to switch from one delivery cylinder to the other. The advantage of one sided wear and tear and the ability to adjust the gap between the spectacle plate and the wear ring makes the S-valve technology the most economical solution.
Concrete pumps with 'S-transfer tube' have been setting new world records in vertical and horizontal delivery. Wherever extremely stiff and abrasive mixes of concrete are encountered, this S-valve system is really useful. It is not surprising that due to this advanced technology in truck-mounted concrete pumps they are affectionately known as `S-tube elephants'.
The Putzmeister concrete pump achieved landmarks in long-distance concrete conveying at the French Le Refrain with 2015 m, and a record pumping height of 606 m at the Burj Khalifa Tower in UAE, 2008. Even in both these cases, the pumps and accessories were still not operating at their limits. Even with difficult concrete, they can be counted on to perform reliably on continuous duty.
The S-valve is the first choice for jobsites with concrete pressures above 85 bars. This is especially useful for long pumping distances over stationary pipelines. The Putzmeister S-valve is especially designed for long life and high concrete pressure. This results in long service intervals and increased availability of the machine. To extend the life of the S-valve, the inside wall can be rebuilt by hard- face welding.
The S-tube that is manufactured out of thick-walled special cast steel is designed for difficult, abrasive concrete. The S-transfer tube masters the most difficult pumpable concrete such as viscous hydro concrete, mixes made up of crushed quartz, granite or basalt with a consistency up to K1 (1? slump) and a grain size of up to 63 mm.
The spectacle wear plate is fitted in the hopper, to the openings that lead to the delivery cylinders. The wear ring is fixed to the inlet opening on the S-transfer tube and the thrust ring lies between the wear ring and S-transfer tube entry. Because of the very abrasive mixes, this three- piece system is subjected to many different types of wear and load stress while the pump is in operation:
? Sliding abrasion on both contact surfaces of the wear parts.
? Blast jet wear on the outer edges of the wear ring and inner edges of openings on the spectacle plate.
? Impact stress at the parting plane, between spectacle plate and wear ring.
? Flow abrasion on openings of the spectacle plate and wear ring.
The low lying agitator that is driven on both sides keeps the mix homogeneous and guides the concrete directly in front of the cylinder openings without sucking the air, thus increasing its efficiency.
The optimised hopper shape reduces concrete settlement and residual concrete. The hopper is easy to clean. The residual concrete is simply emptied via a cleaning valve. The line is cleaned by conveying a sponge ball in a reverse pumping mode.
As and when there is wear and tear of the S-tube due to friction against the spectacle plate, the automatic ring optimally seals the system. This prevents the bleeding out of concrete lines through the fine gaps caused due to abrasive nature of the concrete and thus reduces the danger of blockages. This automatic ring compensates for the wear and seals automatically. This results in an even wearing of parts and therefore prolongs service life. The large stroke volumes reduces the number of strokes and hence the wear and tear. The wear extensive areas are especially protected by chroming, face welding or hardened inserts.
The S-valve has very few wear parts and all parts of the S-tube are easy to change. The hopper remains mounted when the few wear parts require replacement. Hydraulic and switchover cylinders are outside the concreting area and remain clean. The delivery pistons are centrally lubricated for a safer and longer service life. The hard-chrome layer of the delivery cylinders assures a still longer service life of the pistons and the cylinders and protects against corrosion. The non-contacting end-position impulse switch of the pump cylinder is wear- proof. Truck-mixers have optimum access due to the minimum projection of the reduction elbow. The concrete hopper extension can be folded open for easy servicing. All these advantages make the S-valve technology really beneficial for the entire concrete pumping operation.