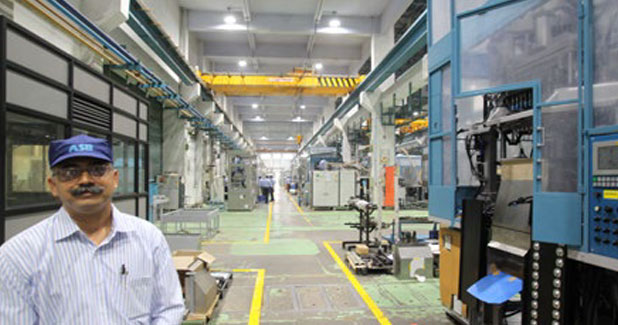
Safe lifting solutions
<span style="font-weight: bold;">Customer-focused major ASB export plant in India equips for the future with Konecranes' latest safety-oriented and cost-efficient lifting technologies.</span><p></p><p> A global leader in the manufacture of high-technology PET container production machinery, ASB International Pvt Ltd, is equipping its major export-oriented plant near Mumbai with some of Konecranes' most advanced lifting technologies to enhance its quality, safety and cost-efficiency.</p><p>The showplace export plant at Ambernath, Thane, was established by ASB parent company Nissei ASB Machine Co Ltd, Japan, and is one of the most modern and largest manufacturing facilities among PET processing machine manufacturers in the world. A key focus of the plant is ensuring high quality and efficient process to cost-efficiently and reliably produce solutions for its customers in more than 80 countries and regions of the world, where 5,000 ASB moulds - the most important item in bottle moulding - are in use.</p><p>More than 50 Konecranes, in capacities from 0.5 to 30 tonne, have been progressively installed to facilitate efficient and safe lifting of machine components, entire machines and complete moulds used to make BoPET (Biaxially-oriented polyethylene terephthalate) stretched polyester film products used globally by industries such as food and beverage manufacturing, liquor, chemicals and cosmetics, building products and household products.</p><p>A total of more than 750 stretch blow moulding machines and 1,200 moulds are produced a year using Konecranes' CXT single and double electric overhead travelling cranes, which are equipped with safety and efficiency features such as automatic overload protections, automatically resettable limit switches and the latest ControlPro safety and performance control system.</p><p>The newest pair of 15 and 25 tonne double girder Konecranes to be delivered to ASB also incorporate Konecranes' latest TRUCONNECT system, incorporating remote digital monitoring and analytical technologies which can look inside the performance of cranes to accurately predict the most suitable and timely maintenance for optimum service, as well as spot impending production risks and accident hazards.</p><p> TRUCONNECT is a suite of remote service products and applications to support maintenance operations and drive improvements in safety and productivity. It is an important building block in delivering Lifecycle Care in Real Time.'By operating in this way, they can enable maintenance and prediction efficiencies that were unimaginable just a short time ago,' says Konecranes. The TRUCONNECT system is now in operation at ASB.</p><p>ASB's fleet of Konecranes also includes flexibly configured travelling wall cranes and XM workstations, which can be customised to precisely fit the different lifting needs of diverse applications, and offering the flexibility to be changed to suit the evolving needs of the user. The Konecranes WLS family of Workstation Lifting Systems ranges from hand-held lifting tools to robust hoists up to 2-tonne capacity. </p><p>'Our Konecranes are an integral component of our relentless focus on quality and process at ASB, by which we have been able to set international benchmarks in our field,' says <span style="font-weight: bold;">Jagdish Shukla, ASB's General Manager, Moulding and Project.</span></p><p>Smaller capacity Konecranes handle machinery components, while larger capacity machines are involved in the assembly and despatch. In addition to standard models, ASB also uses the cranes in the engineering of machines custom-tailored for individual customers' bottle production systems.</p><p>'Cranes are vital to our assembly and dispatch. We rely on them for efficiency and safety. Our Konecranes are easy to use. We have completed operator training with Konecranes, which further contributes to our safety and cost-efficiency. Our cranes are backed with service, with the location of the new Konecranes production facility near us being even better for our needs.' </p><p>'We have enjoyed a very long association with Konecranes, extending from when the plant was established in 1999, and which has become even closer following the opening of Konecranes new production plant near Mumbai. We particularly value their reliability of product, good service and globally advanced technologies that contribute to our safety and cost-efficiency.'</p><p><span style="font-weight: bold;">Chetan Shape, Konecranes District Manager </span>says that, to optimise uptime and minimise potential safety hazards and downtime cause by safety issues, ASB cranes are equipped with:</p><p><span style="font-weight: bold;">Overload protection:</span> Each hoist is equipped with overload protector, which will prevent the lifting of loads beyond the capacity of each hoist on the crane. The overload protector is self-re-setting and the hoist motion is stopped if overloading occurs, but lowering is permitted, making the crane safe.</p><p><span style="font-weight: bold;">Limit switches:</span> Adjustable, four-step, geared, self-re-setting hoist and lower limit switches are provided as standard solution to prevent over-travel of hooks. The up-direction limit switch has three steps. The first step switches the speed from fast to slow and the second step from slow to stop. The third step cuts the hoisting movement in case of phase mismatch.</p><p><span style="font-weight: bold;">ControlPro safety and performance control unit:</span> ControlPro is the new generation of Konecranes' system for hoist and crane safety and performance control. Industry leading electronics and software design of ControlPro device make the load handling safer and easier, says Shape. The model range of ControlPro Perform, Life Time, Optic, Multicare and Interface offer versatile solutions for a wide variety of applications; from light duty monorail hoists to heavy duty process cranes with several hoists and from regular to preventive maintenance programmes. </p><p>'ControlPro solutions offer benefits for crane operators, production managers and maintenance personnel in the form of worker safety and increased productivity and optimal maintenance planning. For crane and hoists owner system means an increased return on investment,' says Shape.</p><p>According to Shukla, the Konecranes technologies incorporated into ASB's equipment reflect the close relationship and understanding of needs developed between Konecranes and ASB. 'Konecranes understands our business and our product very well. They know our production requirements. This saves time and heightens cost-efficiency and ensures services are correct for particular applications,' he adds.</p><p>'When older cranes need parts, we can rely on Konecranes to have spare parts available to keep us at optimum efficiency. They also can help us to introduce new technologies as required, to optimise uptime and safety. We were happy to renew our annual service contract with Konecranes without any issues, given the standard of service and the quality of the relationship,' Shukla concludes.</p>