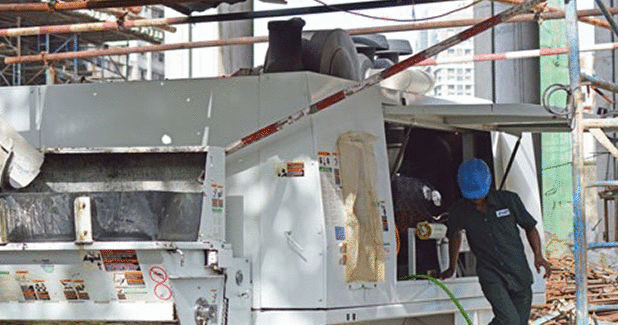
Safety in Concrete Pumps
Safety is one of the major concerns of every person involved in the concrete pumping industry. Although much of the responsibility for everyday safety rests upon the pump operator, it is vital that everyone involved makes safety the top priority. This includes the owners, the mechanics, the ready-mix drivers, the placing crew, the concrete contractors and the machine manufacturers. If spectators will be near the pour, cordon off an area where they will be safe. Never operate the machine if it is not safe to do so, even if the spectators just want to see a certain operation or function.
Setting up a stationary pump
The job set-up phase sets the stage for most accidents. Taking a few extra moments to correctly set up the job will improve the chances of having a safe, trouble-free day/night. Before laying the pipeline or pumping the concrete, the machine stability is very important:
- Place the concrete pump on a hard and levelled surface.
- The front and rear jacks can be operated manually when the locking pins are released.
- With the help of the screw jack, lift the front portion and release the locking pins of the two front jacks and lock it again with pins after setting up.
- Now release the screw jack and loosen it. Set up the two rear jacks and lock it again with pins.
- Make sure the tyre is above the ground level not more than a few inches.
- Pump should always rest on its stabilisers during pumping.
- The operator should not stand on the pipe line.
- The operator should always be near the machine in view of the pipeline.
- Never stand on the grill of the hopper.
- Never remove the hopper grill during pump operation.
- Never insert your hand into the water box during pump operation.
- Never lift the flat gate valve by inserting your hand inside the housing.
- Never try to adjust the hydraulic settings during pump operation.
- The hydraulic hoses should be pressure released while removing the hoses.
Pipelines, end hoses, couplings, and all other material delivery components must be able to withstand the maximum concrete pressure of the pump. Knowledge of minimum wall thickness, operating and concrete pressure is mandatory. Concrete pipeline system is subject to wear, and the rate of wear is affected by pumping pressure, concrete composition, pipeline material and other factors. Bursting pipes and concrete escaping under pressure is a serious safety hazard. Delivery system components must be able to withstand maximum pump pressure. The maximum concrete pressure of the pump must be the only factor used to determine what thickness of pipe and what type of ends are needed. In the case of a valve jam or any other type of blockage, the maximum pressure of the pump will be exerted.
- Never try to adjust or remove the clamp with concrete inside the pipeline.
- Ensure the fitment of the ball catcher during ball passing.
- Ensure the proper support for the pipeline at uniform distance.
The operator is responsible for checking the pipeline for dents, cracks, wear, and continuity each day before the pour begins. In vertical runs, the weight of the vertical sections of pipe must be supported by a thrust block (often called Deadman) or other load-bearing device. Each section of pipeline in a vertical run must be secured from lateral and horizontal movement. Never try to operate the pump by an unskilled operator.
It is recommended to make the ?Operation and Safety Manual? available to all the personnel involved in the pumping job. Safety during pumping, safety during cleaning and safety during clearing the blockages, can only be achieved by proper planning and implementation of periodic quality checks.
The author is Managing Director, Schwing Stetter Sales and Services Pvt Ltd. He is also Chairman of Mechanisation Committee, Builders Association of India.