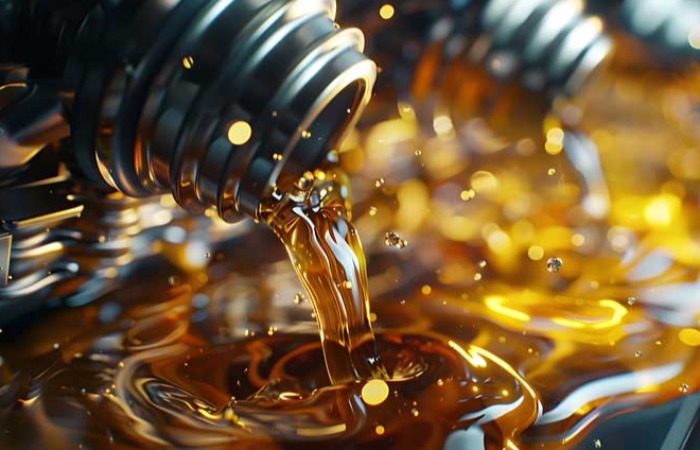
Smooth Operations
In the high-stakes world of construction, where colossal machines operate under intense conditions, the silent hero that ensures their seamless performance is often overlooked: lubricants. From reducing friction and wear to enhancing fuel efficiency and equipment lifespan, lubricants form the backbone of the construction equipment ecosystem.
The construction industry in India is undergoing a transformative surge, with exponential growth in infrastructure projects ranging from highways and metro rail networks to real estate developments and mining operations. In such an environment, the role of industrial lubricants has never been more crucial.
Construction equipment such as excavators, bulldozers, loaders, and mixers work in environments laden with dirt, dust, moisture, and extreme temperatures. These factors contribute to rapid wear and tear. Lubricants not only reduce friction but also offer critical protection against corrosion, thermal degradation, and contamination.
“The Indian lubricant market is demonstrating steady growth driven by escalating demand for industrial equipment. The recent years have witnessed a surge in construction, manufacturing, and mining activities, all of which intensify the requirement for high-performance industrial lubricants,” said Praveen Nagpal, Chief Technology Officer – Lubricants & Services, Shell Lubricants India. “These lubricants are essential to ensure the efficient and productive functioning of heavy machinery operating in these sectors, often under arduous conditions such as mining.”
Shell has co-developed the Komatsu Genuine Oil 15W-40 with Komatsu, meeting stringent OEM standards and enhancing high-temperature performance. Shell’s product range also includes the Shell Tellus S4 VE hydraulic oil and Shell Gadus S3 V460D 2 high-temperature grease, both derived from cutting-edge gas-to-liquid technology.
Demand drivers
India’s lubricant market stands at an estimated 130 million litres annually, with more than 54 percent coming from the industrial sector. According to Ravi Chawla, Managing Director, Gulf Oil India, “The Indian finished lubricants market is the third-largest and one of the fastest-growing lubricants markets in the world. With the growing trade of vehicles and their spare parts, it is anticipated to grow at a CAGR of 4.77 percent by 2027.”
Gulf Oil recently partnered with Schwing Stetter to supply premium lubricants like hydraulic oil, axle oil, and synthetic gear oil tailored for concrete pumps and batching plants. “We offer customised products and services at more than 5,000 sites and to more than 1,000 customers who are building roads, highways, metros, and houses,” added Chawla.
Satya Ranjan Mohapatra, Deputy General Manager, Tide Water Oil, said, “The industrial lubricant market is growing at a modest rate of 3.5 to 4 percent per annum. In the industrial segment, the construction and mining industry contributes around 12 percent to the total lubricants market.”
Customisation and sustainability
Jayanta Ray, GM – Industrial and OEM at GS Caltex India, emphasised their eco-conscious efforts: “GS Caltex is promoting sustainability by offering lubricants with extended drain periods and using recycled plastics in packaging. Our base oils are low in volatility and support high thermal and oxidation stability.”
Their product line, Kixx Lubo, offers environment-friendly Group II/III base oils developed through advanced hydrocracking technology. The company has also introduced Kixx HDX Euro (API CK4) and FA4-compliant lubricants for BSVI engines, reflecting compliance with new emission norms.
“To cater to stricter norms, we have expanded our synthetic grease and hydraulic oil portfolio for construction and mining. These innovations are designed to meet extreme conditions and are backed by proven testimonials,” added Ray.
Emissions, additives, and the future
Vinni Chemicals, a key player in fluid dynamics, has recently developed non-conductive greases for the EV segment and additives that reduce engine corrosion caused by ethanol and methanol blends. “These additives can extend engine life by up to 1.5 years and improve fuel economy by 5–7 per cent,” Harsh Vardhan Jain, Chief Executive Officer, Vinni Chemicals, shared. Their collaboration with JCB and Tata Motors further underscores their credibility.
Vaibhav Maloo, Managing Director, ENSO Group, added, “Our lubricants enhance uptime through high viscosity index, anti-wear additives, and thermal stability. Customers prioritise anti-wear properties, thermal stability, and multi-purpose use along with sustainability and regulatory compliance.” ENSO is developing smart packaging and AI-driven monitoring tools, while focusing on compliance with global standards such as API and ACEA.
In one case, a prominent m-sand manufacturer switched to Mobilgrease XHP™ 462 Moly and saw grease consumption drop by 67 percent, translating to savings of Rs 9,80,000. This wasn’t just due to the lubricant but also an improved lubrication strategy, including better monitoring and predictive maintenance.
Mobilgrease XHP™ 460 series, designed for temperatures up to 140ºC, is ideal for the mining sector where equipment faces severe pressure and environmental conditions.
Says Vasanth Thangavelu, General Manager – Marketing Deployment (Commercial), ExxonMobil Lubricants, “In our product line-up, we have a range of high-performance lubricants designed specifically for the construction and mining sector. These products are tailored to withstand severe conditions such as high temperatures, heavy loads, and harsh environments. One notable product is our Mobil DTE 10 Excel™ Series, hydraulic oil with high viscosity that extends oil change intervals and improves energy efficiency. Another is the Mobil Delvac 1TM ESP 5W-40, a synthetic lubricant offering fuel efficiency and extended engine life. We also have the XHP series, like the Mobilgrease XHP™ 220 Series, focusing on structural stability in harsh operating environments.”
OEM-approved lubricants are specifically designed to meet the unique requirements of the machinery they service. For instance, Caterpillar’s lubricants are formulated to match the exact specifications of their engines and components, ensuring that each part operates under ideal conditions. Similarly, Komatsu and Volvo CE develop their own lubricants to cater to the operational needs and environmental conditions of their machinery. This tailored approach helps maximise performance and efficiency, reducing the risk of breakdowns and costly repairs. One of the key benefits of using OEM-approved lubricants is the extended lifespan they can provide to machinery. These lubricants are engineered to offer superior protection against wear, corrosion, and high temperatures, which helps in maintaining the integrity of critical engine and transmission components.
Caterpillar Oils are designed to provide you with increased performance and extended engine life. They are specially formulated to reduce wear on bearings, piston rings, bushings, and other valvetrain components, which can help your engine run longer. Cat Oils improve engine life, performance, and efficiency. The detergents in the formulation are effective at reducing buildup in your engine.
Case IH stays ahead of the curve with newly improved Hy-Tran® Premium Hydraulic Transmission Oil designed to keep tractor transmissions, axles and hydraulic systems free of deposits while inhibiting wear, corrosion, sludge and foaming. Similarly, CNH top-grade Premium Transaxle Oil enables smooth, noise-free operation in equipment, especially those fitted with oil-immersed (wet) brakes like wheel loaders and tractor loader backhoes.
Tata Hitachi offers a wide range of lubricants includes hydraulic oils, engine oils, gear oils, grease and coolants. The company’s engine oils include high quality base oil and advanced additives combined in a balanced manner for high output and low emission diesel engine. Its heavy duty grease is multi-functional extreme pressure grease suitable for temperatures up to 130°C. It is specially recommended for use in construction equipment and heavy duty vehicles.
Fluid management
Yogesh Kumar, Director – Technical Service, Minimac Systems, shared, “Our business recovers the oil and restores it to fresh oil quality. Reclaimed oil reduces pollution and offers a cost-effective solution.” Minimac has developed indigenous technologies for contamination management, purification, and oil flushing, tailored for diverse industries from coal mining to cement.
Selecting the right lubricant
Selecting the appropriate lubricant—whether oil or grease—is crucial for maintaining equipment performance and prolonging its life. Each type of lubricant has its own set of advantages and drawbacks, making them better suited for different applications and conditions. Effective lubrication not only minimises friction and prevents wear but also ensures smooth and efficient machinery operation.
Viscosity is a key characteristic of lubricants that impacts their ability to protect heavy machinery. It essentially governs the lubricant’s flow and thickness, akin to its lifeblood. When choosing a lubricant, consider both the type of machinery and the specific operating conditions it encounters. Different machines require different viscosities to function optimally. For instance, high-speed equipment typically performs better with low-viscosity lubricants that reduce friction and improve efficiency, while heavy-duty machinery may need higher viscosity lubricants to support greater loads. Environmental factors, especially in industries like oil and gas, also play a crucial role in determining the right viscosity.
Additionally, compatibility is an essential factor in lubrication. The chosen lubricant must be compatible with your machinery’s existing systems. Incompatible lubricants can cause efficiency issues, increased wear, and costly breakdowns. By opting for our pressure-activated lubricants, you minimise the risk of compatibility problems.
Conclusion
Lubricants play a vital role in the effective operation and longevity of construction equipment. By reducing friction, dissipating heat, preventing corrosion, and providing cleaning and sealing functions, lubricants help ensure that machinery performs optimally and remain reliable in challenging conditions. Understanding the types of lubricants available, adhering to best practices, and addressing common challenges can significantly enhance equipment performance and reduce maintenance costs.
Investing time and resources in proper lubrication practices not only extends the life of your equipment but also contributes to safer and more efficient construction operations. As construction projects continue to grow in complexity and scale, maintaining a proactive approach to lubrication will remain a key factor in achieving success and maximising the value of your investment in machinery.
Despite the best efforts, challenges in lubricating construction equipment can arise. Here are some common issues and how to address them: