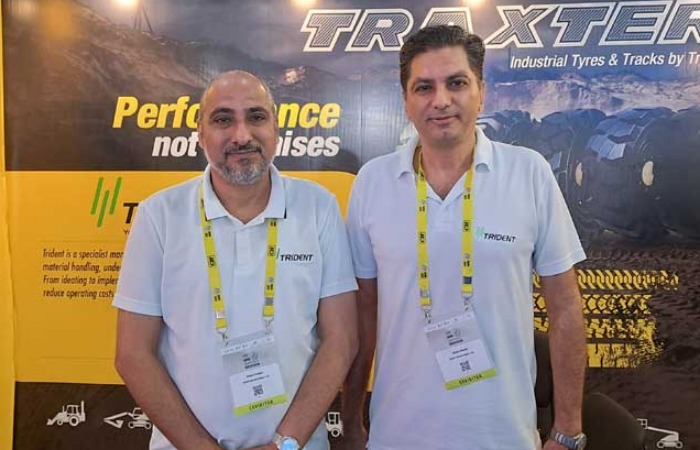
Sooner there will be a trend of electrification in construction equipment
Trident was founded in 1997, and its primary business has always been the production of tyres. In the tyre industry, we specialise in producing industrial tyres for mining equipment, material handling equipment, infrastructure equipment, and construction equipment. Our industry is non-agricultural OTR.
What are the companys offerings for the mining segment?
Our concentration is on underground mining within the mining sector”tyres for LHDs, jumbo drills, etc. As you are aware, underground mining has its own unique quirks and working circumstances that set it apart from surface mining. As a result of the tight quarters and challenging terrain, operating in underground mines presents safety challenges. If a tyre fails in that setting, whether due to damage or premature manufacturing-related problems, it presents many difficulties. We developed solutions for the underground mining industry because of this.
What are the USPs of these products?
Our value proposition is to provide a customer with a product that boosts safety, decreases downtime, and promotes productivity. We concentrate on offering remedies that render tyres impervious to punctures. We provide two technologies: tyre filling technology and full rubber tyres, often known as solid tyres.
Tyres made entirely of rubber cannot puncture. The benefit is that solid tyres last longer due to the deep thread in tyres. In tyre filling, polyurethane is injected within an existing tyre. In tyre filling, you take an existing tyre and inject polyurethane inside. Its replacing the air with polyurethane. You are making a pneumatic car tyre into a solid.
Depending upon the specific application, there are some applications in which solid tyres are better suited. There are some applications in which overdyed are better suited. We try to engage with the customer and understand what their specific issues and challenges are.
The availability of raw materials is one of the key issues faced by most tyre manufacturers. What are the challenges faced by your company?
Yes. The supply chain had problems, but many of those problems have already been remedied. We keep a substantial amount of stock on hand. We do conduct a sizable amount of export business, however there were some delays. There was not a single incident of any supply problems for the clients on the domestic market. Our strategy has always been to overstock so that there is never a supply shortage.
For instance, the raw materials needed for the foam filling process and even the machinery needed to inject the modules are imported. The exact ratio in which the tyres must be filled is specified. We actually got four stations. We started with one, but we made sure to build a certain amount of redundancy in the system. These stations or production units are like a complete setup to fill tyres, and are located in Pune and Jaipur.
We are not awaiting orders from clients. We have enduring connections with our clients. We are aware of the tools they use and the sizes of tyres they need. Foam filling is a lengthy process that takes time to complete.
In Pune, we have a fully functional workshop with numerous robust tyre mounting machines and tire-changing tools. Some of the products are created internally, but as time goes on, the percentage will rise.
How important is R&D for the company?
In underground mining especially, R&D plays a very important role. What is happening is that machines are getting bigger, faster and more expensive. This puts a lot of pressure on the capital structure of any business. Even the engines have moved to Bharat VI. In terms of the actual output, there is almost no improvement, but the cost has gone up by 15 to 20 per cent.
It is more important that you make sure that your machine is as productive as it possibly can be. The last thing you want is that in you spend a huge amount of money on buying equipment and you have downtime because the tyre is not performing or is damaged.
Sooner there will be a trend of electrification in construction equipment. We are seeing that trend in Europe. Even this will have an impact on the tyre. The requirements of rolling resistance, the requirements of higher torque, etc. are going to have an impact on the performance of the tyre.
Do you export? Which are your stronger markets?
About 80 per cent of our sales are already exported. There is a very clear strategy to make supply chains more resilient. Even if they have not faced any major issues in terms of the supplies from China, they are increasingly wanting to develop an alternative. We are seeing a lot of customers inquire and almost actively seeking alternatives to their current supply sources from China.
In terms of performance, how was the year 2022 for the company? What is your plan for 2023?
In 2022, we were almost at the pre-COVID level. The year 2023 is looking like our best year.
We are expanding our facilities in Jejuri, Pune. We are adding substantial capacity over there and well be developing a lot of new products. Some of the products, which are currently not made in India, will also be made. We expect that plant to be operational soon.