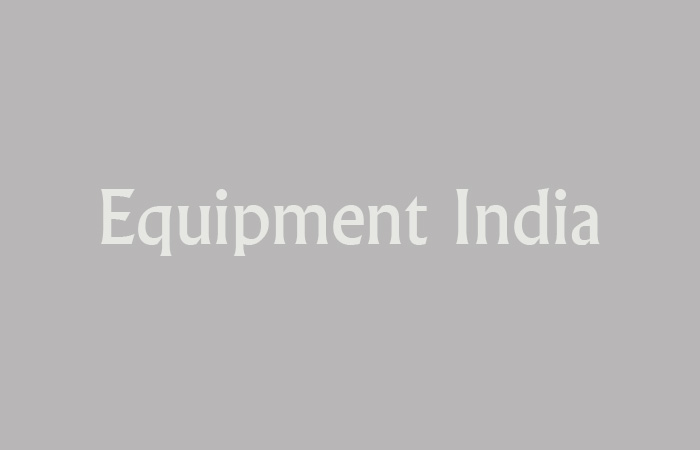
Speco JV with the basic group will have a manufacturing set up in India soon.
Brief us on the core strengths and competencies of the Basic Engineering Group?
The Basic Engineering Group has introduced state of the art hot mix plants (batch type from Speco, Korea). The core strength of the Basic group lies in the service setup created by them to serve customers in India and abroad. It has a team of engineers who look after the equipment sold and provide all kind of technical support.
Tell us about the range of products offered from Speco and services provided by Basic Engineering?
Speco offers hot mix plants - batch type ranging from 80 TPH to 320 TPH. The Basic Group provides all the accessories required for the operations of these plants. The Group also provides after-sales services and maintenance of such plants in India and the Middle East.
How do you rate the success of the Speco range of products and what is the current market share?
Speco sold their first plant in 1999 which is still in production. The biggest market share is with Speco, not only in India, but also in the international market. Speco has been synonymous with the hot mix plant - batch type. Every contractor has a dream to own a Speco plant in their fleet of machinery. There are some contractors who have more than six plants in their fleet and are quite satisfied with their performance. In fact, Speco plants have a long life and experience multiple shifts from one site to another.
What is the impact of the economic slowdown on your business and how do you expect to end this fiscal?
There has been an impact due to the economic slowdown especially in the infrastructure sector. We expect things to be better only by the middle of the next year which is when we expect the economy to stabilise. We hope for a more stable government which will focus on infrastructure projects specially the road projects. We also expect the interest rate to be brought down and anticipate new investments in the road sector.
What is the impact of the plummeting value of the rupee?
There has been a big impact of the falling rupee and contractors have been trying to postpone their decisions to establish the Letter of Credits. We expect the rupee to be around 52 to 53 by next year when the Indian economy stabilises.
What is the present status of the hot-mix technology and how is Basic Engineering meeting the evolving challenges?
Speco is the only company which is constantly upgrading the technology by introducing an air automised burner to reduce the fuel cost. The new design dryer has reduced maintenance. The new vibrating screen design ensures good quality. The mixer design has also improved, the quality of the mix is also very good and the life of the wear parts has increased by at least 30 per cent.
Could you tell us the selection criteria for hot mixing plants?
Should one go for the drum mix type or the batch type?
Most of the customers select the batch mix plants if the technical specifications are such. The quality of mix is not comparable between a batch mix plant and drum mix plant. The batch mix plant provides much better quality of mix. In India, it is advisable to go for the batch mix plant in order to have good quality roads. The cost of making a road involves a big cost for bitumen, fuel, and aggregate. The processing cost due to high investment in the batch mix plant is much smaller in comparison to the input cost incurred for bitumen, fuel, and aggregates. We are in fact surprised as to why authorities still allow the use of the drum mix plants in the country. The raw material cost for making a road is more than Rs 3,000 per tonne and the laying cost is around
Rs 300 per tonne. The processing cost will go up by Rs 50 per tonne if one makes use of the batch mix plant and this cost is insignificant. By just spending a little extra, one can ensure the good use of Rs 3,300 for raw material and the cost of laying. The authorities should not come under pressure and should allow only the batch mix plants in the country.
We are sure once the volume increases, the prices will come down for the batch mix plants. Moreover, the drum mix plant pollutes the complete environment as it does not have a bag house and it also pollutes a lot of water due to the use of wet cyclone.
How environmentally friendly are the Speco range of products that you offer?
The Speco range of plants offers emission norms better than 20 ml/gm per cu nm. In fact, operators of the plant sometimes wonder whether the plant is in operation or shut down as they can't make out the difference due to the bag house provided in the plant.
What are your views on the existing codes and specs with regard to recycling, particularly the use of RAP? To what extent does the Speco range have RAP processing capabilities? Also, what are the challenges that you face in this area and how do you overcome it?
The RAP systems are of two types: Warm RAP and Cold RAP. Speco has vast experience in both the systems. In India, we have supplied Cold RAP systems along with the batch mix plants, but its use is limited to 10 per cent of mixed material. The Cold RAP is mixed in the mixer and there is a limitation of use of 10 per cent to 12 per cent. The quality of the RAP material is also to be tested before it is re-used. In the Warm RAP one could use 40 per cent of RAP material. The material is heated up in the separate dryer and is weighed and added to the mixer for mixing.
How have the operators of these plants been trained?
Since we have a huge number of plants, our customers do not find it difficult in locating trained operators. We have regular training programmes at the customer's place. However, we also hire many trainees and train them at our plants and place them with our customers.
How do you view the future of the HMA industry?
The present scenario is challenging due to the falling rupee. However, we will overcome this once Speco JV with the Basic Group has a manufacturing set up in India, which will be soon. If the authorities are serious about the quality then we expect a good market for the HMA industry.