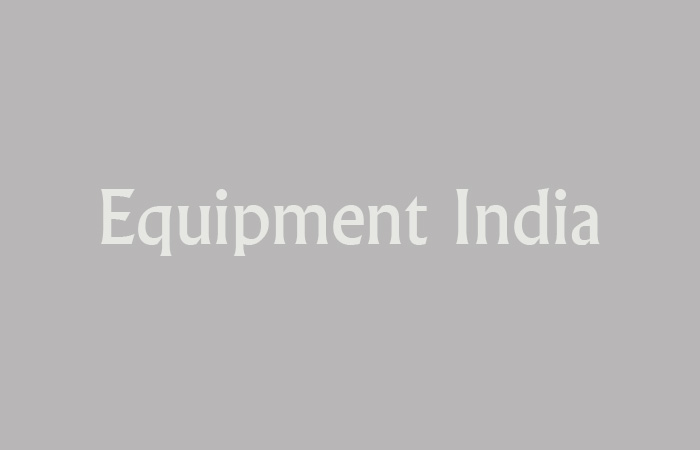
Switching from conventional to microtunnelling
Prof. Niranjan Swarup discusses the impediments faced by urban local bodies, the reasons for selecting the microtunnelling technique, project related issues, learning from the situation, and proposed working methodology.
Of late, many urban local bodies (ULBs) have started using microtunnelling (MT) for installing gravity flow pipelines in urban areas. Some of the projects are planned MT works but others are outcomes of failure situations, where initially a conventional construction method was planned, and due to impediments, the owners were forced to use MT.
These projects are problematic for everyone as the timelines are failed ones, money and efforts are wasted, and at times, there are possibilities of complete project failure. One, therefore, must try to avoid getting trapped in such situations. Recently a ULB engaged in the construction of a trunk sewer line through cut-and-cover construction process, had to stop the entire construction operations and seek guidance from Indian Society for Trenchless Technology (IndSTT), after things went horribly wrong.
As an alternative, they considered applying trenchless technology applications to overcome the impediments and accordingly, contacted IndSTT for directions. Upon inspection, a combination of trenchless techniques was suggested with a majority of portions to be constructed through microtunnelling, as in a majority of places the impediments could be overcome by this technique alone.
This article discusses the impediments faced by the ULB, the reasons for selecting MT, the microtunnelling technique, project related issues, learning from the situation, and proposed working methodology.
The project was for the construction of a sewerage network in a densely populated urban area and under execution for quite some time. Gradually, the hurdles in open cut excavation became immense at certain locations due to several unexpected or unplanned for impediments, both underground as well as over ground. Such impediments included urban settlements and encroachments on the right-of-way, presence of hard rock with a recorded peak, unconfined compressive strength of 300 mpa on the alignment in some stretches, presence of very high levels of groundwater table in some other stretches necessitating substantial dewatering exercise, and several such impediments. In addition to these, the upper levels of subsurface strata in some stretches also had high concentration of underground utilities and telecom appurtenances of sizes varying from 300 to 1,200 mm. A further complication was in the shape of stiff traffic management conditions that required retaining continuous traffic movements at the road junctions within the project area.
These impediments ensured stoppage of excavation works and the project owners were forced to look for safe alternatives. Due to the criticality of these impediments, a solution had to be found which was capable of installing the pipeline at the required depth without disturbing the existing structures and installations in proper grade and alignment. Such capability is typical of the microtunnelling technique and therefore the suggested solution.
Solution
As surface excavation was found to be impossible, the natural outcome was to opt for trenchless technology. The next decision needed was to select the most suitable trenchless technique as there are several trenchless techniques, each with different attributes. Based on the impediment report, in most of the stretches, employment of microtunnelling was proposed as this technique is capable of developing buried pipelines on critical grade and alignments, at required depths, without excavating the complete cross section from ground surface. In addition to avoiding disturbances to above ground settlements and structures, application of this technique could also help in avoiding expensive rock excavation of the upper regions.
Microtunnelling
This is a trenchless construction method employing a remote controlled articulated shield and a pipe jacking system. The shield or the Microtunnelling Boring Machine (MTBM) is used to excavate the soil and the pipe jacking system is used to push the segments of the pipe and machine forward simultaneously. The excavated material is transported by either mechanical means or by a slurry system. The technique heavily depends on a laser guidance system that keeps the progress on track.
It is operated through an access shaft in which the jacking system is placed. Once the MTBM is lowered, placed and operated on the jacking system, the MTBM shield starts cutting the soil and the spoil is transported either mechanically or in the shape of slurry mixture. Upon extraction from the entry shaft the slurry is recycled to remove the spoil in the separation unit. Once the MTBM is jacked into the soil, the jacks are retrieved and the new segment of the pipe is lowered into the access shaft to be jacked behind the shield. The new segment is connected to the previous one and the process continues until the MTBM reaches the receiving shaft. Once the excavation and installation of the pipe is complete, the MTBM is taken out of the receiving shaft.
The microtunnelling method offers highly accurate installations of pipeline at any depth and under various difficult ground conditions. The disadvantage of microtunnelling is the high initial cost of the microtunnel boring machines. Microtunnelling is not appropriate for low strength pipes due to the jacking procedures involved. Obstructions in the soil profile may cause problems during the cutting procedure.
Project
In the project, besides the technical issues, commercial matters also had to be handled by the ULB as the contract was already awarded and the onus of removing the impediments was under debate then. As those matters are beyond the scope of this article, we are discussing the issues and related learning from the project hereafter.
Issues
1. Project was planned as an open cut work and therefore the budgets were also in alignment.
2. Eviction of encroachments over government lands and acquisition of private properties was one major bottleneck.
3. Geotechnical reports failed to identify the presence of hard rock
4. Reports also failed to detect buried utilities.
5. Substantial time was lost before the project was stopped, leading to escalation of costs and project delays.
6. Normal pipes in line with open cut working methodology were fabricated for the entire project length. So, any change in pipe details was bound to make those pipes unusable.
Learning
1. Switching from conventional methods to trenchless methods entails major changes in project scope.
2. Costs of changeover are extremely high and may have a bearing on the success of the project.
3. Ground reality is that the prices of similar projects executed under conventional and trenchless method would be substantially different, with trenchless being more expensive.
4. These price differences lead the project planning engineers to opt for conven?tional construction methods on
account of contemplated savings.
5. However, one must consider the actual similarity before taking this decision.
To elaborate, let us look at the issues of the highlighted project. The geotechnical report was incomplete, the squatters could not be removed, water table and buried utilities enhanced the difficulties, and traffic approvals were stringent. Had all this been considered, the planners would have chosen to apply trenchless in the first go itself. This would have helped the project owner on many counts and prevented major time and cost over-runs. When planned, the considered project was a simple one, where none of these difficulties were anticipated, naturally conventional trenching and backfilling was adopted. However, that was not to be, what happened had not been considered. The learning therefore, is to go for proper investigation and a thorough risk assessment before taking any decision.
Proposed working methodology
One must consider preparing a feasibility report on the basis of site conditions, available data/information, bore log details, soil and rock test reports, drawings and other site related information and see if an open cut is possible or if there are possible threats. Should the threats be irresolvable, one must select the suitable trenchless technology based on the feasibility report. One must check the ground reality before selecting any methodology, whether conventional or trenchless. Altering the choice midway is no solution. One must seek expert advice, in case of doubt, in advance, rather than leaving the issue unresolved at feasibility stage, and spending more at execution stage.
My advice: do your homework before signing on the dotted lines.
The author is Executive Director, Indian Society for Trenchless Technology. Email: indstt@indstt.com
Of late, many urban local bodies (ULBs) have started using microtunnelling (MT) for installing gravity flow pipelines in urban areas. Some of the projects are planned MT works but others are outcomes of failure situations, where initially a conventional construction method was planned, and due to impediments, the owners were forced to use MT.
These projects are problematic for everyone as the timelines are failed ones, money and efforts are wasted, and at times, there are possibilities of complete project failure. One, therefore, must try to avoid getting trapped in such situations. Recently a ULB engaged in the construction of a trunk sewer line through cut-and-cover construction process, had to stop the entire construction operations and seek guidance from Indian Society for Trenchless Technology (IndSTT), after things went horribly wrong.
As an alternative, they considered applying trenchless technology applications to overcome the impediments and accordingly, contacted IndSTT for directions. Upon inspection, a combination of trenchless techniques was suggested with a majority of portions to be constructed through microtunnelling, as in a majority of places the impediments could be overcome by this technique alone.
This article discusses the impediments faced by the ULB, the reasons for selecting MT, the microtunnelling technique, project related issues, learning from the situation, and proposed working methodology.
The project was for the construction of a sewerage network in a densely populated urban area and under execution for quite some time. Gradually, the hurdles in open cut excavation became immense at certain locations due to several unexpected or unplanned for impediments, both underground as well as over ground. Such impediments included urban settlements and encroachments on the right-of-way, presence of hard rock with a recorded peak, unconfined compressive strength of 300 mpa on the alignment in some stretches, presence of very high levels of groundwater table in some other stretches necessitating substantial dewatering exercise, and several such impediments. In addition to these, the upper levels of subsurface strata in some stretches also had high concentration of underground utilities and telecom appurtenances of sizes varying from 300 to 1,200 mm. A further complication was in the shape of stiff traffic management conditions that required retaining continuous traffic movements at the road junctions within the project area.
These impediments ensured stoppage of excavation works and the project owners were forced to look for safe alternatives. Due to the criticality of these impediments, a solution had to be found which was capable of installing the pipeline at the required depth without disturbing the existing structures and installations in proper grade and alignment. Such capability is typical of the microtunnelling technique and therefore the suggested solution.
Solution
As surface excavation was found to be impossible, the natural outcome was to opt for trenchless technology. The next decision needed was to select the most suitable trenchless technique as there are several trenchless techniques, each with different attributes. Based on the impediment report, in most of the stretches, employment of microtunnelling was proposed as this technique is capable of developing buried pipelines on critical grade and alignments, at required depths, without excavating the complete cross section from ground surface. In addition to avoiding disturbances to above ground settlements and structures, application of this technique could also help in avoiding expensive rock excavation of the upper regions.
Microtunnelling
This is a trenchless construction method employing a remote controlled articulated shield and a pipe jacking system. The shield or the Microtunnelling Boring Machine (MTBM) is used to excavate the soil and the pipe jacking system is used to push the segments of the pipe and machine forward simultaneously. The excavated material is transported by either mechanical means or by a slurry system. The technique heavily depends on a laser guidance system that keeps the progress on track.
It is operated through an access shaft in which the jacking system is placed. Once the MTBM is lowered, placed and operated on the jacking system, the MTBM shield starts cutting the soil and the spoil is transported either mechanically or in the shape of slurry mixture. Upon extraction from the entry shaft the slurry is recycled to remove the spoil in the separation unit. Once the MTBM is jacked into the soil, the jacks are retrieved and the new segment of the pipe is lowered into the access shaft to be jacked behind the shield. The new segment is connected to the previous one and the process continues until the MTBM reaches the receiving shaft. Once the excavation and installation of the pipe is complete, the MTBM is taken out of the receiving shaft.
The microtunnelling method offers highly accurate installations of pipeline at any depth and under various difficult ground conditions. The disadvantage of microtunnelling is the high initial cost of the microtunnel boring machines. Microtunnelling is not appropriate for low strength pipes due to the jacking procedures involved. Obstructions in the soil profile may cause problems during the cutting procedure.
Project
In the project, besides the technical issues, commercial matters also had to be handled by the ULB as the contract was already awarded and the onus of removing the impediments was under debate then. As those matters are beyond the scope of this article, we are discussing the issues and related learning from the project hereafter.
Issues
1. Project was planned as an open cut work and therefore the budgets were also in alignment.
2. Eviction of encroachments over government lands and acquisition of private properties was one major bottleneck.
3. Geotechnical reports failed to identify the presence of hard rock
4. Reports also failed to detect buried utilities.
5. Substantial time was lost before the project was stopped, leading to escalation of costs and project delays.
6. Normal pipes in line with open cut working methodology were fabricated for the entire project length. So, any change in pipe details was bound to make those pipes unusable.
Learning
1. Switching from conventional methods to trenchless methods entails major changes in project scope.
2. Costs of changeover are extremely high and may have a bearing on the success of the project.
3. Ground reality is that the prices of similar projects executed under conventional and trenchless method would be substantially different, with trenchless being more expensive.
4. These price differences lead the project planning engineers to opt for conven?tional construction methods on
account of contemplated savings.
5. However, one must consider the actual similarity before taking this decision.
To elaborate, let us look at the issues of the highlighted project. The geotechnical report was incomplete, the squatters could not be removed, water table and buried utilities enhanced the difficulties, and traffic approvals were stringent. Had all this been considered, the planners would have chosen to apply trenchless in the first go itself. This would have helped the project owner on many counts and prevented major time and cost over-runs. When planned, the considered project was a simple one, where none of these difficulties were anticipated, naturally conventional trenching and backfilling was adopted. However, that was not to be, what happened had not been considered. The learning therefore, is to go for proper investigation and a thorough risk assessment before taking any decision.
Proposed working methodology
One must consider preparing a feasibility report on the basis of site conditions, available data/information, bore log details, soil and rock test reports, drawings and other site related information and see if an open cut is possible or if there are possible threats. Should the threats be irresolvable, one must select the suitable trenchless technology based on the feasibility report. One must check the ground reality before selecting any methodology, whether conventional or trenchless. Altering the choice midway is no solution. One must seek expert advice, in case of doubt, in advance, rather than leaving the issue unresolved at feasibility stage, and spending more at execution stage.
My advice: do your homework before signing on the dotted lines.
The author is Executive Director, Indian Society for Trenchless Technology. Email: indstt@indstt.com