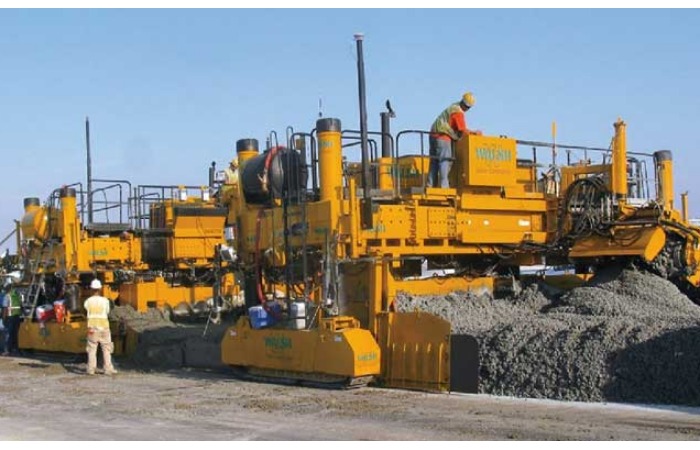
The Concrete Advantage!
On the basis of value, batching plant segment is the largest segment in the Indian concrete equipment market. The growth of the segment is led by growing customer preference for high capacity and technologically advanced batching plants. Moreover, factors such as the increasing number of construction projects, shorter completion time, and the demand for customised solutions by end-users are further fuelling the growth of this segment.
Government initiatives toward infrastructure development are further boosting the demand for concrete equipment in India. Some of the construction projects in the country include Smart City Mission, AMRUT, the Atal Mission for Rejuvenation of Urban Transformation, Metro Rail in urban areas, Bharatmala, and Sagarmala, among others.
In addition, the government is also supporting the Indian concrete equipment market by liberalising taxation policies for the construction industry such as GST and customs duty. In 2018, the government of India reduced the GST on concrete equipment from 28 per cent to 18 per cent, which will help the concrete equipment manufacturers to reduce the overall cost of equipment and other operational losses.
Speaking on the current market, Anand Sundaresan Managing Director, Ammann India, said, “Undoubtedly, India offers a huge opportunity for the growth of the construction equipment industry, due to the government’s focus and trust in infrastructure development. The recent budget has been quite encouraging for the CE industry. The budget is an investment-oriented budget with over 35 per cent increase in Capex outlay for infrastructure development covering road, river linking, railways and affordable housing amongst others. Prime Minister Gati Shakti master plan for the expressway for faster movement of goods and people will spur road construction activity. Further, the announcement of the growth of the highway network by 25,000 km in 2022-23 will help the CE Industry. So overall there are huge opportunities for the CE Industry to grow including our products.”
Ammann India offers Ammann Elba CC60 plant, which is a linear and transport-optimised concrete mixing plant. Fast installation times and ease of relocation – as well as favourable transport dimensions – were the engineering goals of the new plant concept. The result is the new CC plant, which is extremely fast to set up due to its folding mechanisms and compact plant design.
Sundaresan adds, “The compact plant is equipped with a specialised design CEM 1000 S Elba single-shaft mixer in operation globally with an integrated linear bin for storing between 2 and 4 aggregate types. Cement, water, aggregate scales and all other electric and pneumatic plant components are pre-installed and ready for operation. The integrated control cabin houses the switching cabinet and offers additional space for the control system. With a theoretical hourly output of 60 m³/h, the new CC 60 is the ideal plant for a wide range of applications. No foundation is required for plant installation. Optional solutions are available as per project requirements. Customers will appreciate the exceptional service and maintenance accessibility designed into the CC 60.”
All control systems in Ammann plants are equipped with microprocessor control, which is 1,000 times faster than PLC control systems offered by most of our competitors. He adds, “The system helps to enhance fuel economy. AS1 control system provides fully automated mix production, plus the flexibility to work in safe manual mode. The system offers a host of other benefits including the use of unlimited recipes, automatic burner control, dynamic in-flight correction abilities and full integration of bitumen storage tanks. Such advanced technologies in our plants help our customers to achieve high-quality mix, energy and fuel savings and high reliability, thereby improving productivity and TCO. AS1 software is specially designed to improve efficiency and is compactable with all asphalt batch plants.”
Ramesh Palagiri, Managing Director and CEO, Wirtgen India, said, “The market for concrete pavers has been varying in the past few years. Concrete roads are extremely durable. Their tremendous compressive strength prevents the formation of wheel ruts even when used by a high percentage of heavy vehicle traffic. Such concrete pavements, which need to withstand exceptional loads each and every day, are paved and smoothed by the Wirtgen slip form pavers at working widths from 2.5 m to 16 m.”
For concrete paving, the Wirtgen slip form pavers can now offer dual-layer concrete paving, where a single machine is used for dual-layer concrete paving, and the bottom layer and the top layer concrete are paved in a synchronised operation. It is additionally ensured that both the top and bottom layers are paved “wet-in-wet” regardless of weather or site conditions. This can be done with a single paver or with two pavers where it is necessary to distribute the operating weight to two separate machines.
Wirtgen Group is the world market leader in concrete slip form pavers and these are available in working widths of 2.5 m to 16 m. Palagiri adds, “The type of the project and the timeline for execution determines the type of machines to be procured. The width of the road and the density of traffic in terms of millions of axle loads to be paved is one of the prime criteria in selecting a slip-form paver. For an existing State highway that is to be developed from a single lane to two lanes with shoulders, where the existing road cannot be disturbed due to ongoing traffic, the paving has to be done in two passes and you may have to select a paver with a width of around 5 m, whereas for a new greenfield project the paving can be done in a single pass where the no of lanes to be paved would determine the width of the paver required. Another important criterion for selection is whether the dowel bars are to be inserted manually or automatically, though it is always recommended to use an automatic dowel bar inserter to ensure the right quality. The type of the project and the timeline for execution also determine the type of machines to be procured. Relevant technology is always important for completing projects on time, and also ensuring that we have good quality and longer lifetime for the roads.”
The Wirtgen Group has been involved with road development in India since the golden quadrilateral days starting with the Mumbai Pune Expressway. Wirtgen slipform pavers have several innovations like the automatic dowel bar inserter system DBI, super smoother, central tie bar inserter, oscillating beam, etc.
VG Sakthi Kumar, Managing Director of Schwing Stetter (India), said, “The current market size is approximately at 150 batching plants, 150 concrete pumps, 750 concrete truck mixers and 350 to 400 self-loading mixers per month. The year 2021 should see an increase of 20 per cent over 2019. The YoY demand will be at 20 to 25 per cent in today’s scenario. Roads and highways will be the real differentiator. Metros and high-speed rail will give momentum to the business. This can be met by the Government’s keen initiatives on the completion of existing projects and awarding new projects. Easy funding from bankers/NBFI’s will increase the demand.
He adds, “Segments that will drive the demand for concrete equipment are highways and roads, metros in major cities, irrigation projects, infra projects, and real estate (for ready mix concrete). Road/rail connectivity in North and Northeast has and will give good business for concrete equipment. The YoY demand will be at 20 to 25 per cent in today’s scenario. Roads and highways will be the real differentiator. Metros and high-speed rail will give momentum to the business. This can be met by the Government’s keen initiatives on the completion of existing projects and awarding new projects. Easy funding from bankers/NBFI’s will increase the demand.”
The concrete equipment market in India is looking very positive currently, backed by the strong investment plans of the Central and State Governments and private core sector companies. We have observed that the demands across all product range of concrete equipment viz batching plants, transit mixers, concrete pumps, self-loading mixers, etc. are consistently growing over a period of time after the lockdowns. In the past few years, demands for high productivity and high-capacity machines are increasing and customers are open to exploring more technologically-advanced products and we feel the product evolution of equipment will be faster in coming years,” said a spokesperson from Husqvarna India Products.
KYB-Conmat is introducing new and advanced range of self-loading concrete mixers—CSLM 2800, CSLM 4300 and CSLM 4800—which can produce 2.8, 4.3 and 4.8 cbm of concrete in each cycle, respectively. These CSLMs offer high productivity, faster loading and unloading, and have an electronic weigh batching system with a printer. The concrete mixing quality is also superior due to the advanced design of the spiral blades. These machines are very operator friendly due to their single joystick control and reversible operator posts.
“In KYB-Conmat, we are practicing the “Atmanirbhar Bharat” concept from the inception: Our entire range of products are designed, developed, and manufactured in India keeping in mind the ‘heavy-duty cycle’ requirements of our esteemed Indian customers. KYB-Conmat has a state-of-the-art R&D and manufacturing facility in Vadodara, Gujarat, spreading over 5,00,000 sq ft. to produce technologically advanced yet economically viable equipment. We are happy to convey that we have done production and sale of more than 10,000 pieces of equipment from this facility,” adds the spokesperson from Husqvarna.
“The last two years have been challenging for the industry and in the quarter ending September 2021, the construction equipment industry posted a robust sales growth of 47 per cent. So, we can see some green shoots, and the Government's continued focus on different missions has increased the impetus and catapulted various infrastructure development projects across India. The National Infrastructure Pipeline, an Rs 111 crore project by the Government of India which has been actioned upon, augurs well for the Indian construction equipment industry,” said Ajay Aneja, Chief Marketing Officer, AJAX Engineering.
He adds, “The infra projects award tendering activity has started to pick up and the majority of this is an account by road projects. The road construction activity will gather pace from now on with the withdrawal of the monsoon. Road construction has been a major volume driver for the CE industry with the pace of execution pace in FY22, targeted at 40 km per day.”
CRISIL estimates that the investment in Industry could rise by 30 per cent in FY22-24 led by mega projects in High-Speed Rail, corridors, expressways, solar energy, affordable housing, and airports apart from roads and railways. This project’s pipeline and shortage of labour have led to an increase in demand for higher capacity and productivity equipment like batching plants, boom pumps and transit mixers.
Over the years, AJAX has expanded its product portfolio from self-loading concrete mixers to a total concrete equipment supplier. The portfolio includes batching plants, boom pumps, and India’s first locally made concrete slip-form paver. Today, the company has a customer base pan India and across the globe.
AJAX was the pioneer in bringing the concept of SLCM to India way back in 1992 and revolutionised the way of concreting in project sites. Over the years we have added new features like the load cell weighing system for higher accuracy that has been patented. Further, we have introduced smart fleet telematics, rear-view camera, admixture dosing units, bidirectional tyres, AC cabins, EH drum control, high-pressure water jet, smart CBC, etc., to name a few and many of these have been an industry-first keeping in mind its customers evolving needs. In August 2021, the company introduced India’s first all-new CEV Stage IV compliant ARGOs that offer the best-in-class benefits with excellent fuel efficiency as well as less downtime due to longer service intervals ensuring very high reliability due to our high-quality standards.
The road ahead'
The Government of India has ambitious infrastructure goals. And concrete equipment has a big role to play in helping meet these targets. Given this, there is potential for further growth in the concrete equipment segment.Concludes Sakthikumar, “The future is bright. Since more focus is now on infra, road, metros, and high-speed trains, all these have huge requirements for concrete. We have inaugurated a state-of-the-art global manufacturing hub in Cheiyar – 90 km from Chennai to exceed the future demand.”
Case Study
Concrete Solution for a Challenging Project
The 180 MW run-of-the-river power facility is being constructed on the River Ravi in Chamba, which is located in the Holi Bajoli village in Himachal Pradesh. The construction of the Rs 1,765.38-crore project began in April 2013 in which, and the total civil work cost is Rs 1,005.41 crore. Bajoli Holi Hydroelectric Power Project (HEPP) is a run of river scheme harnessing the hydroelectric potential of River Ravi in its upper reaches. The project will have power and no irrigation benefits mainly, as the scope of irrigation is negligible in these areas.The project will feed power in the Northern region which comprises the states of Himachal Pradesh, Haryana, Punjab, Delhi, Uttaranchal, Uttar Pradesh and the union territories of Chandigarh and Jammu & Kashmir. The Northern region power grid includes the power system controlled by the electricity board of the above states.
Construction
Bajoli Holi HEPP has been allotted to GMR as the main contractor for project implementation and GMR has sub-contracted the civil work to Gammon India. It took 76 months to complete 80 per cent of the project and will take 12 more months for handing over the project. It has been almost five years since the construction process began and with around a year left to go, this project is on track to be completed by the end of 2020. In this Bajoli Holi HEPP, there are three phases and each phase is of 60 MW (3 x 60 MW) capacity. Also, there are six additional tunnels that are connected to the head race tunnel. Total volume of concrete poured and produced at this project site for all additional and head race tunnel's upper face is 3,12,000 cu m. Concrete grades used are M10-M50. Construction is in full swing on all fronts and dam structure works are nearing the advanced stages of completion.
B Choubey, Project Manager, Gammon India, says, “I am elated to be posted here for the completion of 180 MW hydroelectric power project, which is being developed by GMR and is a very exigent project located on River Ravi due to the rugged terrain and logistics being the biggest pitfall. With the expertise of Schwing Stetter's trusted equipment and skillful engineers, we are nearing the completion of the arduous hydroelectric power project."
Why Schwing Stetter?
Choubey says, "Among the companies in the concreting equipment field, Schwing Stetter is the best. They are providing good service and genuine spares to all of their clients and especially the very best service to the corporate clients. We get spares only from Schwing Stetter India purely because of their unmatched reliability."
Schwing Stetter equipment is known for "Built to Last" and here is the live example.
As many as 60 Schwing Stetter equipment were used out of which eight are batching plants, of which seven units are at least a decade old (older than 2007).
Rohit Sood, Mechanical Head, Gammon India, says, "In a project of national importance, there are many components and challenges involved, that make up the larger project stand significant. This isn't a simple feat and would have become impossible without Schwing Stetter India's mastery in handling the equipment.
Erection of batching plant is a challenging task in the hilly terrain mainly due to unpredictable geological conditions at the site location which include roadblocks and landslides. Shifting it from Chamba to the dam site involved a lot of expertise and of course a large, complex, unique challenge but nothing that the Schwing Stetter India's team couldn't handle."
On the reasons to partner with Schwing Stetter for the concrete solutions, Sood adds, "I have been the plant in charge of this project from day one and have been using Schwing Stetter's concreting equipment for 22 years and all that I could say about Schwing Stetter is that the products are of desired quality and we are very contented with the service. They provide continuous support and insight that is needed to navigate the equipment in rugged terrains and using them effectively across this hydroelectric project. The aftersales service is what makes Schwing Stetter unique."
“We are using CP 30 since a very long time,” says Sood. "The life of the plant and performance is exemplary and we are getting genuine spares from Schwing Stetter. In addition to this, we are operating a 2001 model M1 batching plant at the powerhouse complex which is running successfully and we have completed 4,000 cu m of concrete using this plant and the remaining 8,000 cu m of concrete is expected to be completed using this plant. We are getting superior service in this remote area and are able to complete our scheduled target on time. We have completed 312,000 cu m of concreting till now using various equipment supplied by Schwing Stetter as they have equipment suitable for structures that rise above the water and also the foundations that dive down to the ground."
On the challenges faced in the execution of the project, Sood is of the view, "There is never only one way to do anything and getting exposed to challenges, finding unrivalled alternatives and triumphing over it with the best concreting partner like Schwing Stetter is the great reward."
In this hilly terrain, shifting and erection of Stetter concrete batching plant H3N from Chamba to the dam site was a herculean task. Sood concludes, “Schwing Stetter India's engineers made it possible with their full-fledged support and now we are operating the plant successfully at the site. Schwing Stetter India has gained unbeatable reputation for the service it offers which is an integral part in making the project a flawless one. There is no doubt that we are a part of Schwing Stetter and we would always prefer to be!"