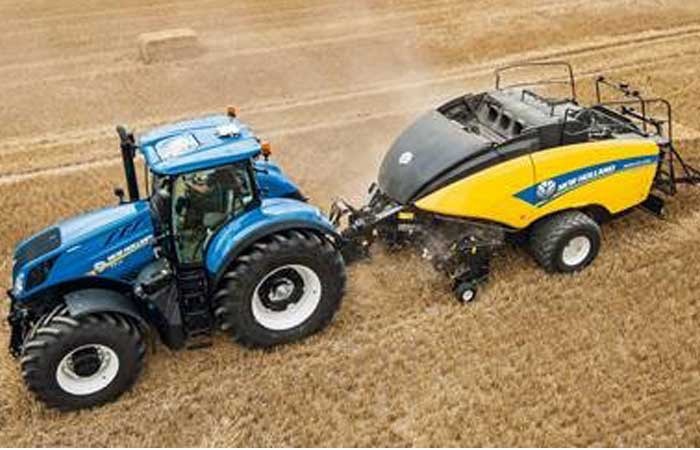
The simulation factory answers heavy equipment variability
System simulation for heavy equipment: The maturity age
System simulation appeared in the industrial world in the late 1980s using in-house codes that relied on C or Fortran languages. These codes were developed and maintained by researchers in universities or directly by industrial companies.
In the mid-1990s, the need for a simpler modeling approach increased with the understanding of system simulation power and effectiveness. This marks the birth of model authoring tools based on drag and drop like Simcenter Amesim software. Simcenter is a part of the Xcelerator portfolio, a comprehensive and integrated portfolio of software and services from Siemens Digital Industries Software. In the heavy equipment industry, Tamrok (now part of Sandvik Mining) was the first to use Simcenter Amesim to engineer its hydraulic hammer and drilling machines.
Heavy equipment suppliers and original equipment manufacturers (OEMs) understood the value of Simcenter Amesim and deployed it widely. Today, system simulation is an integral part of their process. In addition, pre- and postprocessing are tightly linked to other processes, methods and tools. System simulation value (frontloading, quick turnaround, design exploration, machine synthesis) has been demonstrated over time and is at its zenith. (From heavy equipment component design to system integration with Simcenter Amesim)
The other side of the coin is that since more and more system simulation analyses are required, the resources dedicated to running these analyses are under constant delivery pressure. Indeed, simulation engineers must deliver results for many different variants, through different projects, for different markets. On top of that, they need to gather data from many different stakeholders, suppliers and departments to feed into their models.
This creates a bottleneck for the simulation engineers, particularly in the heavy equipment industry, where the number of product lines and variants are high.
Starting from this observation, there are two solutions. The first and most straightforward one is to increase the system simulation workforce. But we live in a budget constrained world and this may not always be possible for every company.
The other alternative is to make the models usable by people who are not system simulation engineers (for example, allowing other engineers to do engineering analyses). At Siemens Digital Industries Software, this concept has a name: the simulation factory.
The simulation factory: Enabling system simulation mass deployment
To describe the system simulation factory, let’s first make an analogy with an off-road vehicle factory. To build a vehicle, we need raw materials. These raw materials are processed using machine tooling and these machines are arranged around different product or assembly lines. Once the vehicle is built it is delivered to the different customers.
Now, let’s replace the off-road vehicle with a system simulation model:
The machine tooling becomes the solver of Simcenter Amesim and its eco-system (reduced order models methodology, co-simulation, scripts)
In the next section, a part of the simulation factory is demonstrated through an agricultural tractor simulator developed in Simcenter Amesim and explored in Simcenter System Analyst.
Managing the engineering complexity of a tractor with Simcenter System Analyst
Configurability is an important aspect of agricultural equipment. Tractor usage is quite versatile and usually performs a broad range of tasks such as trailing, loading, mowing, digging, seeding and tilling. As an example, in one year a tractor OEM received orders for 7,800 different tractor configurations from its customers (Source: Bloomberg). Managing these configurations, not only from a manufacturing perspective but also from a conception perspective, is critical.
Additionally, according to a study from the Deutsche Landwirtschafts-Gesellschaft (DLG) organisation, fuel economy is the second most important criteria when purchasing a tractor.
The DLG proposes a standardised test cycle that compares the fuel efficiency of several tractors, the so-called DLG PowerMix, which is truly influential in the agricultural industry. As a result, the DLG PowerMix assessment is a must when developing a new tractor.
In this use case, we will show how Simcenter Amesim and Simcenter System Analyst can answer these two challenges during the product development phase.
While Simcenter Amesim is a system simulation solution, Simcenter System Analyst is a collaborative solution that creates industry-specific applications to drive system simulation models. Model reuse by an increased number of people helps to maximise return on investments for the model development efforts.
The starting point is a Simcenter Amesim model arranged in super components, which contain several submodels that are gathered in company libraries. The different submodels representing a system (like an after treatment system or internal combustion engine) can either represent the same variant with different modeling approaches or different configurations.
For each submodel, we defined the parameters and variables that are accessible by the Simcenter System Analyst user. These submodels can be shared across the company (and beyond) and facilitate complete tractor model assembly through standard interface contract definition.
Once the architectures and submodels are defined, they are shared through the model lifecycle management solution or locally for later use in Simcenter System Analyst. One can customise the views, filters and scripts in Simcenter System Analyst using a “view editor” that ensures a smooth connection between Simcenter Amesim submodels and architectures and the Simcenter System Analyst user experience.
The first step in Simcenter System Analyst is to select the architecture or architectures to be simulated. This is done by selecting among existing technical definitions and modifying them if needed. In our case, there are three architectures:
Once the technical definition is selected, we can still modify it before doing any analysis.
Once the technical definition is done, we can select the component and/or individual parameter set variations. In this case, we choose to modify:
This is done by using the filters to select among the different available submodels prepared in Simcenter Amesim.
The variability manager lets the user choose if they want to run a full factorial design of experiment or deselect any specific combination. When the variability is defined, the user can launch the simulations. Since the number of simulations to be run can be huge, parallel processing or high power computing (HPC) options are proposed to execute the simulations.
Conclusion
In the heavy equipment industry, the many different usages and configurations of a given machine quickly become an engineering hurdle. It is not reasonably possible to simulate every variant for every market for every product by only relying on simulation engineers. Simcenter System Analyst allows you to leverage the value of existing models by providing an easy-to-use, deskilled simulation platform for performing trade-off and optimisation studies. This also behaves as a collaborative platform which capitalises on the shared and validated simulation models and the knowledge that they contain.
Ultimately, the system and modeling simulation process is automated. Clear roles are defined to run the simulation factory. Most of the time and effort is spent on analysis simulation results rather than on creating and managing the models. This is where system simulation meets tomorrow.
Article courtesy: Siemens Digital Industries Software