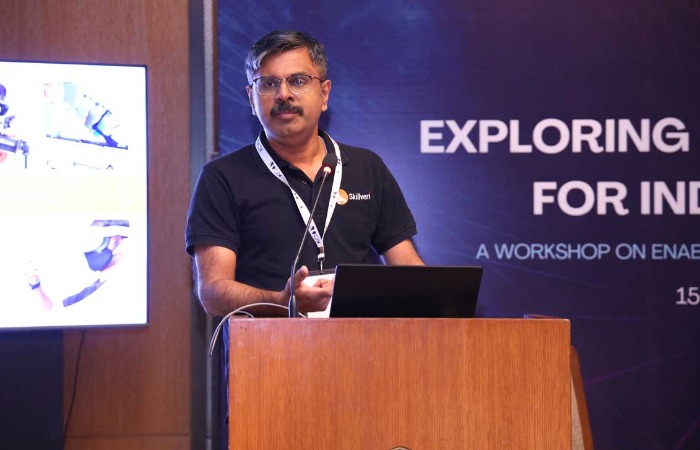
The skill level of the workers directly affects the output quality
Skillveri is the world's leading MR/XR skill training platform for welding simulators, painting simulators and other manufacturing skills. Sabarinath C Nair, CEO, Skillveri, speaks on the skill training platform that helped bridge the skill gap in sectors like construction and manufacturing.
Could you begin by telling us how Skillveri’s journey started and what inspired you to create this unique platform?
India has a huge youth population, but major infrastructure projects like the Delhi Metro and Delhi Airport were built with outsourced labourers from China and Peru. It gave us the realisation that despite there being a lot of demand for skilled labour in our industries, our youth is unable to benefit from those opportunities since there is a significant gap in both the required skill levels and awareness.
Skillveri was started with a mission to bridge this gap by providing accurate, measurable, and cost-effective training for industrial skills using state of the art technology.
Your platform has been highly impactful in industries like automotive and manufacturing. How did you identify the specific skills that needed to be addressed?
We initially began our journey when industries approached us for a reliable and effective way to train their workforce on the shopfloor. We began with welding which is the most critical skill needed across most manufacturing industries. We then realised that whatever was welded needed to be painted, and a few years down the road our spray-painting simulator was launched. We have also added other skills to our platform like HVAC/RAC repair and solar panel installation, based on the feedback from industries and based on which skills are taught by institutions like ITIs or polytechnics which provide the main source of fresh workforce for these industries.
How do you ensure that the training is both effective and accessible, especially for blue-collar workers with varying levels of experience?
The learning process with the Skillveri simulators is designed to be extremely user friendly and intuitive. It has a game-like approach instead of feeling complicated and does not need any specific educational or experience level as a prerequisite. Hence the users are more eager and interested to learn.
The learning methodology on the simulator follows a systematic step by step approach, where the learner is introduced to one parameter at a time and allows them to master that before they ‘unlock’ and move on to more complex aspects. This ensures they are not intimidated by too many things at once, and each can practice at their own pace.
The simulator also gives them live guidance on the screen during practice, and an easily understandable scoring system that points out their strengths and areas for improvement, which enables a more focused learning.
How has Skillveri’s immersive platform helped bridge the skill gap in sectors like construction and manufacturing, where precision and safety are critical?
In such sectors, the skill level of the workers directly affects the output quality. An imperfectly executed job can easily result in rejections of an entire batch or result in stoppage of conveyors etc which can run up losses in crores in a matter of hours. Skillveri simulators exactly replicate the workpieces and scenarios to give the learner a real world like feeling but eliminating any of the risks and hazards of the real-world training. Hence learners can practice with confidence in an incident free environment till they gain the perfect level of skills.
The scoring algorithm is able to accurately predict someone’s real world performance, and an industry can utilise the analytics to allocate work to people according to their dexterity levels.
Skillveri is known for customising its platform to offer training in 18 Indian languages and seven European languages. How important is localisation in vocational training, and what impact has this feature had on user engagement and adoption across diverse markets?
While the simulator does offer the flexibility of choosing from multiple languages, what really sets it apart is the interface, which has very minimal language dependency. It is important to deliver vocational training in a very easy to understand way, and we have made sure the elements like on-screen guidance, the performance analysis graphs, are all very visually easy to understand. This has made the simulator universally appealing – whether the learner is in a tier 2 or tier 3 town in India or a school or college in US or factory in Europe, they are able to quickly adapt and use it effectively with minimal external guidance. This is also a key factor which has enabled us to scale quickly and expand to global markets and find wide acceptance there.
The gap in skilled labour is an ongoing challenge, particularly in developing economies. What role does Skillveri play in improving the status of these essential careers?
The amount of young people opting for skilled trades in developing economies is largely due to lack of awareness on the career paths they can offer, as well widespread misconceptions about the work environments etc. Skillveri has always firmly believed that a formal, modern training can go a long way in addressing some of these misconceptions. When people see the skills or vocational sector getting access to the same quality of modern, technology-enabled learning that theoretical education gets, it will change their perception. We want to make skill training safe, accessible, and enable people to move from odd jobs in informal workplaces to stable career paths in the formal manufacturing sector. This will unlock opportunities and transform their livelihoods in the long term.
With the rise of automation and AI, what future innovations do you foresee for Skillveri’s platform in helping workers stay ahead in the ever-evolving world of manufacturing and construction?
AI, when integrated with technology like VR/XR, has the potential to enhance training outcomes on multiple aspects. It can be used to analyse individual learning patterns, and optimise the training to suit their pace, strengths and weakness.
At Skillveri, we are also working on ways to leverage the potential of AI to help industries plan the processes for new product lines, which will be critical to them. We plan to map the skillsets and performance patterns of the current workforce of an existing organisation, and provide industries with valuable data on the kinds of errors that are likely to occur, which areas in the new process would need more training, etc. This will result in a lot of time and cost savings in training and optimise efficiency.