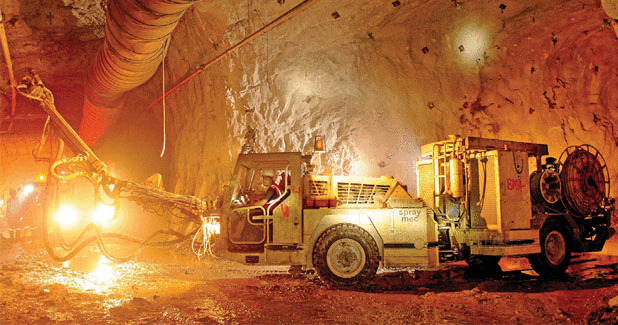
Transforming Mining Safe and Productive
Underground mining is an extremely tough mining method with various risk factors involved. But the evolution of digital technologies and automation, and the technologically advanced equipment are transforming the underground mining operations safe and productive. <p></p><p> With mines are going deeper and minerals on the earth surface depleting faster, underground mining is the option to mine the huge deposits of minerals and coal hidden deep under the earth. However, it is a daunting task to go deep under the earth and mine the minerals. While certain minerals like zinc and copper are mined using underground mining methods, high grade coal is mined from the deep, by underground mining method. Since the coal deposits in the earth surface are fast exhausting, coal miners in future will have to depend on the coal deposits deep underground." </p><p> Underground mining in India The Indian mining sector contributes around 3 per cent of the GDP. According to <span style="font-weight: bold;">Kush Tandon, Commercial Manager, Underground Mining - India, Caterpillar Global Mining, India</span> hosts underground metal mines as well as underground coal mines. 'The geology of metallic mineral ore bodies differs greatly from the bedded seams of coal. </p><p> As a result, the methods and machines to mine metal ores differ entirely from those used to mine coal underground," he explains. Major minerals mined through underground mining in India are zinc, silver, copper, gold, manganese, chromite and uranium. All major underground metal mining companies are bracing for challenges such as rapid increase in production with mechanisation and cost reduction. </p><p>Exploration is being carried out at various locations in the country to identify new mineral reserves. There is an increasing trend of continuous mining mechanisation in coal mining by adopting continuous miners in underground coal. </p><p>Hindustan Zinc (HZL) and Hindustan Copper (HCL) are the two major players in underground mining in India. According to recent reports, the government-owned HCL is planning to re-open its closed mines and expand existing ones in its quest to increase ore production five times from the current level of 4.1 million tonne per annum (mtpa) by 2025. The company, which is also keen on bagging new mines, is expected to spend around Rs 60 billion in this endeavour. HZL, a subsidiary of Vedanta Resources, plans to invest Rs 80 billion in the next 3-5 years to expand its operations and capacity. The company aims to take the existing ore production levels of 9.36 mtpa to 14 mtpa and finished metal production to 1.10 mtpa from 0.85 mtpa. </p><p> <span style="font-weight: bold;">Risk factors</span><br />Once a decision has been made to go underground, the specific mining method is selected depending on the size, shape, and orientation of the ore body, the grade of mineralisation, the strength of the rock materials, and the depths involved. As one goes deeper into the earth, the thickness and, consequently, weight of the overlying rock increase. Pressure from the sides also increases with depth; the amount of this pressure depends on the rock type and the geologic situation. In the world's deepest mines, which are more than 4 km below the surface, pressure becomes so intense that the rock literally explodes. These rock bursts are major limitations to mining at depth. </p><p>"Complexities in underground mining are somewhat different compared to surface mining methods. These challenges emanate from inherent geology and rock conditions. Also, space restrictions, ventilation, lighting, supporting roof and safety issues arising from man machine interface are other challenges," explains <span style="font-weight: bold;">Shib Bhowmik, Managing Director, Komatsu Mining Corp, India.</span> </p><p> <span style="font-weight: bold;">Technology to mitigate risks</span><br />Technology improves safety and productivity. With the help of digital and IoT-based technologies, safety risks can be minimised and the overall productivity of mining underground can be improved. Anirban Sen, Business Line Manager- Underground Rock Excavation, Epiroc Mining India, says,"Underground mining involves high risks, but we can see the trend to mitigate risks and also investing in modern machinery giving high importance to safety and productivity." </p><p>According to <span style="font-weight: bold;">Sunil Duggal, CEO, Hindustan Zinc</span>, the need of the hour is not just mining, but mining with better safety, cost and in a sustainable manner. Rightly, underground mines in India are focused on increased use of technology and skill upgradation to adapt technologies to increase efficiency and productivity, and minimising the cost to gain competitive advantage. </p><p> <span style="font-weight: bold;">Market outlook</span><br />Major underground mining players are looking for expanding operations and increase production in the coming years due to an expected demand growth for metals like copper, zinc, lead etc in the coming years. Sen elaborates, "The projected demand of copper due to electric vehicles is expected to increase by 1.7 mt by 2027. With 0.66 mt of refined copper consumption in 2017-18 and the current consumption growth rate at 6-8 per cent and the additional demand of 1.7 mt from copper-intensive electric vehicles, the total demand for copper is projected at 2.6-2.7 mt by 2023-24." </p><p>According to him, the industry estimates suggest 5-6 per cent annual demand growth for zinc in the coming years. "For lead, growth in automobile sector is the major driving factor. Around 75 per cent of the lead consumed in India is accounted by the lead battery segment. According to the second Automotive Mission Plan 2016-26 (AMP 20126), the Indian automotive industry is expected to grow to $300 billion by 2026, thus driving the demand for lead in the country," adds Sen. </p><p>According to Duggal, the underground operation in India is on the verge of transition from the conventional to the autonomous operation. "In the near future, there will be hardly any deposits left near surface and hence the underground operation shall become more prominent. The future depends on how well we are prepared to address the deeper mining challenges," he concludes. </p><p>In spite of the high risk and investment involved, underground mining can become safe and productive with the help of modern technologies and proper utilisation of the equipment and technologies. </p><p> <span style="font-weight: bold;">EQUIPMENT USED IN UNDERGROUND METAL MINING</span><br /></p><ul><li>Development: Single and double boom drill jumbo </li><li>Production: Long-hole production drills</li><li>Loaders: Load-haul dumpers - diesel/electric/battery </li><li>Trucks: Low profile dump trucks - diesel/electric/battery</li><li>Bolters: Cable and bolters machines</li><li>Raise boring machines</li><li>Ventilation system </li><li>Shotcrete machines </li></ul><p> <span style="font-weight: bold;">CHALLENGES IN UNDERGROUND MINING</span><br /></p><p><span style="font-weight: bold;">Global factors: </span>Over the last one year, the international market has witnessed a downward pressure in the commodities prices due to rising supply from major producers and moderating demand from China due to its stringent environment policy measure. This has impacted the bottom lines of mining companies, thereby leading to limited investment undertaken by them.</p><p><span style="font-weight: bold;">Risk and uncertain geological complexity: </span>The very nature of mineral exploration has a high proportion of unforeseen challenges and complexities. The reserve in place may be established, but the economic feasibility of mining can vary significantly. This, in turn, makes the outlook for a given mining project uncertain and complex.</p><p><span style="font-weight: bold;">Huge potential untapped due to regulatory logjams:</span> One of the biggest challenges is the lack of co-ordination among various government entities associated with the mining industry. </p><p><span style="font-weight: bold;">Local agitations:</span> Local communities often protest against exploration activities that fear a loss of livelihood as a result. </p><p><span style="font-weight: bold;">-Anirban Sen, Business Line Manager - Underground Rock Excavation, Epiroc Mining India.</span></p><p> <span style="font-weight: bold;">MINING INTELLIGENCE AND ASSET OPTIMISATION FROM EPIROC</span><br />From a cost-effective deployment and reuse of the existing datacom infrastructure, Mobilaris can deliver a Mining Intelligence Solution that:<br /></p><ul><li>Increases the overall production efficiency between 10-20 per cent</li><li>Lowers operational costs</li><li>Increases the personal safety in underground mines</li><li>Delivers position data and decision support to other existing mine automation applications</li><li>By connecting machines with Certiq the whole global fleet can be monitored.</li><li>The data is communicated via Mobile network, Satellite, Wi-Fi or whatever available.</li><li>All data is then processed in our central server and made available to all users.</li><li>The customer can access the data on the web portal, via sms, reports or integrated into their ERP system.</li><li>Automation: Automation concept contains four levels of automation. From data monitoring and product function control, to calculated optimisation and in the end, full autonomy. Combining all steps allows you to reach the full potential of Epiroc's equipment. When the machines work together, they can perform very complicated tasks, deep underground. And they can do so with minimal downtime and maximum safety.</li></ul><p><span style="font-weight: bold;">NEW DEVELOPMENTS</span><br />Hindustan Zinc and Hindustan Copper have planned expansion and new projects. <br />Hindustan Zinc:<br />Rampura Agucha underground mine - plans 5 mtpa of ore production<br />Zawar mega mine complex - ore production capacity expansion from 4 mtpa to 8 <br />mtpa<br />Hindustan Copper:<br />Expansion of Sudra mine from <br />0.4 mtpa to 0.9 mtpa<br />Chapri - Sideshwar mine (new mine) - 1.5 mtpa </p><p><br /></p>