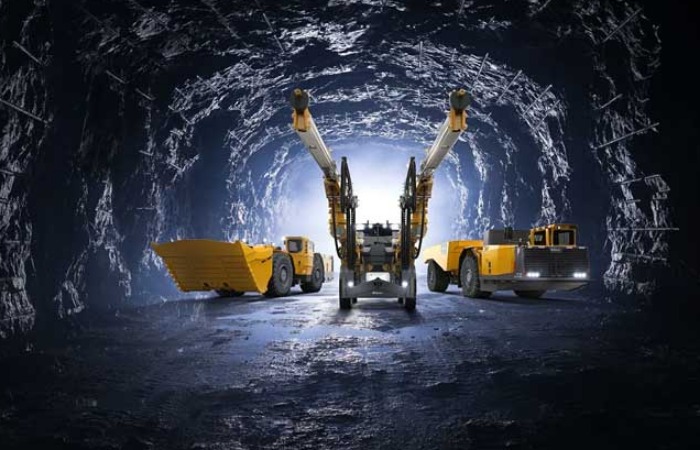
Unearthing Potential
The government plans to introduce a Production Linked Incentive (PLI) scheme for underground mining machinery and heavy earth-moving equipment by 2025-26. This initiative, spanning five years, aims to enhance the largely untapped underground coal mining sector in India.
Currently, Coal India (CIL) imports high-capacity machinery, including electric rope shovels, hydraulic shovels, dump trucks, crawler dozers, drills, motor graders, and wheel dozers for its operations. These assets, valued at Rs 3,500 crore, incur an additional Rs 1,000 crore in customs duties. To mitigate imports and promote domestic manufacturing, CIL has outlined a strategic plan to gradually eliminate these imports over the next six years.
The government anticipates that coal will remain the primary energy source well beyond 2030, driven by increasing power demands, and therefore projects a significant need for equipment for both opencast and underground mines in the upcoming decade. CIL has begun acquiring advanced heavy earth movers and continuous miners equipped for remote operation and real-time tracking to boost efficiency and safety.
The government also emphasized the importance of forming partnerships with leading global equipment manufacturers. It seeks to promote the use of domestically manufactured machinery in coal production, transportation, and monitoring, ensuring that productivity is not compromised.
This initiative is expected to minimize the downtime associated with imported equipment, which frequently becomes inoperative due to unavailable spare parts. This will be achieved by producing key components such as engines, transmission systems, differentials, and motors while implementing duty restrictions on the necessary parts.
Says Rajesh Nath, Managing Director, VDMA India, “Mining would continue to play an important role in India. In actuality, mining accounts for 4 per cent to 5 per cent of our total GDP. Around 60 to 65 per cent of India’s electricity still comes from coal. By 2025, the Ministry of Coal wants to expand coal production from its current level of 740 to 750 million tonne to one billion tonne. India is still one of the few nations in the world where mining is still a major industry. Because of this, even German businesses are optimistic about India.”
Yashvardhan Bajla, Director – Business Development, Taurian MPS, says, “The mining industry is experiencing trends like increased demand for efficiency and digitalisation. There’s a push toward electrification to reduce emissions, requiring equipment that’s both powerful and eco-friendly. Taurian addresses these needs with its Terratrak hybrid track-mounted units that offer efficient, emission-free operation. These crushers meet the industry’s demand for reduced environmental impact while also reducing operational costs by up to 80 per cent.”
Digitalisation in mining
Automation is a key element of Industry 4.0, delivering benefits to multiple industries in terms of safety, efficiency, and productivity. Automated drilling rigs, drones, and hauling trucks are just some examples of automated and remote-controlled machinery that are seeing increased adoption in the modern underground mine, replacing human miners that have traditionally been the backbone of the industry.
Autonomous mining equipment, such as dozers, drilling rigs, load-haul dump machines (LUDs), excavators, and trucks, is outfitted with advanced software, sensors, and robotic components. Features of these machines include semi-autonomous and fully autonomous operation, proximity detection, and fleet tracking.
Several companies have entered the race to develop fully autonomous mining equipment. Rio Tinto, for instance, is employing autonomous drilling systems at its mines in Australia. With this technology, a single operator can simultaneously control four autonomous rigs, improving safety and reducing labour costs while promoting better efficiency and productivity.
Remote-operated vehicles such as drones are being used for safety inspections and exploring mines, collecting raw data, which mine planners can use when situated a safe distance from the mine. They can also be used for blast engineering and stockpile inventory monitoring tasks.
Cat MineStar Edge is Caterpillar’s cutting-edge cloud-based, subscription managed application that creates an operational ecosystem that gives our customers near-real-time visibility to every aspect of their operation. It allows them to efficiently execute their mine plan and deliver optimal quality to the plant and to the surface. Cat MineStar Edge makes it possible to measure, manage, analyse, and optimise its customers entire operations. The interesting point about the solution is that it is OEM agnostic.
Cat MineStar Edge solution doesn’t require extensive infrastructure expenditure from the business makes it an attractive value proposition for our customers. Being a cloud-based solution, it just requires minimum hardware installations to function with any existing infrastructure. With this, data points such as fuel consumption, payload, asset utilisation, etc. are immediately posted into the cloud device, allowing the mine operator or mine owner to monitor how effectively the asset is being used.
Said Bajla, “Taurian washing systems recently introduced the CycloFrac, which showcases significant technological advancements in ultra-fines filtration. The system employs advanced cyclone technology to recover particles as fine as 75 microns (200 meshes); ensuring valuable materials are not lost. High-frequency dewatering screens reduce moisture content, enhancing product quality and processing efficiency. An integrated water management system recycles up to 90 per cent of process water, promoting sustainability and reducing operational costs. The system can be used for highly specialised application like frac sand, silica sand, iron ore recovery, etc.”
Says Prasanta Ganguly, Head – OTR Marketing (Domestic Sales), BKT Tires, “BKT has introduced several innovations in tyre design for the mining sector, particularly in all-steel radial tyres. Our latest radial OTR tyres are engineered to provide enhanced durability, better load distribution, and longer service life. We’ve also incorporated smart tyre technology that allows for real-time monitoring of tyre health, enabling operators to track pressure, temperature, and wear levels. These advancements help reduce downtime, optimise performance, and improve safety in mining operations.”
BKT sets itself apart through a combination of advanced technology, customisation, and unmatched customer support. Our all-steel radial tyres are engineered to meet the toughest conditions, offering superior durability and performance. Adds Ganguly, “We also pride ourselves on customising tyre solutions to fit the specific needs of each mining site, ensuring optimal performance and longevity. Our commitment to sustainability, innovation, and customer-centric service further strengthens our position as a leader in the mining tyre sector.”
Said MT Swamy, General Manager – Sales, Kennametal, “Kennametal is an over 80-year-old company that offers material science expertise and strong manufacturing capabilities. It provides solutions for various industries, with a focus on improving productivity and reducing downtime for customers. Our tools, materials and wear-resistant solutions enable customers to run longer, cut faster and machine with greater precision.”
Kennametal operates in the road rehabilitation, surface mining, underground mining, foundation drilling, and trenching applications within the construction industry. Kennametal believes that the market for urban infrastructure development in India will be robust for the next decade due to the governments focus on improving infrastructure such as roads, metro trains, ports, airports, and bridges.
Sandvik continue to add solutions to help the digitalisation in mining. A complete digital platform for optimised operations, from planning to execution, is the latest addition.
An increasing number of mines have already incorporated the use of OptiMine, a comprehensive suite of digital solutions for analysing and optimising mining production and processes underground. For several years mines around the world have made use of fully autonomous mining equipment from Sandvik, such as underground trucks and loaders. The first AutoMine automation system Opens in new window was developed and delivered in 2004. To help the industry obtain the benefits of digitalisation, Sandvik is continually upgrading its offerings. An exciting new product to be rolled out in 2022 is a collision-avoidance system developed by the Newtrax business unit. The acquisition of Australian software company Deswik Opens in new window, a top-tier supplier of mine planning software, supports digitalisation throughout the mining value chain.
The mining industry is increasingly adopting digitisation. Sensors, big data, Artificial Intelligence, digital twins, and many Industry 4.0 technologies are being implemented to improve monitoring, exploration, data analytics, predictive maintenance, and worker safety. The mine of the future will become a smarter more interconnected, data-driven environment.
Predictive maintenance is a key trend in the mining industry, made possible by increasing digitization and data analytics and the development of smart sensors, AI, and machine learning. Vast amounts of data from multiple points can be retrieved, analysed, and used to action maintenance tasks, reducing downtime and improving productivity while improving safety.
“There needs to be a conscious endeavour to reduce the carbon intensity by the public and private sectors such as the direct reduced iron (DRI) electric arc furnace (EAF) IF route, which is expected to become dominant over the years,” says Amit Bhargava, Partner & National Head - Mining & Metals, KPMG India, highlighting strategies to align with carbon reduction targets. “Further, the steel scrap requirement is projected to double by 2030. Several promising technologies are under evaluation, including COREX with an oxygen converter for direct and automatic use of export gas for power generation, COURSE 50 for highly efficient CO2 separation and recovery from blast furnace exhaust gas, and Volteron, a first-of-its-kind iron reduction and steel processing route that produces iron via direct electrolysis, expected to be operational by 2027.”
Said Tridib Majumder, Managing Director, Quaker Houghton India, “The products we have in the metals industry contribute to reducing friction, energy savings and improving finish primarily in cold rolling of flat steel products. We have rust-preventives to ensure there is no corrosion after the steel is rolled. For the benefit of both steel and non-ferrous customers, Quaker Houghton continuously improves our products and develops novel solutions. For the Transportation OEMs, we have fluids that go into improving process efficiency once steel or iron is used to build a vehicle car, 2-wheeler, 3-wheeler bus, or truck. We have fire-resistant hydraulic fluids for the mining segment. There are numerous hydrocarbon gases in subterranean mines which have a tendency of catching fire. This can cause the entire equipment to be destroyed or damaged in the fire.”
Said Vivek Misra, Associate Vice President, Business Excellence and Transformation, Smartchem Technologies, “We produce technical ammonium nitrate in the mining chemicals industry, which is used to make explosives. These explosives are then used in the blasting of various minerals, such as coal, limestone, and iron ore, as well as in other infrastructure-related areas. Power generation also makes use of ammonium nitrate. By supplying infrastructure and energy, our two business sectors help the country flourish. We concur with the PM’s goal of an Atmanirbhar Bharat. In order to support these efforts, we are attempting to expand our capabilities.”
SIT S.p.A. is the leader in the design and production of a vast and complete range of couplings that include rigid couplings, flexible couplings, zero backlash couplings, toothed couplings, couplings with shaft, bellows and disc couplings or to the clients own design. Said Amit Nangre, Executive Director, SIT PTC India, The technical complexity of what we offer from the catalogue gives it uniqueness. We promise to supply the customer with everything that is listed in the catalogue. Since our company has been in operation for 200 years, the couplings we produce have been put to the test for that entire time. The product must be excellent and benefit the customer if it is still on the market.
He adds, “Currently, the market is huge for our products. We don’t offer a whole selection of products in India. As a product, the coupling has over Rs 100 crore in sales across all categories, types, and capacities. Our aim In India is to acquire a major market share. We are closely working with many OEMs to understand their requirements and give them a proper solution.”
Miner safety
Miner safety is a critical concern as deep underground mines are hazardous environments that are hard to reach if there is a disaster. Several new technologies have appeared to improve miner safety in recent years, taking advantage of innovative developments in wearable technologies, sensors, and advanced monitoring systems.
The underground mining equipment market in India has been experiencing growth due to increasing demand for minerals and the expansion of mining operations. Overall, the outlook for the underground mining equipment market in India remains positive, driven by these trends and the ongoing demand for various minerals.
Underground mining techniques include blast mining, room and pillar mining, block caving, retreat mining, drift and fill mining, cut and fill mining, longwall mining, shrinkage stope mining, and sublevel caving. Explosives are used in blast mining to remove complex rock layers, loosen rocks, and open up underground mining sites. Room and pillar mining entails building rectangular pillars to support the weight of the ceiling while miners extract minerals from around the pillars.
Specialised underground mining machinery may perform this approach. Removing the pillars from the room and pillar mining is known as retreat mining. This method strategically removes the pillars, allowing the remaining ore to be extracted from the mine. The mine collapses in on itself as the pillars are removed. It is an extremely risky underground mining procedure, and the pillar removal process is meticulously planned to avoid injury and death.
Block caving is a large-scale mining method that takes more time to develop than any other underground mining method. Cut and fill mining is a small-scale technique involving horizontal cuts in the orebody. When an orebody is wider than the drift, drift and fill mining is performed. Longwall mining is a type of coal mining that uses a shearer mounted on a kilometre-long track to crush coal off the mine face.