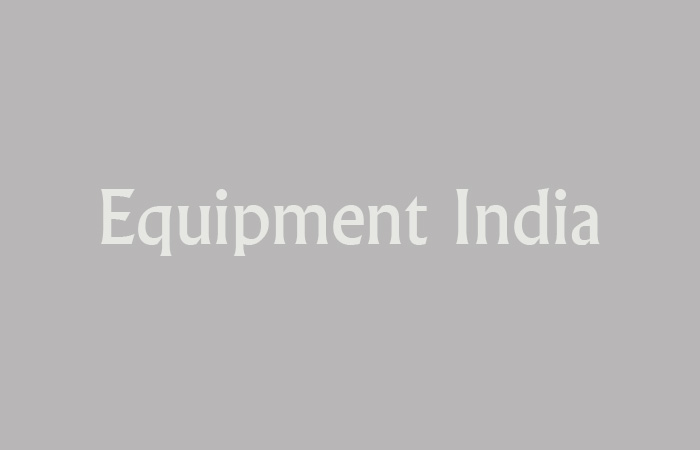
Upgrading foundries to meet OEM needs
In 2011-12, about 4,500 Indian foundries produced about 10 million tonne. However, of these 4,500, we estimate that over 75 per cent are manual foundries. Of the balance 25 per cent, a significant majority uses semi-automatic technologies, and less than 150 foundries use the latest global technologies, namely the high pressure moulding lines. As a trend, we have seen the move from manual to semi-automatic solutions and from there, to high pressure moulding lines. This trend is only getting further reinforced in spite of the current slowdown in the markets.
Competitive pressure from Chinese foundries, coupled with severe labour shortage for manual/semi-automatic foundries, is now driving a continuous demand for upgrading of foundry technology and equipment. With the Chinese competitive pressure already in India at some major OEMs, it is now a matter of survival for Indian foundries as the old manual and semi-manual technologies are the sure prescription to suicidal margin pressures and eventual failure.
In order to stay ahead of the business, upgradation is required at a foundry to feed the requirement of OEM - the customer. Customers are the driver of a business and it is imperative to provide them with the best suitable solution. Domestic manufacturers should be able to face challenges posed by global competitors or exit the market.
What OEMs look from foundries are right quality and quantity at the right time? This should be coupled with and an optimum price and minimum inventory at the customer's end.
For upgrading small and medium foundries, key drivers include:
- High capital costs
- Limited access to high-end solutions
- Local OEM support
- Environment
- Power constraints
- Labour availability
- High demand
- Total solution support
- Safety
- Lower operating costs
- New avenues
- Low rejection
- On time delivery
As such, the foundries have to make themselves more attractive and competitive for their customers for continuous business growth. Technology upgradation is the only way for this. In order to ensure growth and development of the industry, DISA India has been reaching out to various manual and small foundry belts across India to increase awareness and need of upgrading foundries. This year, DISA conducted three symposiums across India: Howrah, Rajkot and Agra, and plans to conduct more symposiums in other foundry zones.
Case study
The foundry average production of castings ranges from 50 to 250 tonne per month per foundry in Agra. Agra is an important market for the foundry industry in India. Though majority of the foundries in Agra are manual (more than 90 per cent) they cater to almost all types of castings like household castings, generator parts, pumps, sanitary, automotive, etc. These castings are mainly for domestic usage and some of the castings are exported as well. Taj Mahal, one of the wonders of the world is situated at Agra and this poses environmental restrictions to the foundries situated in and around Agra. Most foundries melt cupola with natural gas to meet their foundry requirements and in recent times, a few foundries upgraded to induction process to optimise properties of the metal.
The problems faced by foundrymen in Agra include:
- Taj Mahal corridor restrictions - environment related issues.
- Availability of local skilled manpower.
- Migrant labour issues.
- Power availability.
- Casting quality/weight variations.
- Cost of production (due to high rejections).
- Not able to attract new generation skilled talents.
- Not able to explore new market/segments.
DISA India offers conventional simultaneous jolt-squeeze moulding machine to fully automatic high pressure moulding lines (HPML). DISA India offers complete foundry solutions from the state-of-the-art manufacturing facilities situated near Bengaluru. This facilitates an advantage to the customers to get world-class technology offered locally in Indian currency. The table given above highlights the various solutions from DISA for emerging markets such as Agra.
R&D at DISA
R&D is the key activity for DISA India to bring forth best technology and products to customers. Being the leader in the industry, customers expect the best and ongoing R&D gives a competitive edge over the competition. DISA being a pioneer in this industry also focuses on various application services to ensure perfect castings for customers. The sales and support team are also available round the clock ensuring easy reach for timely supply of spare parts and services.