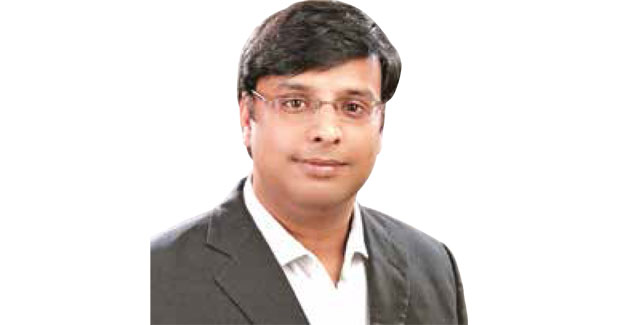
We plan to launch more centres in south and west of India
Could you brief us on ThinkLink? and its activities?
ThinkLink is the leading voice in India for the re-imagination of supply chains in a connected and on-demand business environment.We work through our Supply Chain Engineering, Material Handling Automation, and Supply Chain Talent Assurance teams to create outsized value for our clients. We do this through integrated solution delivery on an outcome-based approach that leads to a win-win shared risk partnership model with our customers.
ThinkLink Learning, subsidiary of ThinkLink SCS, was set up in 2011 to create management and operational capacity in supply chain through executive education, talent development, and skill enhancement initiatives under the brand called ?Praguna? which stands for ?efficient?.
There are two kind of programmes run under Praguna, one solely focuses on creating specialised skilled operatives (through Praguna centres), and the other focuses on creating and nurturing young graduates for roles of first line supervisors and managers (supply chain hub centres) catering to the demands of the logistics and supply chain industry at large. We also plan to work with clients on an interesting model (called Praguna Plus) where the workforce is deployed at clients? site on our payrolls with a minimum agreed commitment on their quality, productivity, availability and uptime.
What has been the response to your initiative on the best forklift operator in India? Could you also brief us on the procedures and how you ensure the maximum number of participants?
We launched the competition at India Warehousing Show in Delhi on July 1 this year, and response to this event has been very encouraging. Leading names in the industry have shown great appreciation and interest in being a part of this initiative. ThinkLink along with RTITB will utilise their combined industry outreach through a host of marketing mediums including but not limited to direct mailers, press releases, digital media marketing and print media.
How do you assess the ?skilling? of people in the construction equipment and logistics space?
We have a deep belief that there is waste in the Indian supply chain ecosystem and a large part of this comes from zero focus on skills and career development of operators and first line manager/supervisors - the people who actually get things done. In fact, people are rarely professionally trained, and even when they are, quality of training is either antiquated or abstract in nature.
What are the major challenges and how do you address those challenges?
Firstly, the mindset needs to change, skilling should longer be treated as a cost but as an investment, that will pay off itself and more in a medium to long term. Secondly, skilling in logistics space has been loosely structured and unstandardised. Therefore, there is no good way to train and assess quality of training/skilling. Moreover, the associated infrastructure and systems are also not in place.
We aim to change all these and more with our initiative ?Praguna?, where we are striving for high quality standardised training and quantifiable results through our programme offerings in state-of-the-art training centres across India.
Brief us on the facilities created in India, and your future plans.
Our first centre in India is located in Dharuhera, Haryana (around 50 km from Gurgaon on NH-8) and is a 26,000 sq ft simulated warehouse environment for practical hands-on learning experience. This facility has a state-of-the-art and well-equipped practical area as well as classrooms to facilitate effective training delivery.
Currently, we run programmes for training as Lift Truck Operators and Warehouse Associates - focused on e-commerce out of this centre, and in the near future, we aim to launch programmes on commercial vehicle driving, handling of hazardous materials, manufacturing logistics etc. We also plan to launch more centres in south and west of India in the next one year.
How do you evaluate the effectiveness of the trained people? Will there be further training for them to enhance the skills?
We have a scientific process of assessment in place, whereby the evaluation is not a one-time activity but is a continuous process during the course of the training. The evaluation is a combination of written examinations, practical tests and oral examination that happen in the course of the training and at the end of the training as well. Only after a candidate is able to clear all assessment criteria, we declare him ?Certified?.
After training gets over, the trained people are evaluated on parameters including but not limited to machine downtime, productivity, machine maintenance cost, inventory damage costs etc, and their performance pre- and post-training are compared. Further training: After a specific duration (three years) the candidate needs to reappear and undergo through a fresher training. This is to ensure that his/her skills are still up to the mark and whatever gaps might have crept in his/her work style and knowledge are appropriately taken care of.
Moreover, some programmes have graduations in the levels of training, and in those cases, a candidate who wants to move from one level to the other has to go through a ?conversion course?.
What is the current demand-supply scenario of forklift operators for logistics including ports?
There are estimated 100,000 forklifts in India, and around 8,000-10,000 new forklifts are added to this number every year. Given the lack of proper skilling and training initiatives in the country, most people either learn the machine on the job or go through loosely structured/unstandardised programmes. On the basis our study, there is a huge gap between supply and demand of trained professional forklift operators in the country.
What are the selection criteria for training? Will there be specific training for advanced forklifts?
For novice candidates looking to get trained on forklifts, we require them to be 18 years of age, in possession of a valid four-wheeler driving licence and to clear our eligibility tests (aptitude + medical). While existing operators need to pass a ?theoretical and a practical assessment? proving their skills/experience on forklifts. Currently under the lift truck training programme, we are providing training on a counterbalance lift truck (forklift) and a reach truck. Very soon, we plan to include stackers and articulated forklifts and other advanced lift truck under the available training programmes.
To what extent the training that you impart can help enhance productivity?
Our approach to training is a bit different; we focus on two of the most important aspect of operations - safety and productivity. Historically, both these have been thought to be mutually exclusive, but we firmly believe these go hand-in-hand. Not all areas of training are quantifiable, but for the areas that are, we do commit on a minimum improvement. For example, in areas like uptime, maintenance cost and productivity, useful life of equipment/battery/tyres to name a few.