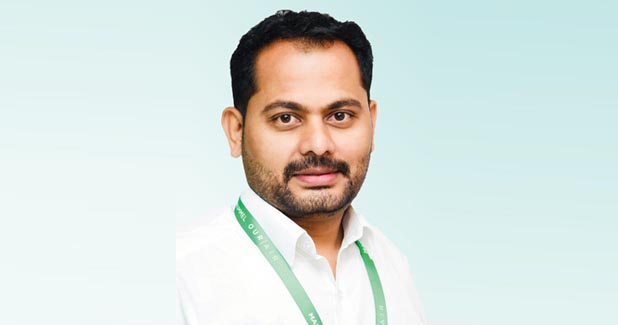
We take advantage of IoT at every opportunity
Mann and Hummel offers end-to-end filtration solutions for construction and mining equipment. <span style="font-weight: bold;">Antomon Rapheal, Director-R&D Engineering - OE, Mann and Hummel Filter,</span> explains more on the market opportunity and products and solutions. <p></p><p> What are the different types of filters used in construction and mining equipment?<br />The products manufactured by the Mann and Hummel group include air cleaner systems, intake manifold systems, liquid filter systems, plastic components, filter media, cabin filters, industrial filters and membrane filters.</p><p> The filters used in construction and mining machines have to consistently perform well. Mann and Hummel offers end-to-end solutions for these segments that include air cleaners, oil filters, hydraulic filters, fuel filters, crankcase ventilation, cooling water compensation tanks, cabin filters, air and oil separator elements, spark erosion filters and other technical performance parts under the hood. Large volume of dust and enormous mechanical loads place filtration systems under a lot of pressure. </p><p>The different filter systems in an engine or hydraulic systems have to filter the operating materials such as air, fuel and oil. Filters in OE matching quality provide the best possible protection for the machines; they reduce machine downtimes and make sure that the machine users are complying with the prescribed service intervals of the machine manufacturer. Long machine running times and optimum protection are not only good for the machine but also for the budget of the machine user. </p><p><span style="font-weight: bold;">How important are filters for providing better fuel efficiency and productivity in an equipment?</span><br />Without clean fuel, there can be no clean combustion - a maxim which never been more relevant than it is today. The more complex the design of diesel engines and their injection systems, the more sensitively they react to fuel contaminants such as particles or water. Fuel filters protect all the components of the injection system. Super-fine nozzles, high pressures and cycle times lasting only a few milliseconds - modern engine injection systems are highly intricate and require particularly clean fuel. Even particles of dirt measuring as little as 15 micrometre (five times narrower than a human hair) or the smallest amounts of water in diesel can reduce the engine's performance, particularly in the case of modern common-rail systems. Fuel consumption and wear increase and, in the worst case, there is a danger of costly damage to the injection system.</p><p><span style="font-weight: bold;">How are you gearing up to meet the latest emission norms? What are the new developments?</span><br />Efficient filtration systems can help manufacturers meet stringent emission regulations requirements, be it fuel filters, engine oil filters or air filters. The packaging of filters is becoming a constraint since vehicles are getting more complex with the addition of various sub-systems, in order to meet the current emission regulations. Other than these constraints, there are a lot of technological advancements to our filtration products in order to meet new emission norms. As an example, the latest emission standards in India will require the sulphur content in diesel fuel to drop to 10 ppm from the existing 50 ppm. In order to maintain the lubricity on the fuel, additives are combined with the fuel, which do not allow the water content in diesel to be separated easily. This poses a key challenge in the separation of small water particles that are up to 10 microns in size. Mann and Hummel has come up with a patented three-stage water separation filter for diesel fuels, which is currently being proposed to a number of Indian OEMs. Similarly, we introduced many new series of air cleaner systems to ensure consistent mass air throughput, which is very critical to maintain combustion performance.</p><p> <span style="font-weight: bold;">What are the new filtration products and solutions from Mann and Hummel for construction and mining equipment? </span><br />Many newer machines in the industry are built with technologically advanced engines that require a different level of maintenance than older ones in terms of productivity or ownership costs. These engines are designed with high-pressure common-rail fuel systems. Fuel cleanliness is critical with high-pressure common-rail fuel system. Other important aspect is the consistency in delivering the air mass information for the engine control unit (ECU) to balance and deliver the correct fuel mass to the engine. New range of products are designed and validated to meet these new challenges.</p><p>In the view of highly efficient non-stop operations, with alert functions and automatic cleaning systems are now at demand, especially on the construction and mining applications. Hence, we take advantage of Internet of Things (IoT) at every opportunity even predicting and correlating the lifetime of filtration products under various operating conditions. IoT provides actionable information from equipment to your location of choice - including an office computer, laptop or mobile device and can significantly reduce the time involved in the data-collection process that triggers preventive or corrective maintenance. </p><p> <span style="font-weight: bold;">How do you offer filters for applications in varying geological, climatic and environmental conditions? </span><br />A wide range of filtration solutions, filter materials, and optional accessories are used in order to meet the filtration needs of equipment operating in various geological, climatic and environmental conditions in India. </p><p>In the construction and mining machinery, uninterrupted performance is the goal while ensuring engine life to its maximum. To accomplish this, inlet air must always be optimally conditioned. Especially, for inlet air filtration in areas with high dust levels, our new range of air cleaners provide high performance with their compact and robust construction. The use of high-quality filter materials for dust removal leads to long service life, low pressure loss, and very good separation performance. We have developed completely new filter solutions in the area of fluid filtration to meet the increased requirements for cleanliness of components and media. For example, a new series of three-stage fuel filters optimised by application - for the highest purity requirements with filter performance that has never before been achieved.</p><p> <span style="font-weight: bold;">What are your future plans on product development and market expansion in India?</span><br />Mann and Hummel initiated its R&D set-up in India in 2007 in order to generate new innovative products in a globally organised and standardised network of R&D locations close to the customer, and working efficiently and fast according to the market requirements. By now, this set-up has more than 200 R&D engineers and established with state-of-the-art validation set-up in India, includes specialised equipment and test benches to incorporate real-world properties such as filtration efficiency/performance, vibration, cyclic flow pulses, thermal cycling and more in par with global standards. These test benches bring tests closer to the actual vehicle operational environment in order to provide efficient solutions and to protect equipment in the long run. </p><p>The Indian market for construction and mining machinery offers attractive growth potential. As a result, quick market launches of new products could be realised; thanks to the state-of the-art R&D facility established at Bengaluru together with high-end manufacturing facilities and logistics set-ups at multiple locations in India. Mann and Hummel focuses on launching standard and customised products in the Indian market, with German filtration technology.</p><p> <span style="font-weight: bold;">How is the market for hydraulic filters progressing? What are the growth prospects?</span><br />Rapidly increasing production and infrastructure projects across sub-continent is leading to rising demand for filtration solutions and major factors propelling growth of the hydraulic filter market. The market for hydraulic filtration is growing consistently in the past and is expected to grow further in the coming years. Mann and Hummel has definite plans to expand further with hydraulic filtration portfolio in order to be a single solution provider for entire filtration needs of OEMs.</p>