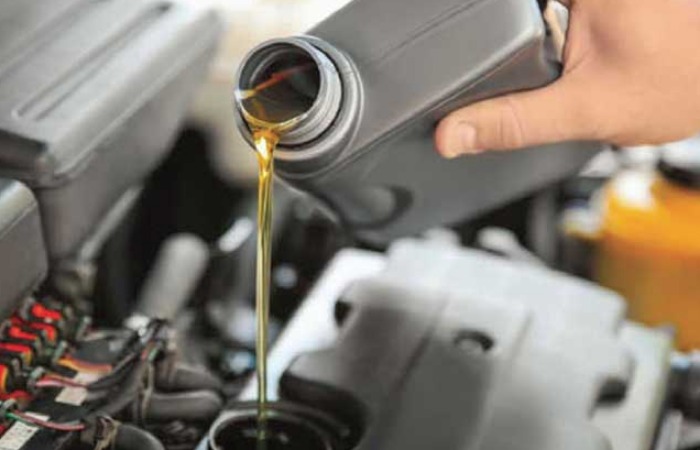
Why proper lubrication is essential for construction equipment
Lubricants play a vital role in construction. The equipment needs to perform under severe conditions, from heavy loads and extreme temperatures, to excessive wear and dirt and water contamination. Such challenges mean it is essential to provide optimal protection.
Since construction operations often move frequently from location to location, a maintenance team will not always be nearby. Machine breakdown can lead to long unplanned downtime and unexpected costs, which all equipment owners and operators hope to avoid.
Choosing the right lubricant is essential in helping to improve reliability, boost productivity and reduce the frequency of breakdowns. It’s important to consider what factors will impact whether a lubricant will be effective for its intended purpose. With engine oils, some of the key considerations are viscosity grade and performance attributes.
Lubricants are available in different Society of Automotive Engineers (SAE) viscosity grades, which dictate the acceptable temperature range in which they can perform optimally.
According to the engine oil viscosity classification, the W ("winter") following a SAE viscosity grade indicates that the oil is suitable for use in and provides protection in colder temperatures. For construction equipment working in warmer conditions, a heavier grade oil may be more suitable. These oils are often better suited for higher operating temperatures by ensuring adequate lubricant flow and the subsequent protection of critical engine components.
Viscosity changes based on temperature are vital to take note of, particularly for equipment operating in colder conditions where it may be sitting idle for considerable periods. The thicker the oil, the harder it is for it to flow around the engine; in some cases, this can leave internal hardware without the protection it needs. This increases wear rates and can lead to increased maintenance costs and unplanned downtime.
Oxidation and Aeration
Another consideration is the lubricants’ ability to resist thermal and oxidative breakdown. When lubricants are exposed to oxygen and certain metals or compounds at high temperatures, they can be prone to oxidation. Oxidation can have detrimental consequences, such as increased oil viscosity, formation of corrosive acids and sludge buildup.
Improved aeration control is also particularly important for off-highway engines due to the potential for more air than usual to become entrained within the oil. At the bearings, this can prove dangerous as these components need an oil film to protect them. Entrained air is detrimental as it interferes with boundary lubrication, or the thin oil film that protects against metal-to-metal contact.
Consultation
When selecting lubricants, it’s crucial to consult the equipment manual to confirm the viscosity recommended for the engine and if the warranty will be affected by the lubricant.
For further support or advice, consult the OEM directly or speak with a member of the technical service team from lubricant suppliers such as Petro-Canada Lubricants. It’s important to get expert advice specific to your equipment’s operation, and for recommendations to be based on test result data and extensive industry experience. This can ensure the correct oil is used to improve the reliability and efficiency of your equipment.
- Darryl Purificati is OEM technical liaison, Petro-Canada Lubricants