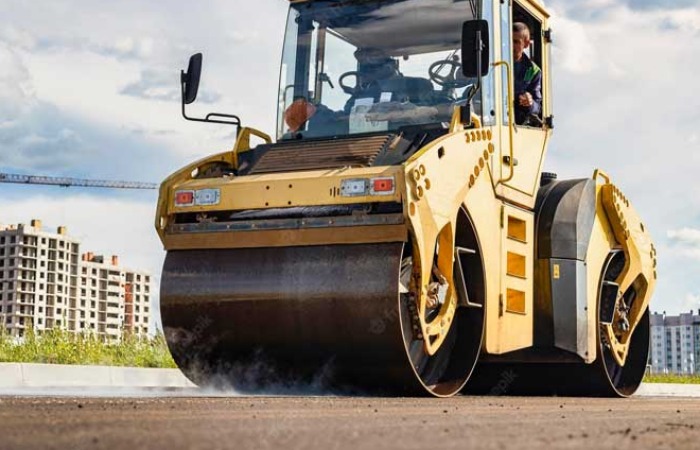
Vision 2030 Drives Growth
A report by Off-Highway Research reveals that 99 per cent of compaction equipment demand in India is met through local production, with imports accounting for only 1 per cent in 2021. The extensive infrastructure plans, especially in the road sector, will continue to drive the compaction equipment market for years, despite an anticipated 8 per cent decline in demand in 2022 due to reduced road laying activities, the implementation of CEV-IV emission norms, and high commodity prices. However, the market is expected to rebound, reaching 5,000 units by 2026.
The introduction of CEV-IV emission regulations for tyred construction equipment in India has impacted machine costs, which have risen by 5 to 7 per cent this year. Additionally, increased commodity prices and inflation have contributed to higher running costs, primarily due to elevated fuel expenses.
Despite these challenges, the report emphasises the substantial amount of work remaining in the road sector, necessitating large volumes of equipment. The industrys growth is contingent on the governments effectiveness in facilitating project execution and addressing key impediments.
The compaction equipment industry in the Asia Pacific and the Middle East is experiencing dominance due to rapid infrastructure development in countries like India, China, Indonesia, Kuwait, and Qatar. These regions witness numerous engineering and building projects, with governmental organisations focusing on organised facilities in healthcare, transportation, and tourism.
Manufacturers are responding to the growing competition by releasing compaction machine types that are fuel-efficient and require minimal upkeep. They are tailoring machines to suit Indian working conditions, with a focus on performance and productivity maximisation as key concerns for manufacturers of compaction equipment.
Ground-breaking tech
Investments in compaction equipment and related products are primarily directed towards the APAC and MEA regions, where numerous infrastructure development projects are currently underway. The focus on structured facilities like hospitals, transportation, and tourism by government bodies in developing economies has significantly contributed to the growth of the compaction equipment market.
Various companies have introduced new models or upgraded existing ones with advanced features, particularly in soil and asphalt compactors. CASE India, for example, has incorporated in-built safety features and fuel efficiency in all its equipment. Additionally, the introduction of Eagle-Eye telematics, a GPS-tracking system, enhances machine safety by providing remote diagnosis alerts. The Compaction Meter, another innovative feature, analyzes soil density and acts as a defense mechanism against unseen compaction issues.
Case's compactor range and road equipment boast smart features, including the Eagle Eye telematics system for real-time monitoring of performance, security, and efficiency. The soil compactors offer excellent maneuverability with features such as a 15° drum oscillating angle, 37° steering angle, and a short steering radius. The 1107 Ex compactor, equipped with a 4-pins central joint, ensures reliability in harsh conditions and includes safety handrails for operator convenience. The machines also feature the renowned FPT Industrial engine for faster response time and better fuel economy.
The increasing adoption of telematics, driven by stringent government mandates and consumer preference for connected vehicles, is a notable trend. Telematics aids in reducing operating costs for heavy-duty vehicles, and manufacturers in the soil compaction machines market are offering service contracts and extended warranties. Leading players like John Deere and Volvo have introduced machine monitoring services to align with this trend. This shift towards advanced telematics is expected to gain momentum in the soil compaction machines market in the foreseeable future.
JCB's compactor lineup includes the JCB116 soil compactor, the VMT860 tandem roller, and the VMT330 smaller 3T category tandem roller. Designed exclusively to meet road construction needs, JCB Road Solutions offer a comprehensive range with unique features and a robust structure. Whether a single drum soil compactor or a vibratory tandem road roller, every JCB Compactor prioritises efficiency and productivity, catering to various compaction work volumes.
He added, We are offering L&T DigiEye as an optional fitment on the L&T compactors. This digital technology helps in tracking the equipment performance, fuel consumed and machine location. The use of telematics by end-users is slowly catching up, but still, actual utilisation is low. Many fleet owners feel the need to monitor the machines remotely. In the CEV-IV compliant machines, this option of L&T DigiEye is offered. compaction meters is another concept that is offered on L&T soil compactors and this helps the operator in knowing if the desired levels of compaction have been achieved.
L&T Construction & Mining Machinery reached a milestone in the supply of indigenous equipment with the successful delivery of the 3000th L&T compactor. The roll out of this 3000th machine reinforces LTCELs leadership in manufacturing indigenously-designed equipment and paves the way for fulfilment of Atmanirbhar Bharat mission launched by the Government of India. L&T has been successful in exporting these compactors to SAARC and African countries as well. L&T compactors, launched in 2017, have fast penetrated the Indian market and are a preferred choice of customers given their excellent quality and reliability.
To accelerate infrastructure development as well as implement execution and holistic planning to improve logistics efficiency, the government announced the Gati Shakti- National Master Plan in 2021. The focus on infrastructure continued in 2021-22 too. However, the CE industry contracted by 11 per cent mainly due to the impact of change in emission norms for wheeled construction equipment to CEV4, said BKR Prasad, Head “ Marketing and Product Development, Tata Hitachi Construction Machinery.
Vogele has been the industry pioneer for asphalt pavers. It can pave from 1.5 m paving width to a maximum of 16 m. Several innovations like the pressure bars and electric heating of the screed, Niveltronic plus operating concept and ergo plus operator features have been introduced. Hamm compactors are equipped with an isolated operator platform mounted on shock absorbers so that the vibrations are reduced. The operator platform is with antiskid material to ensure operator safety. The engine compartment is closed with FRP hood in Hamm compactors, which reduces the noise levels. ROPS/FOPS requirement is currently not mandatory as per Indian regulations however it can be provided as an option.
Said Himanshu Sharma, Head “ Marketing & Corporate Communication, B&R Industrial Automation, The current innovative trends in this industry are exponentially high, looking at the new buy out strategies and the development of newer machines, changing the old-fashioned way of equipment and inculcating innovations to it, it is very clear the industry is boosting high. Also, the construction sites have newer projects, developments seen in industrial sector of manufacturing construction equipment has given new dimensions in manufacturing and in turn the upliftment of urbanisation is rapidly changing the face of the city. It is seen as per recent reports that the growth of the earthmoving equipment market will significantly contribute to the growth of the construction machinery market, which is expected to increase exponentially in coming years. Thus, as the consumer demand is increasing there has been a significant uplift of market size too.
Safety in Selecting Compaction Equipment
The top priority in road building is crew member safety. But conventional compaction equipment is about as inflexible as it gets. Operators sweat down the sloping road shoulders and ditches, risking a rollover but praying for the best as they feel every degree of slope. Although rollover protective structures (ROPS), seatbelts, and personal protective equipment (PPE) like hard helmets have been demonstrated to be effective at saving lives in compactor rollover accidents, they are not very effective for averting a disaster altogether.
Some manufacturers are redesigning the compaction process from the ground up in order to overcome the main challenges posed by conventional compaction rollers, including risk, excessive maintenance, and limited utility. When considering a new compaction roller, here is what to look for.
Manufacturers' perception that the compaction drum is a source of motion, compaction, and stability all in one has been the main barrier to compaction safety. On the other hand, the safety concern is quickly resolved by moving the drum to an offset arm attachment. The compaction roller can now be linked to graders, compact track loaders, wheel loaders, or skid steers as an accessory. These hosts offer a separate source of power for the compaction drum as well as stability and operator safety due to the offset arm.
With this configuration, an operator is now able to compact level areas as well as run the host machine on flat ground while the arm extends to the farthest, steepest edge of sloping road shoulders and ditches. Improving safety to this extent puts a major dent in workers comp claims, lowers insurance premiums, and increases safety ratings ” a necessity to contractors bidding on competitive jobs.
Shifting the drum to an offset arm attachment drastically improves safety, but it can also unlock a host of other benefits.
The onboard engine, transmission, and other connected equipment are no longer present because the compaction roller is now an independent device. Look for an attachment that offers a universal mounting pad and straightforward hydraulic connections for a smooth setup and disconnect to the host machine to further save downtime.
Think about remote-controlled possibilities as well. The operator can make all adjustments from the palm of their hand and without leaving the host machine's cockpit using certain compaction roller attachments that can be quickly attached to the remote.
Typically, aside from a handful of grease fittings to maintain and clean off debris, compaction roller attachments have no maintenance to speak of ” no more oil changes, filters, transmission fluid or any hard parts to wear and break. This can make for 90 per cent less maintenance over self-propelled machines. Cutting out the unnecessary bulk seen with traditional compaction machines also allows manufacturers to design a more compact, versatile machine.
Compaction roller attachments can easily surpass their conventional equivalents in every way during a busy roadwork season. These attachments prevent an engine from lying idle and progressively deteriorating into a surprise repair charge when the next season comes along. But more crucially, offset-designed compaction roller attachments boost crew safety and offer a multipurpose piece of machinery that will outlast any conventional compaction machine in a road crews fleet. Customers may buy with confidence knowing that they will receive the best possible return on their investment.
Road ahead
Despite recent challenges for construction equipment manufacturers, the industry remains optimistic. Intense competition compels manufacturers to innovate, and the entrance of global leaders is a positive development, bringing the latest technology to the market. Established players in the Indian market are poised to strengthen their positions in the coming years by introducing newer models. Increased collaboration between construction equipment manufacturers and rental fleet owners ensures that products are tailored to meet customer needs. Despite competition concerns, the global recovery trend instills confidence in investors, leading to continued optimism and the expectation of new investments entering the field. Key players in the compactor market include JCB India, Wirtgen, Hamm, Volvo CE, Escort, Case Construction, Ammann, Atlas Copco, and others.
The compaction equipment market is around 4,000 machines annually.
The market is anticipated to flourish at a healthy CAGR of 6.4 per cent between 2023 and 2033.
The market growth will depend on the speed of execution of the road projects.
Despite the promising trends, the compaction equipment market in India faces several challenges that need to be addressed for sustained growth.
High initial costs: The capital-intensive nature of compaction equipment poses a significant barrier for small and medium-sized construction companies. The high initial costs of purchasing advanced compaction machinery often deter potential buyers, hindering the widespread adoption of modern technologies.
Limited awareness and training: A lack of awareness and training on the benefits and operation of advanced compaction equipment is a challenge in the Indian market. Many construction professionals may not be fully aware of the latest technological developments or the potential efficiency gains associated with automated compaction. Bridging this knowledge gap is crucial for the successful integration of advanced equipment.
Infrastructure and connectivity issues: Remote monitoring and control systems heavily rely on robust internet connectivity. In many construction sites across India, especially in rural or remote areas, inadequate infrastructure and connectivity pose challenges for the effective implementation of automated and remote-controlled compaction equipment.
Environmental regulations: While there is a growing demand for eco-friendly equipment, stringent environmental regulations can pose challenges for manufacturers. Adhering to emission standards and sustainable manufacturing practices adds complexity to the production process, potentially affecting the cost and availability of compaction equipment.